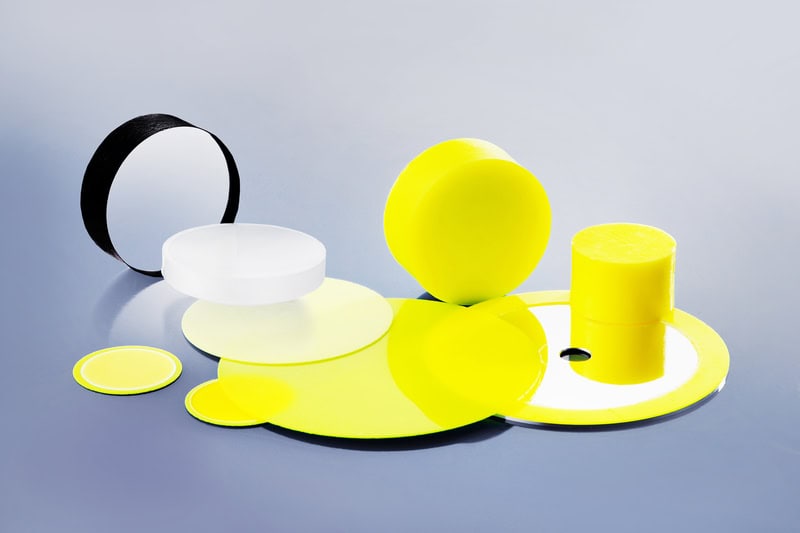
There is increasing interest in the use of transparent and translucent ceramics, but much of the work in this field has been done in developing proof-of-concept and small-run products. The interest is driven in large part because ceramic-based optical components would have several property and manufacturing advantages over their glass counterparts. A big thing that has been holding back the use of ceramics is the perfection of large-scale production techniques, but now Schott Research and Development says in a news release that it has laid important foundations on manufacturing optical ceramics in a reproducible manner.
Although Schott is largely associated with glass R&D and manufacturing, the company entered into a special joint project funded by Germany’s Ministry of Education and Research (BMBF) called “OptokeraMat.” To be a little more precise, OptokeraMat falls under a BMBF initiative begun in 2007, “Materials Innovations for Industry and Society” (WING). According to its webpage, WING is described as
[T]he first program to integrate traditional materials research with the basic discipline of chemistry and with nanotechnology. Besides combining basic research and applied materials research with the aim of accelerating the transfer of results, the new program also takes account of technology-driven changes in market conditions. The materials manufacturers have often only a minor share in the eventual high value creation with the component or system produced although they have covered most of the cost for research and development. Furthermore, the market needs ever-smaller amounts of ever more specialized materials such as functional or layered materials. The increasing specialization of materials therefore requires increasing cooperation. Only R&D collaborations enable small and medium-sized companies to occupy profitable market niches.
OptokeraMat, one of those collaborations, has been a three-and-a-half-year effort begun in 2009. The basic benefits of ceramic optical components are that they have high IR and UV transmission, high refractive indices, are chemically stable, can be easily and reliably doped and can be made relatively efficiently. German public and business officials wisely realized that they have a tremendous potential in nearly all optical applications (future markets related to lens, scintillators and LEDs are particularly attractive) and launched OptokeraMat to gain a foothold for the nation in this burgeoning R&D field.
Besides Schott, a partial list of participants in OptokeraMat includes Perkin Elmer, Braunschweig University of Technology, IBU-tec, B&M Optik, Ceramtec, and the University of Erlangen.
With the collaboration now coming to an end, Schott is says they have accomplished much of what OptokeraMat set out to do. In the company’s release, Yvonne Menke, materials development manager for Schott Research and Development, says “We have now succeeded in meeting the long-held wishes of the optical industry for a new transparent material for use in photography and other types of imaging devices. And we are paving the way for highly-efficient LED systems.”
One of the most significant achievements claimed is that the collaborators succeeded in developing methods to manufacture and reproduce ceramic sintered parts for optical and fluorescent applications.
With reproducible optical ceramics, Schott says engineers can now exploit the superior thermal and mechanical qualities, the high optical refractive indexes (some greater than 2), improved dispersion properties, and the ability to create gradient materials. “This opens up new areas in the Abbe diagram, which systematically depicts the properties of optical materials, which glass was never able to address before. In other words, optic designers now have a larger toolbox to work with,” explains Volker Hagemann, senior scientist at Schott.
According to the company, here are the implications: Camera lenses can be smaller and contain fewer color defects and aberrations. In addition, the lenses will enable new classes of cameras used for geo-observations that could be used on Earth and in space in searches for raw material deposits.
For energy efficiency and lighting applications, Schott predicts a new era when engineers will use ceramic materials for color conversion use with LEDs. Typically, part of the light from blue LEDs must be converted to white for commercial lighting. Schott says in the release that the current color conversion materials are “not nearly as heat resistant as a fluorescent ceramic manufactured at temperatures in excess of 1,600°C. In combination with high-intensity LEDs or laser diodes, the outstanding temperature stability and thermal conductivity of these ceramic converters allow for new light sources to be developed. Their luminance is two to three times higher than that of a typical xenon burner. Areas of application include beamers, next-generation digital projectors and headlights.”
One application area I am curious about that Schott didn’t address in its release is the medical scintillation market, including uses in Computed Tomography machinery. This is an area where GE has already made a lot of progress, but the company made it clear in a 2010 presentation (pdf) that it considered the scintillator market to have a lot a future value.
Author
Eileen De Guire
CTT Categories
- Manufacturing
- Optics