[Image above] Illustration of a reversible solid oxide cell (rSOC), which is a solid-state electrochemical device that is operated alternatively as a solid oxide fuel cell and a solid oxide electrolysis cell. Credit: Marcofici, Wikimedia (CC BY-SA 4.0)
This month’s ACT@20 collection highlights research into cells and stacks for solid oxide electrochemical cells, which are possibly the most complicated ceramic-based devices under development.
This technology requires excellent ceramic performance both functionally and structurally over wide temperature ranges, up to 1,000°C, and in both reducing and oxidizing atmospheres.
Solid oxide fuel cells (SOFCs), which generate electricity from air and fuel via high temperature electrochemical processes, have been the focus of research, development, and deployment of this technology for many years. More recently, solid oxide electrochemical cells are being explored for electrolysis (separation of water into its elements using electricity) to generate low-cost hydrogen.
The ins and outs of solid oxide electrochemical cell design
Functionally, solid oxide electrochemical cells use both electronic and ionic conducting materials, albeit in different locations. That means they have multiple layers, much like multilayer ceramic capacitors (MLCCs) but with greater functionality and operating ranges.
The electrolyte membranes are dense, pure ionic conductors. Electrode layers must be porous to conduct gases in and out of the active zone while also conducting electrons to or from the active zone.
Stacks are formed by connecting the cells in series using electronically conductive, gas tight separators. The stack must have gas manifolds to deliver fuel or water to one side of each cell (and separator) and air/oxidizer on the other side.
The cells, manifolds, and separators must all be sealed from the outside environment as well. All layers and components should have similar coefficients of thermal expansion to withstand the wide operating temperature range while also having little reactivity with each other or with the gases involved. Ideally when integrated into the final device, the stack should be easily repaired or inexpensive to replace.
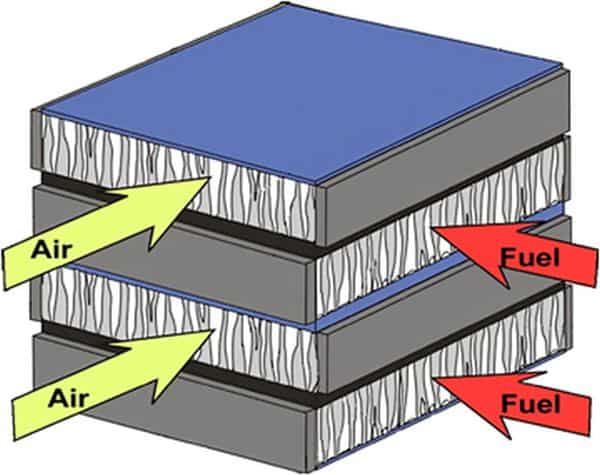
Solid oxide electrochemical cells in SOFCs: Recent studies
The article by P. Singh and Minh, which appeared in ACT Volume 1, Issue 1, provides details on the performance, structural, and manufacturing requirements for SOFCs along with the state-of-the-art technologies from 20 years ago.
Many of the companies mentioned in the article have left the field, but others have emerged. And while many of the issues raised in the article have yet to be completely resolved, a few companies are using early generation cells and stacks in pre-commercial devices to demonstrate the many benefits of the technology while researching longevity and operational parameters. These placements show that there are still many opportunities for solid oxide device research at all stages of product development.
For example, sealing is one area most in need of the right material. Seals must be able to contain gases at modest gauge pressures at stack temperatures ranging from ambient to very high operating temperatures—more than 850°C today, and possibly around 650°C in the future (to enable the use of lower cost components and systems).
Furthermore, seals must be able to withstand multiple heat-up and cool-down events. They must tolerate thermal expansion of the cells and separators, expansion and mechanical property changes induced by phase changes, while also staying nonreactive and compositionally stable.
Demonstrating the magnitude of the sealing challenge, in 2007, R. N. Singh explored four glass compositions tailored for thermal expansions close to those of YSZ electrolyte and a high-chrome ferritic steel alloy used for the separators. The parameter explored was solely self-healing capability, which is necessary to remove cracks formed in seals upon cooling. His work showed that glass crystallization was a key parameter, where highly crystallizable materials showed slower healing kinetics.
Also researching seals, Schilm et al. (2017) reported on reactivity of barium–calcium–aluminum–silicates with a high chromium ferritic steel along with thermal expansion and crystallization. Their results showed optimization of the barium content was key to prevent deleterious formation of barium chromates.
Further, barium content and barium-aluminum ratios also controlled phase formation, thermal expansion ranges, and other properties. Interestingly, some materials that had marginal performance under ambient testing regimes performed better than other materials during thermal cycling and testing under fuel-cell operating conditions.
Reducing the operating temperatures, while relieving the stresses of expansion and reactivity, results in cells with reduced conductivity. Using thinner electrolyte layers, plus substituting scandium and scandium-cerium for yttrium in zirconia, enhances ion conduction.
Unfortunately, higher conductivity cathode materials such as lanthanum–strontium–cobalt–ferrite (LSCF) materials are also needed, and LSCF reacts with zirconium to produce an insulating layer. Using a highly conducting cerium-based material between the LSCF and zirconia hampers the reactions. However, the high thermal expansion of cerium-based materials creates fabrication and operational challenges, such as spalling and delamination.
Snowden et al. address these challenges via modification of low-cost multilayer tape casting methods to fabricate anode supported cells. In their study, five layers were tape cast directly onto each other. This process is called reverse tape casting because the first layer is the ceria-based barrier layer, in contrast to most anode-supported cell fabrication, which begins with the anode support.
The five layers were 1) the ceria-based barrier, 2) the ceria-zirconia composite (for expansion coefficient transition), 3) the electrolyte, 4) the active anode layer, and, finally, 5) the anode support layer. They found approximately 7 micrometers each to be the optimal thickness for the barrier, composite, and electrolyte layers due to the trade-off between conductivity and gas-tightness.
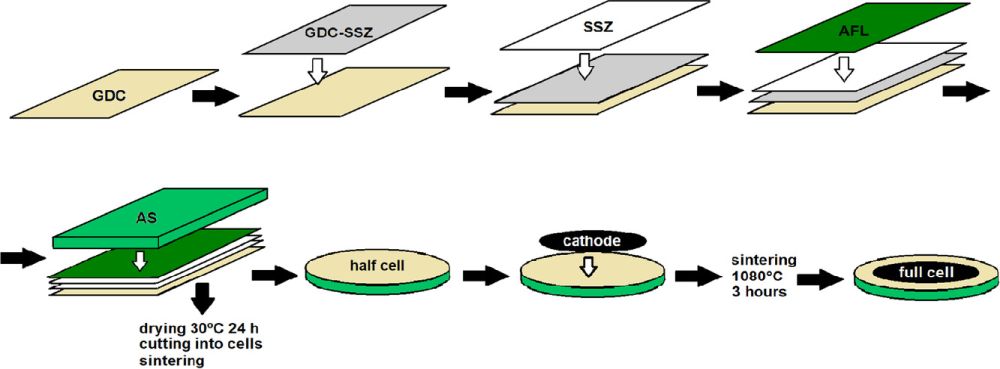
The final paper in this month’s ACT@20 compilation is by Cable et al. While the other papers in this compilation focus on making improvements to operations and fabrication of current generation SOECs, Cable et al. addresses the cell design itself and uses freeze-casting methods discussed in last month’s ACT@20 compilation.
These researchers form “electrode bilayer” cells by laminating porous, relatively thick freeze-cast zirconia tapes to thin zirconia tapes, the latter of which are designed to sinter into dense, gas-tight electrolyte layers. Active cathode and anode materials can be deposited via infiltration and other techniques.
To form stacks, dense conducting ceramic separator layers can be laminated between multiple cells, while zirconia can be used to edge-seal the electrode layers. These repeat units can be sintered as a single unit into the active stack.
The authors tested their cells under reversible SOFC/electrolysis conditions typical of unmanned aerial vehicle operational conditions, which are quite different from typical conditions used in stationary applications, for example, building combined heat and power or bulk electrolysis operations.
Under the conditions used, the cells performed well in both fuel cell and hydrogen generation modes. The authors suggest areas of study to further improve and expand operability.
Articles for Solid oxide fuel cells
Solid oxide fuel cells: Technology status | P. Singh, N. Q. Minh |
Sealing technology for solid oxide fuel cells (SOFC) | R. N. Singh |
Regenerative performance of the NASA symmetrical solid oxide fuel cell design | T. L. Cable, J. A. Setlock, S. C. Farmer, A. J. Eckel |
Glass ceramics sealants for SOFC interconnects based on a high chromium sinter alloy | J. Schilm, A. Rost, M. Kusnezoff, S. Megel, A. Michaelis |
Five-layer reverse tape casting of IT-SOFC | A. L. Snowdon, Z. Jiang, R. Steinberger-Wilckens |
Author
Jonathon Foreman
Spotlight Categories
- Journal and Bulletin Updates