Ceramics and Glass in the Aerospace Industry
There are many properties of ceramics and glass that make these materials desirable for aerospace applications (including both commercial and defense aircraft and vehicles for space exploration). The most important are lightweight, high temperature resistance, electrical insulation, high energy of ablation, resistance to corrosion, chemical stability, wear resistance, and ability to withstand vibration.
Ceramics find use in aerospace because they are lighter than metals enabling faster speeds, reduced fuel consumption, larger payloads, and longer times in space for exploration vehicles. High temperature resistance allows commercial and military aircraft engines to run hotter, thus reducing CO2 and NOx emissions, and is critical for domes and radomes used in weapon systems that travel under the harshest conditions. Electrical insulation is necessary to avoid electromagnetic interference with the instrumentation aboard and the communication system between the pilot and ground control. High energy of ablation is critical for tiles and armor used to protect re-entry vehicles and objects flying in outer space that come in contact with fragments or particles floating in space, such as meteorites, as well as to protect military planes and helicopters during field missions. Resistance to corrosion and chemical stability are needed to protect parts of the aircraft from contact with corrosive and hazardous materials, such as jet fuel. Wear resistance is important in friction products such as brakes and bearings. In addition, vibrations and associated noise must be kept to a minimum because it creates discomfort for passengers, increases fatigue of the aircraft structural and electronic components, and, in military planes, makes them easier to be detected.
Ceramic-based materials for aerospace applications include oxides (e.g., alumina), non-oxides (e.g., carbides, borides, and nitrides), glass-ceramics, and ceramic matrix composites (e.g., silicon carbide composites). These materials are characterized by dimensional stability over a range of temperatures, and are optimized to have good mechanical strength and chemical resistance.
In aerospace applications, ceramics are primarily found in engine and exhaust systems, thermal protection shields, and structures for ultra-high-speed flying objects. Ceramics and ceramic matrix composites that can withstand temperatures as high as 1,600°C are used to manufacture lightweight turbine components that require less cooling air, such as vanes, blades, nozzles, and combustion liners, and parts for the exhaust system that enhance acoustic attenuation and have a long life thanks to their abrasion and corrosion resistance.
Thermal protection shields are critical in reusable space vehicles, similar to those adopted in the Space Shuttle program, where glazed porous ceramic tiles were employed to minimize the heat load and the chemical attack from ionized species present in the top layers of the atmosphere during reentry.
Ultra-high-speed flying objects include supersonic and hypersonic vehicles as wells as rockets and missiles. Their aerodynamic design, which involves the presence of sharp mechanical elements, entails the use of materials that are able to resists very high temperatures. Currently, these materials are being produced by adding reinforcing agents, such as particles, whiskers, and fibers, to also improve thermal shock and fracture toughness properties. Ultra-high temperature ceramics (UHTCs) that can withstand temperatures as high as 2,200°C are being developed for fabrication of hypersonic vehicles.
Other applications of ceramics in the aerospace industry include brakes, bearings, seals, and other wear resistant components; armor for helicopters; electronic thermal management structures; lightweight optical components (e.g., silicon carbide mirrors); radiators (i.e., cooling systems) for space vehicles; and windshield coatings.
Ceramic components for the aerospace industry are often characterized by very complex shapes, driving the development of new forming technologies, such as 3D printing.
Glass is used in aircraft to build windshield and window panes, canopies, panels for cabin interiors, mirrors for lavatories, interior and exterior light-emitting diode (LED) lighting solutions, protections for sensors and instrumentation, ultrasonic transducers, and colored filters for enhanced flight vision systems.
The main applications of ceramics and glass in the aerospace industry are illustrated in the table below.
Ceramics
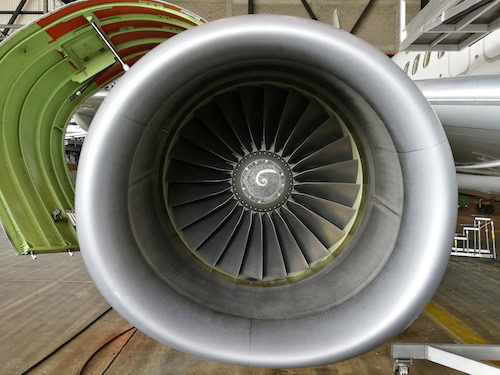
Aircraft - Engines
Components of engine and exhaust systems
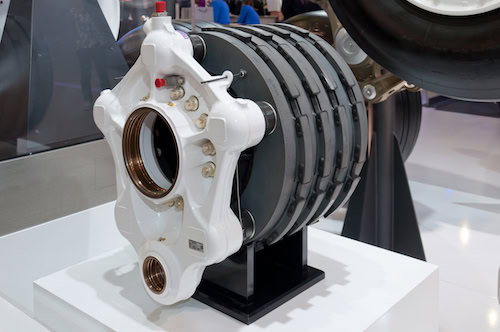
Aircraft - Brakes
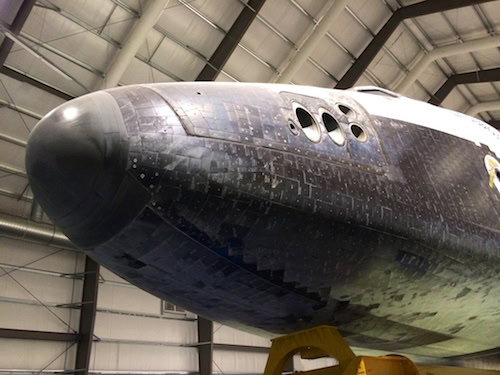
Space vehicles
Insulating tiles
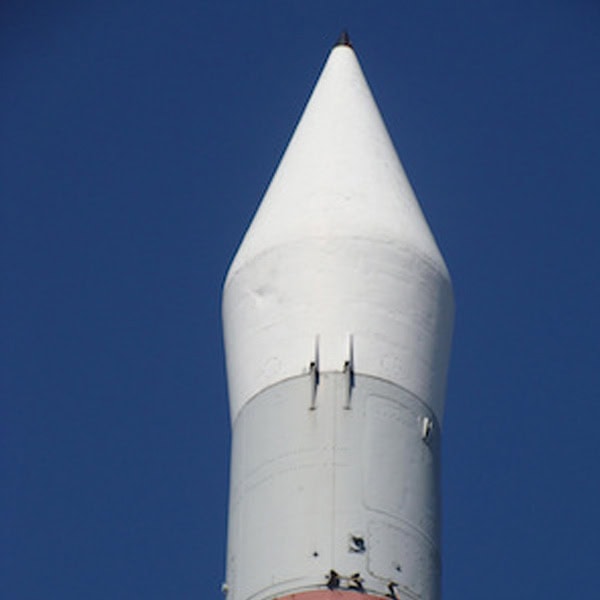
Ultra-high speed flying objects
Nose cones and high-temperature coatings
Glass
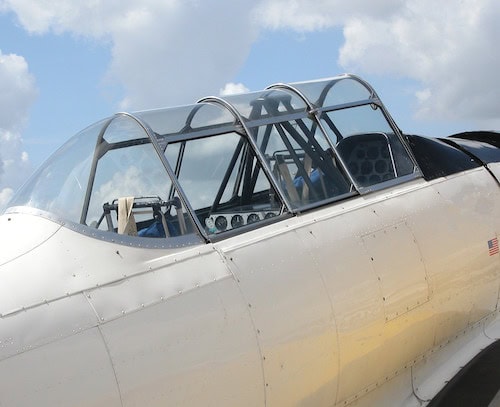
Aircraft - Windshields
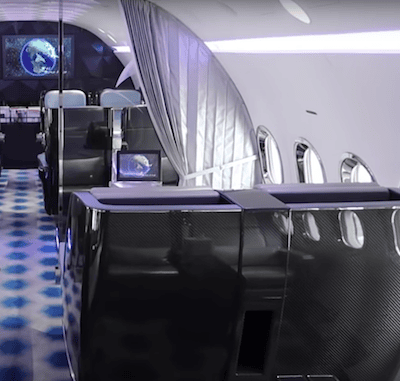
Aircraft - Panels and mirrors for cabin interiors
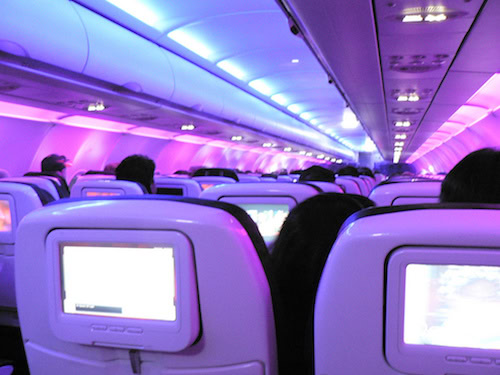