ACerS Eastern Tennessee Section hosted the June webinar, Opportunities for additive manufacturing of ceramic composites using material extrusion in the ACerS Frontiers of Ceramics and Glass Webinar Series.
Material extrusion additive manufacturing (AM) technologies – including fused filament fabrication (FFF) and direct ink writing (DIW) – present opportunities to create polymer and ceramic composite materials and multi-material architectures that cannot be made using other AM technologies. The direct deposition nature of these processes enable the straightforward deposition of multiple materials though the use of multiple print heads, while the extrusion process preferentially aligns high aspect ratio filler materials like fibers, whiskers, and platelets. This alignment, coupled with the flexibility to choose the print path for each layer provides the ability to prescribe unique fiber arrangements within printed parts that simply does not exist with other manufacturing technologies.
The webinar began with a brief history of material extrusion AM and AM of ceramic materials, followed by a discussion of features of the process that are relevant to printing ceramics and controlling architecture and properties in printed composites. The talk proceeded with the discussion of a few examples of material extrusion AM of ceramic composites using highly-loaded silicon carbide and silicon nitride precursor polymers, including additional challenges associated with pyrolysis of the preceramic polymers. The talk concluded with a broader discussion of additional opportunities for tailored fiber orientation and multi-material architectures with material extrusion AM by drawing from recent work on printed thermoset polymer and polymer-derived ceramic composites.
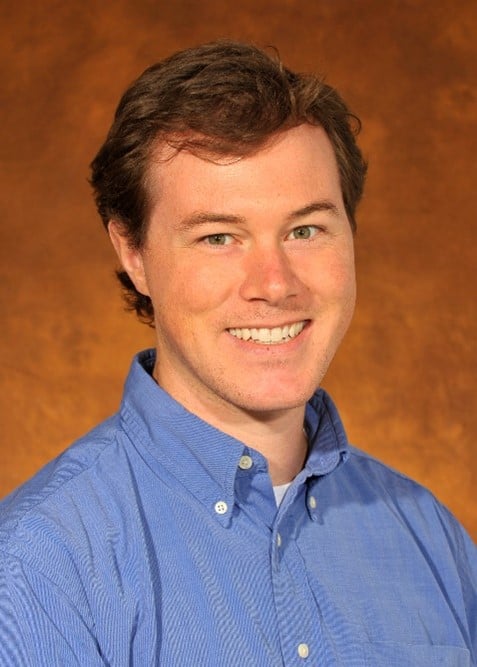
Professor Brett Compton
Prof. Brett Compton is an associate professor of mechanical engineering at the University of Tennessee, Knoxville. Brett moved to UTK from Oak Ridge National Laboratory where he was a staff scientist in additive manufacturing (AM) at the Manufacturing Demonstration Facility (MDF). The MDF is the Department of Energy’s flagship additive manufacturing center, and his research there included thermo-mechanical modeling of large-scale polymer composite AM and in situ thermal monitoring of metal powder bed systems.
Prior to moving to Tennessee, Brett was a Postdoctoral Research Fellow in the Lewis Group in the School of Engineering and Applied Sciences and the Wyss Institute for Biologically Inspired Engineering at Harvard University, where he developed materials and techniques to 3D print short fiber-reinforced epoxy resins to enable bio-inspired, lightweight polymer composites with controlled fiber orientation. Brett received his Ph.D. in Materials from the University of California, Santa Barbara studying impact damage in ceramic armor materials, and earned his B.S. in Mechanical Engineering from the University of Kentucky. Brett has been a member of the Engineering Ceramics division of ACerS since 2010.
Current research activities include the development and study of thermoset polymer and preceramic polymer feedstock materials for AM of lightweight composites, foams, and cellular structures; study of the effects the 3D printing process on properties of composites with anisotropic filler materials; and novel printing techniques to control microstructure and mesostructure in printed composites and cellular materials.
Author
Vicki Evans
Spotlight Categories
- Section News
U.S. Sections
- Eastern Tennessee