[Image above] Credit: ACerS
For the first time in its eight-year history, Ceramics Expo 2023 said farewell to its traditional home of Cleveland, Ohio, and moved to the Suburban Collection Showplace in Novi, Mich.
Ceramics Expo is the leading annual supply chain exhibition and conference for the advanced ceramic and glass industry. It took place last week from May 1–3, starting with a VIP networking event on Monday night and then two days of exhibiting and conference talks. For the second year, the co-located Thermal Management Expo ran alongside Ceramics Expo.
As you might imagine with moving the exposition to the Detroit metropolitan area, transportation and energy technologies were prevalent throughout this year’s technical forums, which also included sessions on extreme applications and traditional and advanced manufacturing methods.
Transportation: From ICE vehicles to EVs
The opening session, moderated by ACerS director of technical content and communications Eileen De Guire, focused on the role of ceramics in the automotive industry.
Keynote speaker Adam Schubring of Kyocera began the session by talking about the potential of this market to grow from $2.5 billion in 2022 to $5.1 billion by 2028. This growth is due not only to the growth of electric vehicles but also improvements to internal combustion engines (ICEs), mainly for emissions purposes.
Currently ceramics are used for parts such as cam rollers and valve disks within ICEs; in key moving parts such as clutches and brakes; and in auxiliary systems such as electronics, actuators, and exhaust components. New application areas include advanced sensing systems, such as LiDAR and compact radar for driver-assistance, along with thermoelectrics for climate control. Many of these technologies will persist with the transition to electric vehicles, along with the growth of other applications, such as inverters and LED lighting.
Understanding the timeline of the transition to electric vehicles is extremely important for the ceramics community. Most automotive manufacturers see the transition occurring in 2030–2035, with carbon emissions regulations as a strong driving force.
Complicating these predictions are the development of ICEs that run on clean fuels, which minimize carbon emissions. Germany, for example is considering how hydrogen ICEs could fulfill European Union decarbonization goals. Plus, Toyota is introducing a hydrogen ICE vehicle.
The ensuing panel discussion, with members representing both traditional and emerging ceramics production technologies, continued along this theme. De Guire began by presenting data that showed that full adoption of ICE vehicles occurred stepwise over 50 years, whereas other technologies were faster.
The panel concurred that governments are key stakeholders in clean transportation. Government roles include planning and funding for infrastructure, such as charging stations, distributed electricity generation, and clean energy generation. One study showed that a typical rest stop service station along high-capacity motorways would require electric capacity on the order of 1 gigawatt to be able to recharge the same capacity of electric vehicles as each can refill ICE vehicles today.
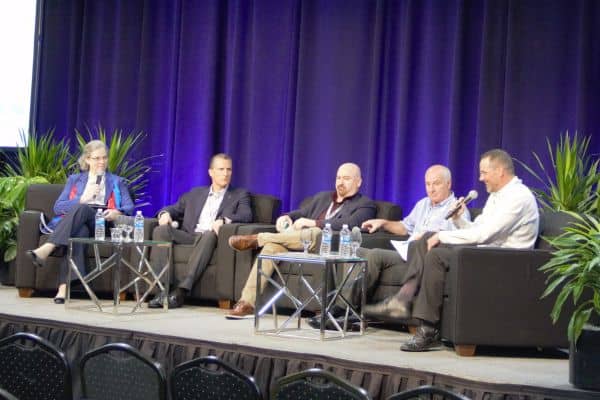
New technologies are needed to reduce adoption barriers. Examples of needed technologies include those for more efficient rapid charging and range extension. Ceramics could solve these problems with new materials for electronics, better batteries, and fuel cells. The panel mentioned that the U.S. and other governments have programs to improve manufacturing, which is available to the ceramics industry.
Several additional challenges remain, including getting more technical data on electric vehicles, such as battery lifetime (due to capacity changes), improving the environmental impacts of vehicle and electricity production, culture changes around vehicle ownership, and lack of students studying ceramic technologies. The panel suggested that these challenges also present tremendous opportunities and business potential for the ceramics community.
New applications and design paradigms
Ceramics in extreme environments (space travel, defense, and nuclear energy production) was a second application theme of the conference.
In the Day 2 keynote, Holly Shulman from Alfred University spoke of returning humans to the moon, possibly as early as 2027. Creating facilities on the moon is a critical step toward sending humans to Mars. Due to the extreme costs of moving materials from the Earth to the moon and planets, production methods that take advantage of local raw materials are critical.
Along these lines, the speaker and others are working with materials that simulate the minerology (composition, shape, and size distribution) of regolith (crushed rock) on the surfaces of the moon and Mars.
The two leading technologies for regolith utilization are microwave sintering and laser methods. Microwaves provide a rapid method for large areas and is being explored for large area “paving.” Lasers are being explored for extrusion (melting) and for additive manufacturing. Read more about these efforts here.
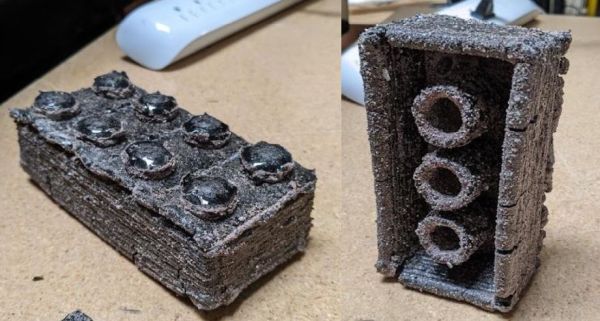
Interwoven with the applications areas were themes such as paradigm shifts in design and specification. One presenter quipped that sometimes their customers request a part fabricated from “ceramic” to replace a part traditionally made from a superalloy metal. Another worked with a customer to design and fabricate a complete ceramic assembly after the customer requested a ceramic component to replace the one metal component of the original assembly. Yet a third described how his company 3D prints ceramic molds, replacing the investment molding process of producing metal dies, wax casting, depositing powder on the wax, and sintering the ceramic to make the final mold.
Ironically, in the session titled “Replacing metals with ceramics,” few in the audience were interested in that specific topic. Rather, and perhaps a result of prior experience with ceramics, some of the audience of this session and others were keen on understanding how and where ceramics can provide new capabilities. Materials such as ceramic matrix composites and Corning’s new ultrathin continuous ceramic sheets garnered many interesting questions.
Other audience members focused on better understanding benefits, parameters, and limitations for both traditional and advanced manufacturing processes. Such discussions included adapting raw material and powder specifications and qualifying new vendors to minimize supply chain issues that arose during the COVID-19 pandemic. Exploring additive manufacturing was a recurring theme, often with questions around use in higher volume manufacturing and larger sized parts. Other themes included new techniques for nondestructive analysis and failure analysis of ceramics.
In summary, the technical sessions at this year’s Ceramics Expo provided a broad range of conversations and information addressing the breadth of the audience’s interests, backgrounds, and experience, from “how-to” questions for engineers and technicians to future technology and market insights for the managers and executives.
See more pictures from Ceramics Expo 2023 on the ACerS Flickr page. Next year, Ceramics Expo will again take place at the Suburban Collection Showplace in Novi, Mich., April 29–May 1, 2024.
Author
Jonathon Foreman
Spotlight Categories
- Division News
- Meeting Highlights
Divisions
- Manufacturing