[Image above] Credit: Kumpan Electric, Unsplash
Efficient, safe, and cost-effective energy storage technologies are required to end our dependency on fossil fuels. In many ways, it is the final piece of the puzzle.
Environmental electricity generation and its use in transportation have both reached levels of commercial viability. However, they are hindered by challenges with current storage solutions, mainly lack of capacity and cost.
At the utility level, large-scale energy storage is required to buffer between times of high energy harvesting (e.g., daylight for solar and high air flows for wind-power) and times of high energy usage (e.g., nighttime after returning home from work). For transportation and other portable applications, the current solutions carry cost, performance, life, abuse tolerance, recycling, and sustainability concerns.
The use of ceramics to develop safer and more cost-effective batteries has been explored for many decades. For example, I experimented with using ionically conductive aluminas and ferrites as electrolytes while working on my Master of Science degree in the late 1980s. The use of ceramics in batteries is the subject of this month’s ACT @ 20.
The first paper by Oshima et al. focuses on the use of sodium beta aluminas as solid-state electrolytes for sodium–sulfur batteries. The beta aluminas and analogous oxides have a layered structure consisting of dense units connected by open frameworks that allow the conduction of sodium ions.
This article discusses how morphology affects ionic conductivity and the tradeoffs required to attain the optimal material. For example, high beta” content enhances ionic conductivity but negatively affects strength. Similarly, large grains enhance conductivity but also reduce strength.
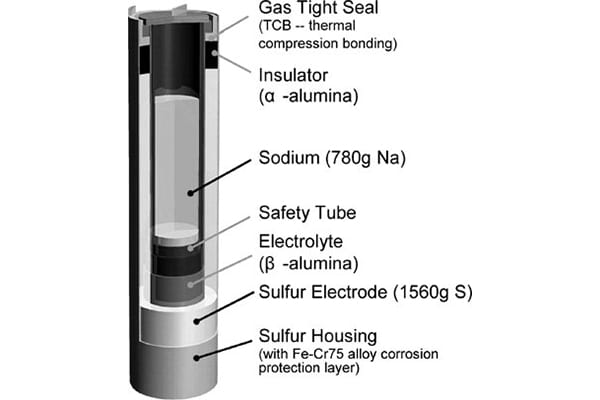
Since that article published in 2004, scientists and engineers at companies such as NGK Insulators, Ltd. have successfully commercialized and deployed utility-scale sodium–sulfide battery technologies, as described in this recent article.
For transportation and portable applications, lithium-ion batteries are clearly the technology of choice. Where sodium-ion batteries tend to require higher temperatures, lithium-ion batteries have acceptable performance levels at ambient temperatures using organic electrolytes and cobalt-based cathodes.
However, in a 2021 report, the U.S. Department of Energy says that cobalt, which comprises up to 20% of the cathode mass, is considered “the highest material supply chain risk for electric vehicles (EVs) in the short and medium term.”
Another major shortcoming of lithium-ion batteries is the formation of dendrites, where lithium metal grows in long spiky structures during the recharging process. These dendrites can penetrate the electrolyte and create short circuits when they bridge the gap between the electrodes.
The heat generated from the short circuit, and other sources, can ignite organic/polymeric electrolytes. This propensity to ignition has led to highly publicized incidences of fires in phones, laptops, personal transportation devices, automobiles, and even airplanes.
Ceramic materials have the potential to solve both these issues by reducing the amount of cobalt used in the cathodes and employing nonflammable electrolytes, which also have the potential to minimize dendrite formation. The remaining papers in this month’s ACT @ 20 highlight exemplary work toward using ceramic materials in lithium-ion batteries.
Yoshida et al. explore lithium manganese phosphate (LiMnPO4) as an alternative to cobalt- or nickel-based cathodes. Phosphate-based cathodes contain abundant, low-cost, low-toxicity materials that can also operate at high voltages, which is desirable for improving performance. Unfortunately, their work shows that the de-lithiated MnPO4 (when the battery is fully charged) can decompose at relatively low temperatures due to the instability of Mn3+ ionic state.
For the electrolyte, doped lithium lanthanum zirconium oxides (LLZO) are leading ceramic material candidates, offering acceptable performance. Processing, on the other hand, is one of the biggest challenges due to lithium volatilization at the temperatures required for sintering. The more common method for maintaining lithium content is to sinter the green electrolyte parts with excess “mother” powder of the same composition in the sintering chamber. Given the cost of the components of LLZO, this method is unfavorable for commercialization.
The papers by Huang et al. and Zhang et al. offer different approaches to solving this issue. Huang and colleagues explore using lithium carbonate as a low-cost gaseous lithium source for high-temperature sintering. They were able to retain high lithium content, phase purity, and high density in the sintered electrolyte. Furthermore, the ionic conductivity was comparable to samples they prepared using “mother” powder within the same sintering process, and electronic conductivity was negligible. They proposed using this method for other compositions.
On the other hand, Zhang and colleagues employed cold sintering methods. While exploring experimental conditions, they found that elevated temperatures, which were still much lower than for traditional sintering, and extended sintering times lead to greater proportion of the cubic LLZO morphology and higher ionic conductivity. While this study demonstrated the feasibility of cold sintering, they found the resulting ionic conductivity to be several orders of magnitude lower than for electrolytes produced by traditional sintering methods.
The main material used for the anode in commercialized lithium-ion batteries is graphite. Lithium metal is not used for the anode due to its expense, rarity, and tendency to form dendrites upon recharging. Graphite is Inexpensive and has a reasonable lithium storage capacity. Its main shortcoming is its low recharging rate, which can also lead to dendrite formation at higher charging voltages and currents.
Lithium titanium oxide (LTO) is being explored as a safer (higher voltage) anode material. Unfortunately, its storage capacity is significantly lower than for graphite. Inada et al. explored titanium niobium oxides (TNO) as alternatives to LTO. They formed TNO by solid-state reactions in air and under vacuum. They found that TNO offered higher capacity than LTO and that TNO formed under vacuum had much higher electronic conductivity (important for electrodes) than TNO fired in air.
Unfortunately, the TNO showed substantial reductions in capacity at higher charge/discharge rates, and cyclic stability was reduced compared to LTO. The authors credit the oxygen vacancies in vacuum-formed TNO for its higher performance and suggest high volume changes during insertion/removal of lithium for its reduced cyclic performance.
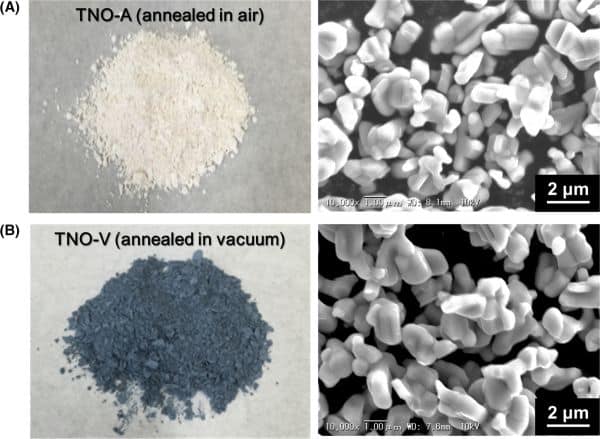
You can read these articles for free during the month of October. Visit https://ceramics.org/act-at-20 to view these articles along with a list of all the other articles in this high-value collection.
Articles for Ceramics for energy storage (batteries)
Author
Jonathon Foreman
Spotlight Categories
- Journal and Bulletin Updates