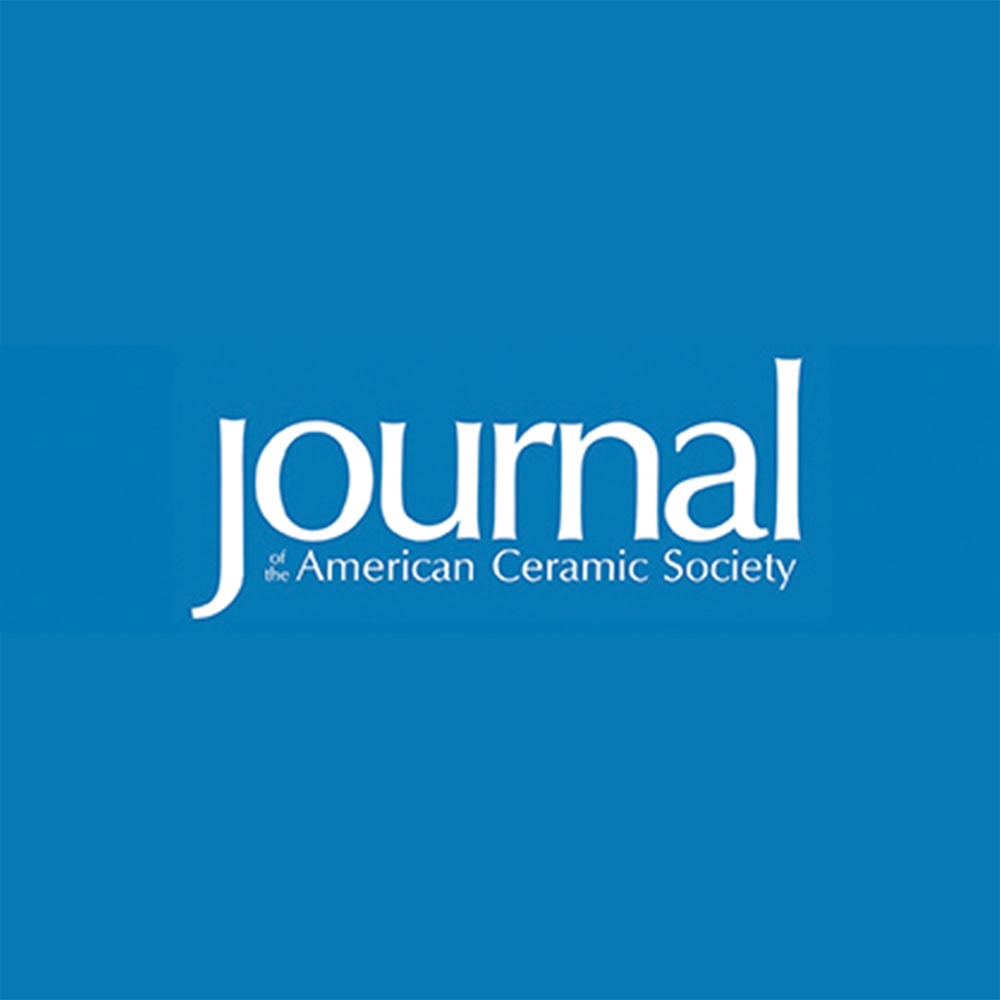
JACerS Articles
Journal of the American Ceramic Society (JACerS) is a leading ceramic science and engineering journal.
Submit Your Manuscript
Establish accounts on these services and associate your articles and reviews with them to begin your journey as a JACerS author and reviewer.
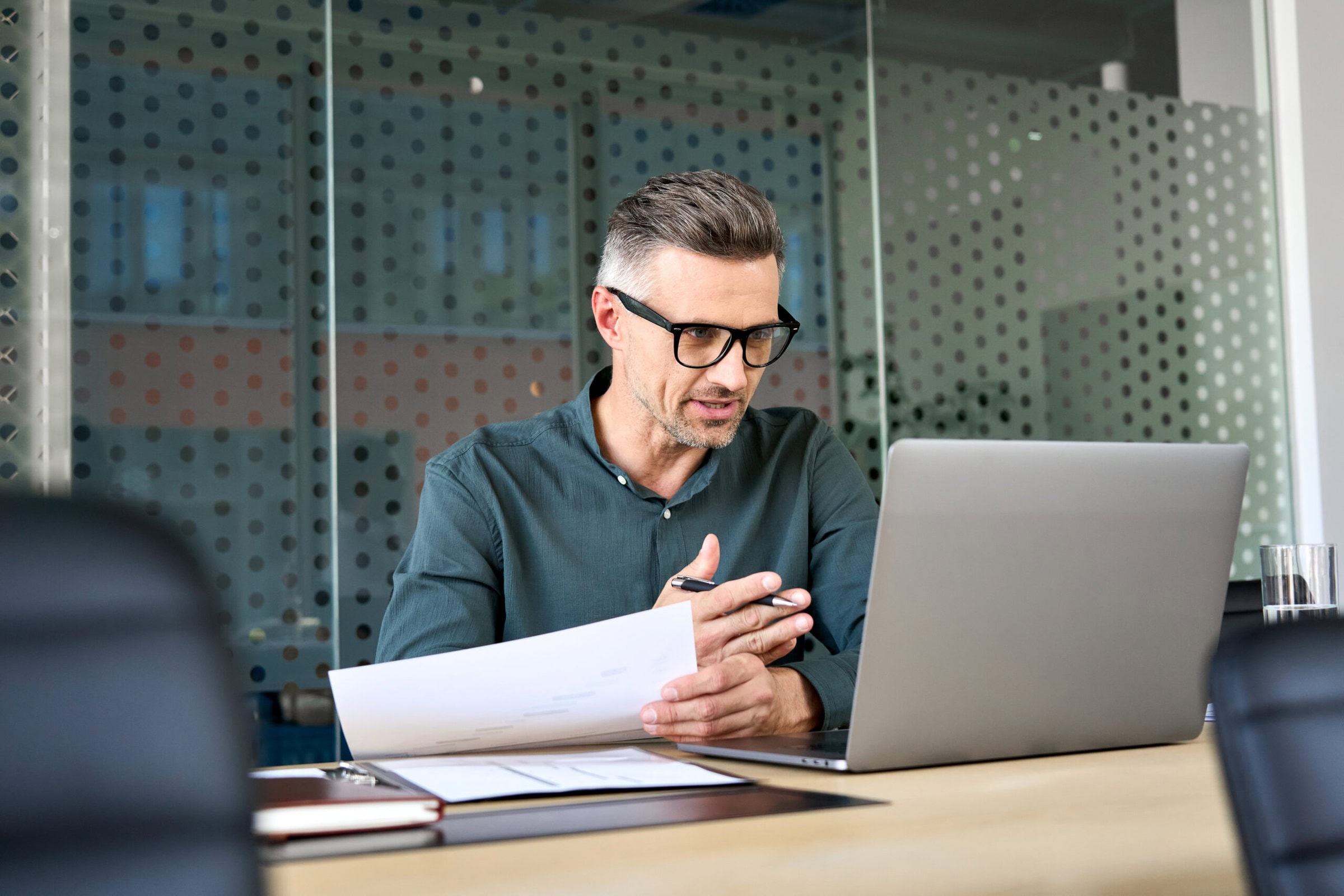
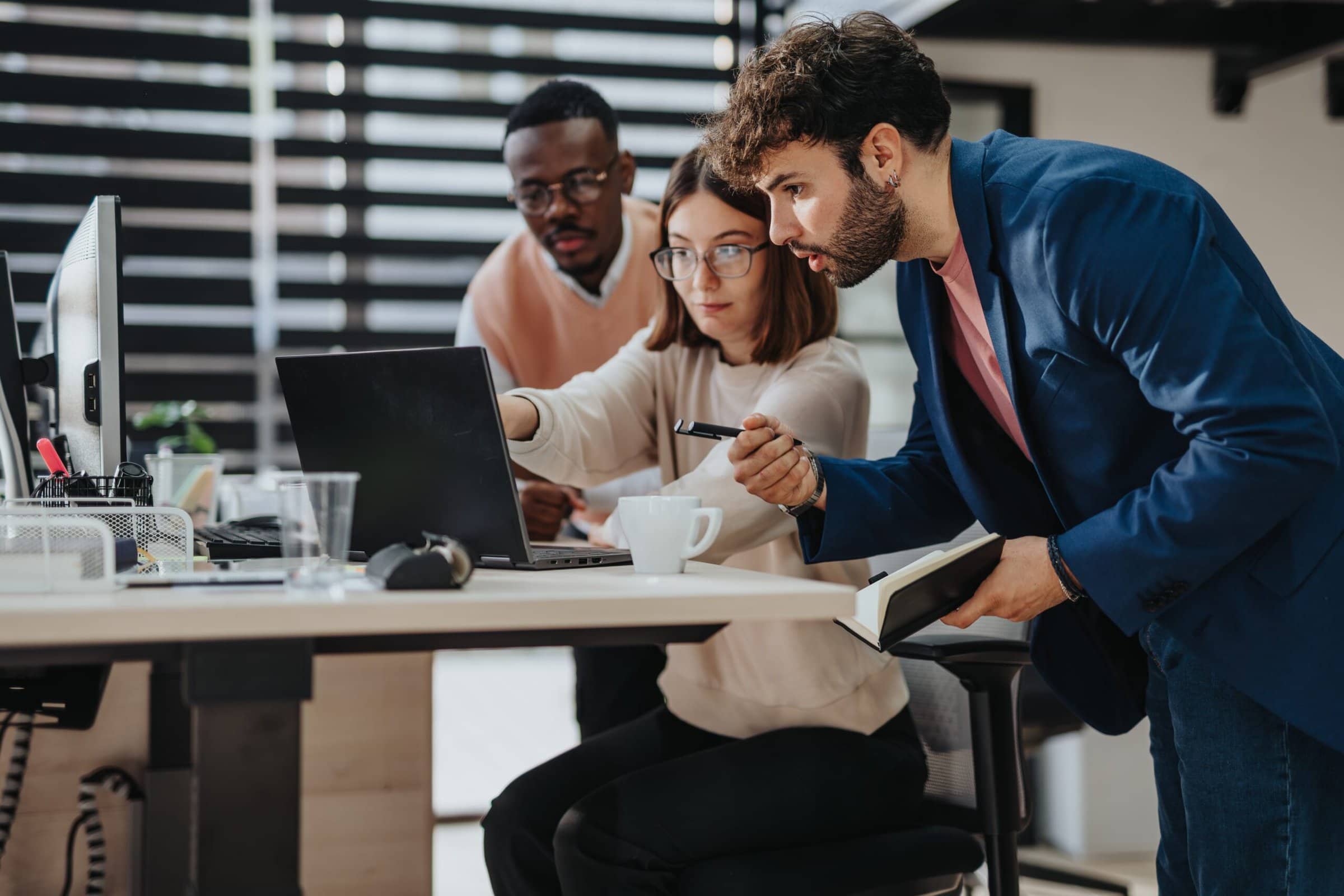
Editor’s Choice Articles
The Editor-in-Chief recommends these outstanding articles.
2nd Century Trailblazers Initiative now accepting new submissions
As the Journal of the American Ceramic Society continues into its next 100 years, we remain committed to bringing to light the impactful work of researchers, both established and emerging. In line with this goal, we are reinitiating our very successful 2nd Century Trailblazers Initiative. This initiative aims to promote excellent work by early career researchers. Over 40 outstanding articles were published in the inaugural JACerS 2nd Century Trailblazers special issue.
Accepted articles will be published in a new special collection of the Journal in 2026. Authors of the outstanding articles recognized by the JACerS Editors will be invited to present their work at the 2026 MS&T meeting,
More information is available here.
Click here to submit your manuscript, Submissions are due by 30-September-2025.
Please let us know you intend to submit a manuscript by filling out this form.
2nd Century Trailblazer Reservation
Special issues for 2025-2026
The editors have ambitious plans for these special issues:
- Materials Inspired By Nature, which highlights bioactive, biomimetic, and bioinspired materials research (in process)
- Preceramic Polymers and Polymer-Derived Ceramics (in process)
- Luminescence Materials and Optical Ceramics (accepting submissions)
- Advances in Transparent Glass-Ceramics (opening soon)
- Thermodynamics for Sustainable Ceramics (opening soon)
More are in the planning stages, please check back.
Reading, Writing and Reusing
Reading journal content
- ACerS members have free access to all articles published in the ACerS journals. Go to the Member Access page or ACerS Publication Central to get started.
- Nonmembers can access journal content via a number of paid routes. Select the “Access Articles” link for more information
Writing journal articles
- The ACerS journal editors have adopted a single-document policy for initial manuscript submissions. Fully formatted files are required upon acceptance of the manuscripts. Select the “Author Instructions” link for complete instructions
- ACerS maintains the highest level of publication ethics. We accept only original work that properly attributes others’ work, be it from co-authors or prior art.
- Prior to submitting your work to JACerS, you should review the aims and scopes to make certain your work meets our high standards for acceptance and publication
Reusing content and other concerns
- Reusing content from the ACerS journals may require you to get permission to reproduce. Our publishing partner, Wiley, manages this relatively simple process and the the reuse permissions page provides instructions for requesting permissions.
- Minor concerns about article content such as requesting a correction to your own work or that of others should be addressed to the authors or the journal’s editor-in-chief. If a public comment or correction are warranted, you can submit these through the manuscript submission process.
- Major concerns/potential plagiarism. ACerS takes all questions of plagiarism very seriously and the process for addressing these is on the Publication Ethics page.
Submitting Manuscripts
or Becoming a Referee / Reviewer
Establish accounts on these services and associate your articles and reviews with them to begin your journey as a JACerS author and reviewer.
Authoring and reviewing manuscripts are important for your scholarly career. We highly recommend beginning this journey by establishing your digital publishing footprint (persistent identifiers). ACerS, Wiley, and most publishers and organizations supporting scholarly publishing use persistent identifiers to connect your work (authoring and reviewing articles) to you. This is particularly important where your name is similar (or identical) to another author.
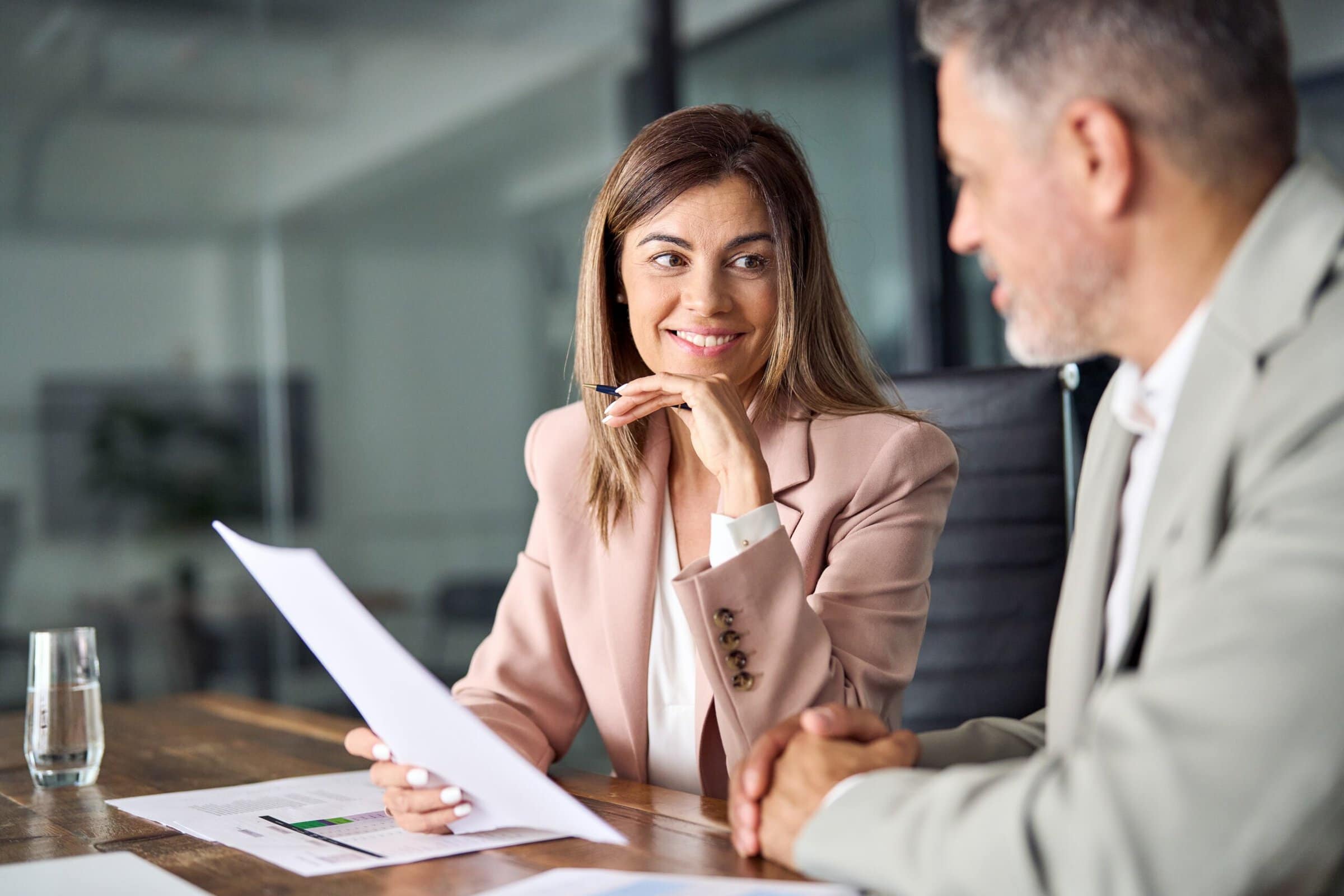
ORCID Account
The first step is having an ORCID persistent personal identifier. Click the ORCID account button to create or update your personal account. As you establish and maintain your other publishing accounts, make sure to add your ORCID to those accounts. If you have already authored or co-authored articles, you can and should add those articles to your ORCID account.
Web of Science Signup
The ACerS journals encourage you to maintain a record of your reviews on the Web of Science (WoS) Reviewer Recognition Service. Our manuscript review management software uses this service to provide a list of highly qualified referees to our editors. Click on Web of Science signup to establish or update your account with Clarivate (the owner of WoS). Associating your ORCID with this account enables WoS to include your articles in their database of your expertise. As with your ORCID, we highly recommend associating your reviews with this account. Prior reviews can be added manually and future reviews for ACerS journals can be recorded automatically during your review.
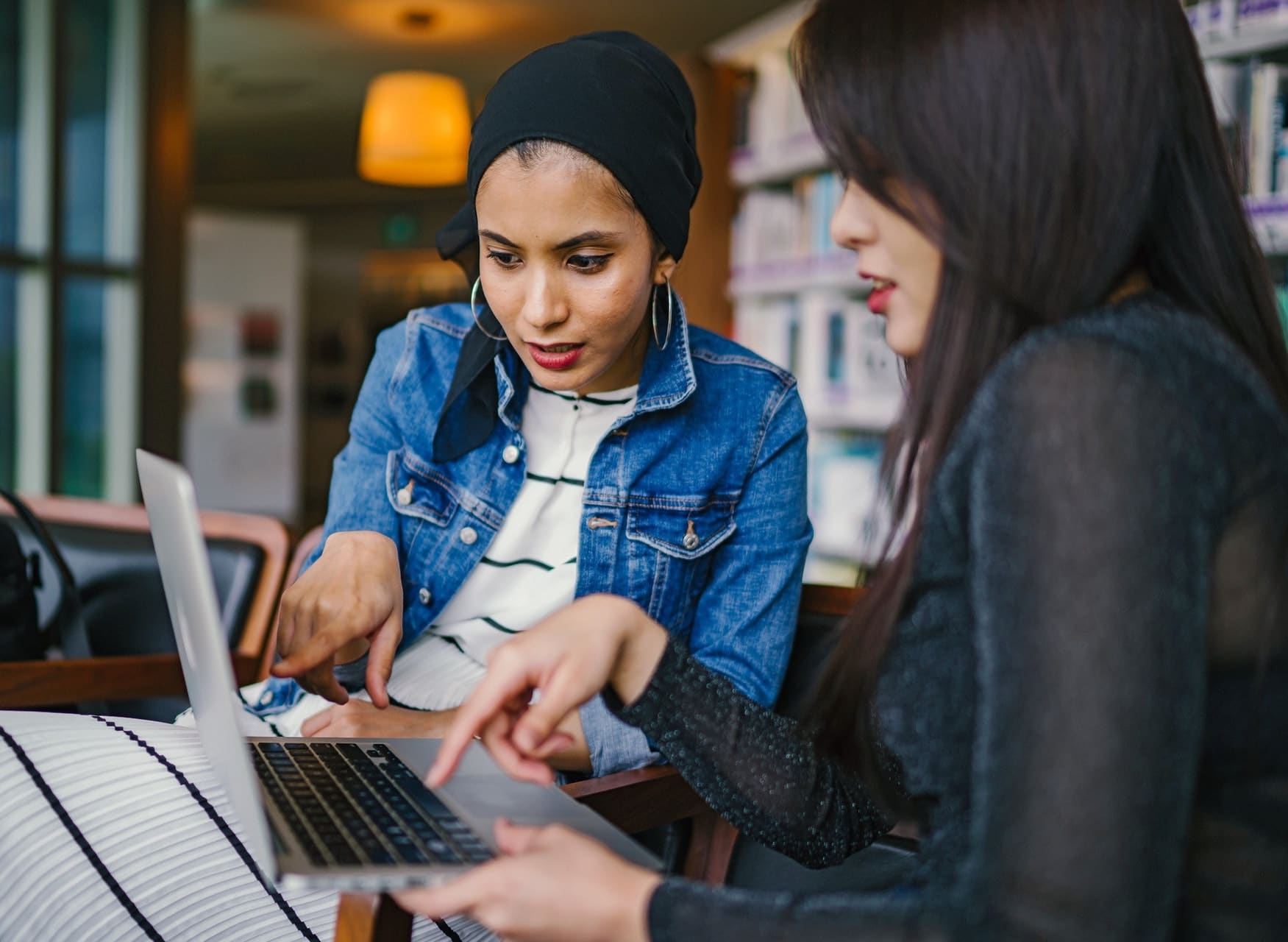
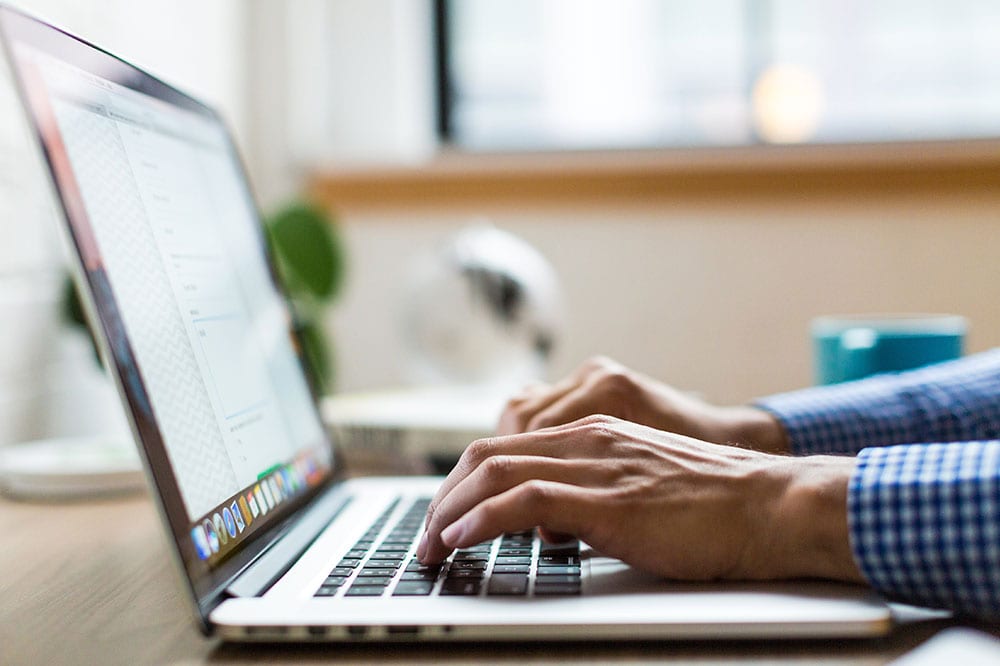
JACerS ScholarOne Account
The JACerS manuscript review process is managed through ScholarOne/Manuscript Central. Having a complete profile on the JACerS ScholarOne site helps our editors see where you have already contributed to our journals, which enhances your prospects as a reviewer. Click the "JACerS ScholarOne account" button to create or revise your JACerS ScholarOne account. Add your ORCID and use the most important keywords to describe your expertise.
REX Account
As of January 2024, JACerS authors submit manuscripts via Wiley's Research Exchange (ReX) website. ReX substantially simplifies the submission process because it uses artificial intelligence tools to extract important metadata directly from the uploaded manuscript. ReX submits the information to ScholarOne on your behalf. Click on "ReX account" button to create your Wiley Online account, submit your manuscript, or check your ReX submissions' status. Note that the email address used for Wiley Online should match the ScholarOne email for best results.
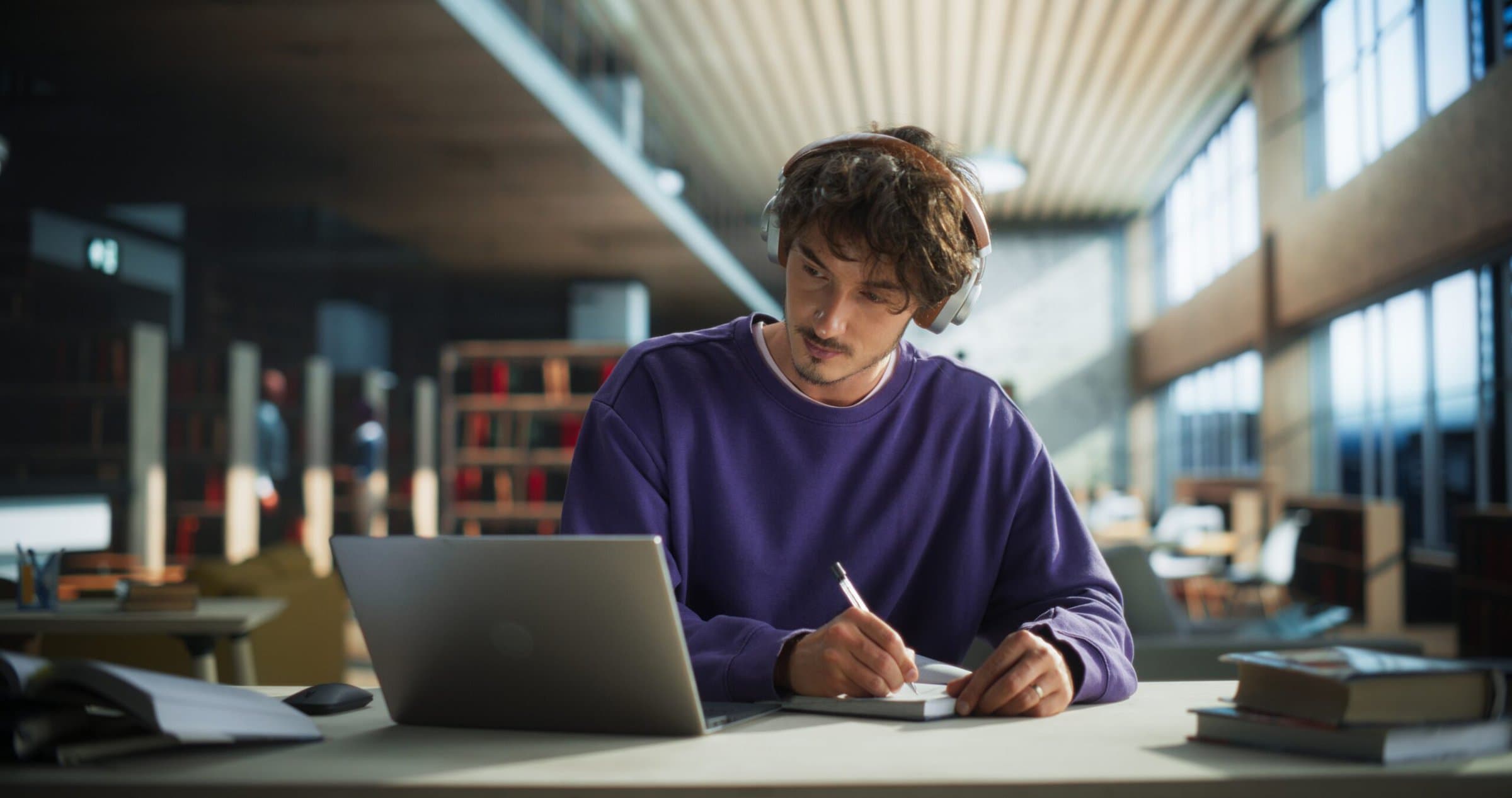