[Image above] Credit: Matt Hollingsworth; Flickr CC BY-NC-ND 2.0
[Editor’s note: This post comes to us from Erkan Gurdal, S. Tuncdemir, and C. A. Randall. Gurdal is a post-doctoral scholar and lead scientist of this project at the Center for Dielectrics and Piezoelectrics at the Materials Research Institute at Pennsylvania State University (University Park, Pa.). Randall is a Professor of Materials Science and Engineering and the Director of the Materials Research Institute at Penn State; he is co-PI of this project. Tuncdemir is chief technological officer at Solid State Ceramics Inc. (State College, Pa.); he is PI of this project.]
By A. Erkan Gurdal, S. Tuncdemir, and C. A. Randall
Even though electronic devices have become significantly smaller in past decades, adapters for charging and supplying power to those devices have remained largely the same. So carrying these bulky, heavy, brick-like adapters has become an accepted part of our daily routines.
Adapters—technically known as power converters—have not changed simply due to the limitations of electromagnetic transformers. These are usually the heaviest and sometimes the largest component of power converters.
Electromagnetic transformers consist of a magnetic core and primary and secondary windings. Electrical energy is converted to magnetic energy in the primary winding, transferred to the secondary winding through the magnetic core, and then converted back to electrical energy in the secondary winding. Assuming the process involves no losses, voltage can be adjusted by changing the winding amount on either side of the magnetic core.
But that assumption is a big one.
Have you ever noticed your laptop gets hot after a while? That heat is due to voltage conversion taking place in a somewhat compact volume with high power/current, which causes joule heating of the windings in the electromagnetic transformer.
Joule heating is energy loss, in which some of the supplied electrical energy is lost to heat instead of converted to magnetic energy. However, not all is lost—increasing the supplied electrical power can make you forget about cold nights, because you can use that warm adapter as a convenient and compact heater.
Piezoelectricity comes from the Greek words “piezo” and “elektron” (“of amber,” referring to amber’s attractive properties), which mean “to press” and “electric,” respectively. As the etymology indicates, piezoelectricity is the conversion of mechanical energy (pressure) to electrical energy.
The Curie brothers, Pierre and Jacques, discovered piezoelectricity in experiments with Rochelle salt in the late 1800s.1 Later, Gabriel Lippman discovered the converse piezoelectric effect, which means that piezoelectric materials can also convert electrical to mechanical energy.
In addition to several natural piezoelectric materials, scientists have invented many synthetic piezoelectric materials. The most notable piezoelectric materials have ceramic perovskite structures, such as Pb(Zr,Ti)O3 (PZT) and BaTiO3 (BT).
Because piezoelectric materials can convert mechanical to electrical energy and vice versa, both conversions can be made within the material simultaneously by considering special designs. C. A. Rosen discovered piezoelectric transformers with PZT ceramics in the 1950s by designing a special electrode and polarization arrangement that could amplify the applied voltage significantly at the secondary side—called step-up.2 Accordingly, designs can also decrease voltage at the secondary side—called step-down.
Given the solid-state nature of piezoelectric transformers, their major advantage over electromagnetic transformers is high efficiency in ultra compact volumes (see comparison below).
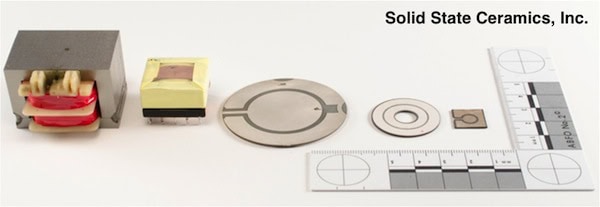
A comparison of electromagnetic transformers (left two objects) and piezoelectric transformers from the miniaturization viewpoint. Credit: Solid State Ceramics Inc.
Therefore, piezoelectric transformers have tremendous potential in electronic applications where size and weight matter, such as avionics and portable electronics.3 On the other hand, piezoelectric transformers can cost significantly more and have driving circuits that are more complicated than electromagnetic transformers.
Piezoelectric transformers require the use of hard piezoelectric ceramic materials, or hard-piezoceramics, which require high temperatures (>1200˚C) to form the ceramic structure.
Designing devices with multilayer forms, where piezoceramic and metal layers are stacked alternatively on top of each other, can maximize power (capacitance) in compact volumes. However, multilayer structures require large amounts of metal, which is mostly limited to platinum because of the high processing temperatures required for hard-piezoceramics. Because power is proportional to layer count and therefore the amount of electrode used, use of large amounts of precious metals like platinum can significantly increase production costs (see graph below).
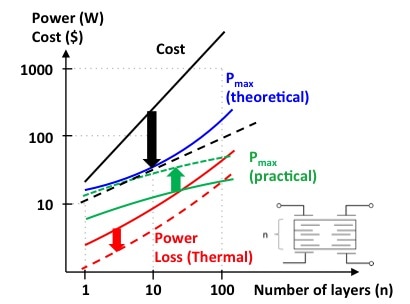
Power and cost as functions of layer count in multilayer piezoceramics.
Hence, hard-piezoceramic compositions need to be modified to lower processing (sintering) temperatures, which would allow use of cheaper and electrically- and thermally-competent precious metals or alloys—preferably base-metal electrodes, such as silver/silver–palladium and copper and nickel. Nonetheless, use of such metals in multilayer applications demands quite challenging scientific and engineering considerations.4
Hard-PZT is one of the most, if not the most, utilized hard-piezoceramic. Unfortunately, nickel is not chemically compatible with hard-PZT. However, copper seems promising considering previous results with copper co-fired multilayer piezoceramics with soft-PZT. Moreover, previous studies have investigated hard-PZT compositions with low sintering temperatures, but they were not practically applied to co-fired multilayer piezoelectric transformers.
Therefore, our research investigated how to substantially lower process temperatures for a typical hard-PZT composition. This accomplishment would allow use of: 1) less expensive electrode materials, such as silver or silver–palladium; and 2) base-metal electrodes, such as copper.
To realize these goals, we have developed modified hard-PZT piezoceramic compositions with low sintering temperatures (≤1000˚C). We demonstrated high efficiency of these materials in multilayer piezoelectric transformers with silver–palladium co-fired electrodes with low palladium content (i.e., 90/10 and 95/5).
We also investigated the feasibility of copper co-firing and prototyped copper co-fired multilayer piezoelectric transformers. Our efforts included typical multilayer prototyping for overall and ambient sintering for silver–palladium co-fired piezoelectric transformers. We used reducing-atmosphere sintering for copper co-firing feasibility investigations and copper co-fired piezoelectric transformer prototypes (see image below).
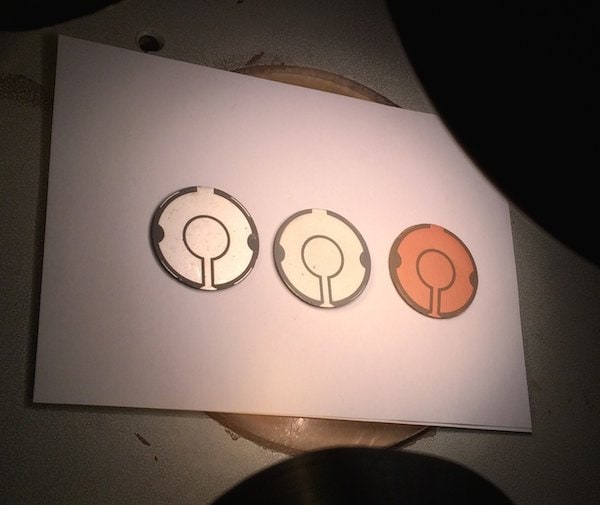
(From left to right) Multilayer piezoelectric transformers co-fired with platinum, silver–palladium (95/5), and copper electrodes.
Our results show that by employing cheaper electrode materials—specifically base-metal electrodes like copper—it is possible to significantly reduce the cost of piezoelectric transformers so that they can compete with the cheaper price of electromagnetic transformers. Moreover, initial characterizations on copper co-fired multilayer transformers show significantly improved thermal and electrical behaviors compared to other materials, which should correlate with significant improvements in device performance.
With recent improvements in piezo-driver technology, in conjunction with our developments, the tremendous potential of piezoelectric transformers can be realized in the electronics industry.
Devices that have become a part of our daily lives—remember that laptop charging brick?—can be made much lighter and more compact with this piezoelectric transformer technology. They may even become be small enough to fit into a wallet or be integrated into laptops or charging cables.
Acknowledgments
This study is based upon work supported by the National Science Foundation (Grant No. 1448918). Any opinions, findings, conclusions, or recommendations expressed in this material are those of the author(s) and do not necessarily reflect the views of the National Science Foundation.
References
1 K. Uchino, Ferroelectric Devices, 2nd Edition. CRC Press, Boca Raton, Fla., 2009.
2 C. A. Rosen, “Electromechanical Transducer”, U.S. Pat. No. 2,830,274, 1958.
3 A.V. Carazo, Piezoelectric Transformers for Space Applications. Face Electronics LC, Norfolk, Va., 2003.
4 C. A. Randall, A. Kelnberger, G. Y. Yang, R. E. Eitel, T. R. Shrout, “High strain piezoelectric multilayer actuators—A material science and engineering challenge”, J. Electroceramics, 14, 177–191 (2005).
Author
April Gocha
CTT Categories
- Electronics
- Energy
- Material Innovations