[Image above] Left, undoped spinel specimen fabricated at sintering temperature of 1,300°C, with heating rate of 2°C/min for 30 min, applied pressure of 63 MPa. and thickness of 2 mm. Right, 1.0%wt. LiF-doped spinel specimen fabricated at sintering temperature of 1,400°C, with heating rate of 15°C/min, for 120 min, and thickness of 2 mm. Credit: Rothman et al., International Journal of Applied ceramic Technology
Few ceramic processing steps are more commonly used than sintering.
Sintering is the process for consolidating powdered materials into shaped components. It usually involves heating a green body to sufficiently high temperatures for diffusion to occur in the solid state. This process is both time and energy intensive, and it often leads to substantial growth in grain size. Furthermore, large-grained ceramics tend to have reduced mechanical properties.
Ceramic researchers have pursued advanced sintering techniques to reduce sintering temperatures and times. Many methods are being explored, from use of sintering aids (additives of secondary materials) to applying nonthermal energy sources, notably electrical fields.
This month’s ACT@20 features five notable articles published in International Journal of Applied Ceramic Technology on the topic of advanced sintering techniques.
The techniques discussed include spark plasma sintering (SPS) and field-assisted sintering technique (FAST), both of which apply electrical fields across the green ceramic as it is being heated; and microwave sintering, in which electromagnetic waves are applied during heating.
The materials tested include both oxides (e.g., aluminas, silicates, titanates) and nonoxides (zirconium carbide). Some articles compare the effects of these techniques on the material structure and properties, while others use these techniques as a means for rapidly sintering samples for deeper experimentation.
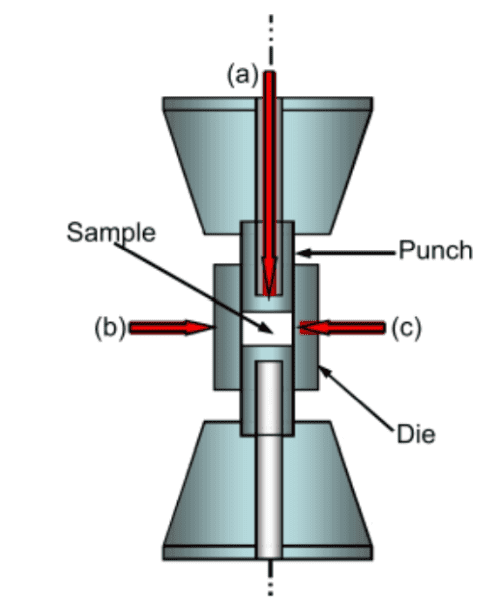
Below are some highlights from this month’s ACT@20 articles.
In “A comparison between FAST and SPS apparatuses based on the sintering of oxide ceramics,” the two techniques, which are quite similar in setup and operation, delivered rather different results. In these experiments, alumina and zinc oxide densified more quickly with SPS than with FAST under similar operating conditions. However, yttrium stabilized zirconium (YSZ) behaved similarly under both techniques.
Diving more deeply, the authors showed that the differences in temperature measurements between the two methods led to very different temperature profiles. The SPS temperature, taken at the outer wall of the sample holder, read about 100 degrees lower than the temperature at the center of the sample. FAST uses pyrometers to measure the temperature closer to the center of the sample. With its low thermal conductivity, YSZ showed a much smaller internal temperature gradient.
Along the same lines, the authors of “Microwave, spark plasma, and conventional sintering to obtain controlled thermal expansion β-eucryptite materials demonstrate that both SPS and microwave techniques provide rapid sintering with 99% dense ceramics after 2-minute and 10-minute dwell times, respectively. Conventional sintering performed with 2-hour dwell times formed about 90% dense ceramics. And for this lithium aluminosilicate material, microwave assisted sintering produced the best combination of properties. These results occur, in part, because the material is a microwave absorbing dielectric.
The combination of nonstoichiometry and fast sintering created very interesting results in “Influence of oxygen substoichiometry on the dielectric properties of BaTiO3-δ nanoceramics obtained by spark plasma sintering.” The oxygen deficiency arising from use of Ti3+ precursor for powder production combined with the rapid sintering (3-minute hold time) and reducing environment produced conductive samples. Oxidizing the samples resulted in high dielectric constants with very low tan δ values. This result occurs because of the oxygen holes being trapped in the grain boundaries.
The authors of “The effect of grain size on the mechanical and optical properties of spark plasma sintering-processed magnesium aluminate spinel MgAl2O4” explore how doping with lithium fluoride affects the structure and properties of the polycrystalline spinel.
The undoped material showed smaller grains than the doped material. As expected, the undoped material had better mechanical properties, which followed the Hall-Petch relationship. The doped material showed superior optical properties, and the authors noted that SPS can therefore be used to engineer products with desirable properties for each specific use. Also notable is that they demonstrated the negative effect of carbon impurities, which are inherent for SPS, have on the optical properties.
The article “Laser melting of spark plasma-sintered zirconium carbide: Thermophysical properties of a generation IV very high-temperature reactor material” revealed two significant achievements. First, they attained greater than 99% dense samples of zirconium carbide in under 60 minutes at temperatures between 2,000–2,100°C. Second, they demonstrated the use of a laser apparatus to explore the melting and solidification behaviors of this material, which occur at temperatures exceeding 3,000°C.
This work was followed up by further studies of zirconium carbide phase equilibria, which can be found in this article published the following year in Journal of the American Ceramic Society.
All these articles, listed below for your convenience, are free to read for the month of April.
Articles for Advanced sintering
Author
Jonathon Foreman
Spotlight Categories
- Journal and Bulletin Updates