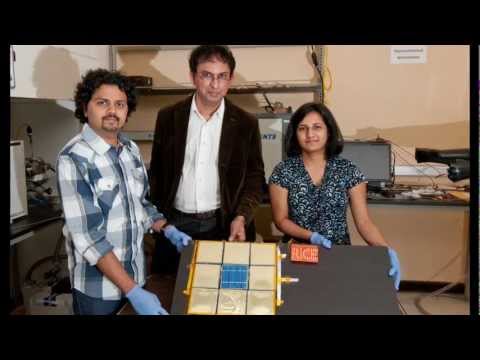
Rice University researchers have demonstrated a paint-on lithium ion battery. Credit: Rice University; YouTube.
“The more things change, the more they stay the same,” according to a 19th century French proverb.
It could not possibly have been a reference to batteries, which were invented also in the 19th century, but it does seem apropos to recent developments in battery research.
The more things change …
Rice University researchers published a new paper on an innovative approach to fabricating rechargeable lithium-ion batteries based on spray painting. The battery components are laid down in five layers: two current collectors, the cathode, the anode and a polymer separator in the middle.
The team demonstrated that the make-it-as-you-go battery could be deposited on just about any substrate including ceramic bathroom tiles, flexible polymers, glass and stainless steel. The process works on a variety of substrate geometries, too, which they demonstrated by airbrushing a battery onto a beer stein. The work was done by Pulickel Ajayan’s group. Ajayan is a professor in the Mechanical Engineering and Materials Science Department and in the Chemistry Department.
The five layers include combinations of familiar and new materials, which were dispersed in a several kinds of solvent vehicles. The first layer is the positive current collector and mixes purified single-wall carbon nanotubes and carbon black particles in N-methylpyrrolidone. The cathode is next and is a mix of lithium cobalt oxide, carbon and ultrafine graphite in a binder. The separator layer is a polymer paint composed of Kynar Flex resin, PMMA and silica in a solvent. The fourth layer is the anode and is made of a mixture of lithium titanium oxide and ultrafine graphite in a binder. The final, fifth layer is the negative current collector and is made of a commercially available copper paint diluted with ethanol.
Neelam Singh, Rice graduate student and lead author of the paper, says in a press release, “The hardest part was achieving mechanical stability, and the separator played a critical role.” The first two layers adhered well, but if the separator layer was unstable, they would peel off. Adding enough PMMA gave the separator the right amount of adhesion. After painting, the tiles were infused with electrolytes, heat-sealed and charged.
The batteries are easily charged with a small solar cell, and the team demonstrated the potential of a battery-cum-solar cell tile array. They created an array by connecting nine battery tiles in a parallel circuit. Then, a solar cell was placed over the center tile. The tile array was charged with the solar panel and house current, and held enough charge to provide a steady 2.4 volts for six hours-enough to power a small set of LEDs that spelled “RICE.”
The batteries appear to be stable. The team reports that the battery capacity was consistently within ten percent of the target, and that they lost very little charge storage capacity when subjected to 60 charge-discharge cycle tests.
The team sees the potential for the technology to have a big impact with scale-up and integration with solar panels. “Spray painting is already an industrial process, so it would be very easy to incorporate this into industry,” Singh says in the press release. She and her colleagues envision, for example, tiles that can be snapped together and configured in any number of ways, or a spray-it-yourself battery kit that could be distributed through outlets like Home Depot.
The paper is open access in Nature’s Scientific Reports. See “Paintable Batteries,” Scientific Reports, by Singh, et al. (doi: 10.1038/srep00481).
… the more they stay the same.
Meanwhile, a team at Stanford University published a paper that describes impressive improvements to the Edison battery by incorporating nanoscale forms of carbon into the electrodes.
The Edison battery was itself an innovation by master inventor, Thomas Edison. It is built with a nickel cathode and an iron anode in an alkaline solution, and was designed to be a rechargeable, inexpensive alternative to corrosive lead-acid batteries. Edison hoped it would be used to power electric automobiles, and in 1910 the potential of the technology was demonstrated in a 1,000-mile road trip. The batteries were manufactured until the mid-1970s, although some are still made today, mostly to store surplus solar- and wind-generated electricity.
Edison batteries have the advantage of being durable and made from some of the Earth’s most abundant materials, but they have the disadvantage of being slow to charge and slow to discharge.
The Stanford group, led by chemistry professor Hongjie Dai, turned to an old friend, carbon, which is often used to improve the electrical conductivity of electrodes, but this time in the form of graphene and multi-walled carbon nanotubes.
Lead author of the paper and graduate student, Hailiang Wang, says in a press release, “In conventional electrodes, people randomly mix iron and nickel materials with conductive carbon. Instead, we grew nanocrystals of iron oxide onto graphene, and nanocrystals of nickel hydroxide onto carbon nanotubes.” The result was a strong chemical bond between the metal particles and the nanoscale carbon and a consequent improvement in battery performance.
The coupling of nickel and iron particles to the carbon substrates means electrical charge can move easily and quickly between the electrodes and the external circuit. Dai says in the press release, “The result is an ultrafast version of the nickel-iron battery that’s capable of charging and discharging in seconds.”
The team developed a one-volt prototype with enough power to run a flashlight. They are optimistic that the technology can be scaled-up for use on the electrical grid or for transportation.
The improved Edison battery is not a candidate to power electric cars, because its energy density is too low, but it could provide an assist to the lithium-ion batteries that power cars like the Chevy Volt. Lithium-ion batteries have high energy density, but can take hours to charge.
Wang notes, too, that the battery could be useful in emergencies, “There may be applications for the military, for example, where you have to charge something very quickly.”
The team admits the battery is not perfect: its storage capacity decays over time, about 20 percent across 800 cycles. “That’s about the same as a lithium-ion battery. But our battery is really fast, so we’d be using it more often. Ideally, we don’t want it to decay at all,” Dai says.
Although Edison developed the original battery design, Dai says, “It’s different from traditional methods, where you simply mix materials together. I think Thomas Edison would be happy to see this progress.”
Indeed.
The paper is “An ultrafast nickel-iron battery from strongly coupled inorganic nanoparticle/nanocarbon hybrid materials,” by Wang, et al., Nature Communications (doi:10.1038/ncomms1921).
Author
Eileen De Guire
CTT Categories
- Electronics
- Energy
- Material Innovations
- Nanomaterials