[Image above] Credit: ACerS
MS&T14 started in its usual way with high energy and good spirits. The conference attracted over 3,000 attendees, including 500-700 students. (It’s Day Two as I write, so final numbers are not available yet.) There was much happy chatter at the MS&T reception Sunday evening as friends and colleagues were reunited.
The conference officially opened Monday morning with a well-attended plenary session on the theme, “Drivers for advanced manufacturing: Energy, sustainability and economics.” These phrases get tossed around often—so often, that organizers gave themselves a challenge to have something new to say. They rose to that challenge in finding this year’s three plenary speakers.
Alex King from the Critical Materials Institute in Ames, Iowa, focused on critical materials (CM), which he defines succinctly as “materials you really, really need, but have trouble getting.” A number of factors can make materials difficult to get, sociopolitical affects being most obvious (remember the rare earth spike in 2011 after a China-Japan skirmish over Senkaku Island?), but include potential bottlenecks, for example, single-sources. He gave a familiar list of examples of how critical materials shortages affect us today: rhenium for jet engine superalloys, neodymium for Nd-Fe-B permanent magnets, lithium for batteries to power our portable devices, and rare earths for phosphors in lighting.
Subtle factors affect CM supply, too. King says ore grades are declining, making extraction of the target element more difficult. A surprising number of critical elements do not exist as ores themselves, but are byproducts in other other ores. Gallium for example, is found only with aluminum ores. An unintended consequence of increased aluminum recycling is a new bottleneck for gallium. “Recycled aluminum does not produce gallium, so where, for example, will we get gallium for gallium arsenide semiconductors,” King asks?
Demand for CMs appears to be a one-way street in the direction of “more.” The first cell phone (built about 40 years ago)contained 30 elements. The just-released iPhone 6 smartphone has close to 75. King noted that the first thing consumers buy on entering the middle class is a smartphone, which in a very real way enables them to interact with affluence-management systems such as banking. Transportation—often a electric-powered bicycle—is usually the second purchase as affluence rises.
From a technical perspective, King suggests three options: diversify sources, provide alternatives to existing materials, and make better use of existing supplies. King warns, however, that these are not speedy solutions. Developing a new mine takes about 15 years and costs billions of dollars—and that does not include discovering where the minerals are. New materials take about 18 years to develop from idea to deployment. And, there are no data on how long recycling impact takes. Recycling is a tricky business, too, with unclear tradeoffs between cost, access (for example, to the magnets in hard drives), and difficulty. According to King, as smartphones become more complex, they become more difficult to recycle, too.
His bottom-line advice is to better anticipate criticality and respond faster, that is, “start sooner and work faster.”
Yves Bréchet from Grenoble–INP, France, talked about energy applications for emerging architectured materials—in other words, systems of multifunctional materials that tie microstructure to superstructure and bridge the gap between materials science and mechanical performance with systems such as graded materials and hybrid materials. He gave the example of a thermal barrier coating on a superalloy. Jet engines operate much more efficiently above the safe working temperature range of nickel-based superalloys, thanks to a complex TBC.
Focusing on energy applications, Bréchet worked through several examples of how architechtured materials help designers and engineers find materials in the “white space” where properties are desired that single materials cannot deliver. Beyond designing materials systems, he says manufacturing of new architectured materials is a wide open question. He says, “some cases additive manufacturing will be the solution, in all cases the interface will be the problem.”
Modeling is essential, he says, because materials science has evolved from accidental discoveries to materials design from first principles. “Nobody has the whole story,” he says.
Finally, Alan Taub from the University of Michigan talked about advanced lightweight materials for transportation. Taubworked for ….. prior to morphing to academia, so the context of his talk revolved around lightweighting of automobiles. But, as he noted, the same issues drive the aerospace, rail, and marine modes, too.
Taub noted that an automobile is a paradoxical consumer product. More or less, a car owner spends less than eight percent of the day driving. The car is (lovingly, sometimes luxuriously) abandoned in garages and parking lots 92% of the time. Consumers spend large amounts of money on depreciable vehicles, and focus very little on the technology advances and very much on color, finishes, stereo systems, and gadgets.
Globally, Taub says, percapita income is rising faster than the price of cars, and the global automobile “population” is approaching 1.5 billion. From an energy perspective, the efficiency of an auto is surprisingly low: only 17 of every 100 Joules of energy pumped into the tank make it to the wheels. One way to increase that ratio is to waste less energy carrying around a heavy machine—every 10% reduction in weight translates to 6% improvement in fuel economy. In the United States and at current representative fuel costs, the cost per pound saved is about equal to the cost per gallon of gas. This is important, Taub says, because consumers will tolerate a three-year payback to get back in fuel savings what they paid up front for efficiency technologies, but not longer.
Many of the solutions are metals-based: high-strength, low alloy steels, and aluminum- and magnesium-base alloys. Carbon-fiber reinforced polymers may comprise larger areas of the car body, too. According to Taub, engineers now will design cars with “the right material in the right place on the vehicle”—optimized structures with optimized materials.
Introducing new materials brings new manufacturing challenges, such as more difficult stamping, and represents a huge tooling capital investments. The American Lightweight Materials Manufacturing Innovation Institute—one of the early National Network for Manufacturing Innovation centers—is forming an industrial consortium of companies to address precompetitive technology barriers. Taub, who is also chief technology officer of the ALMMII, says it takes about 10 years to deploy a new material. However, new materials quickly reach full-saturation in the market.
Check out these other behind the scenes activities caught by April and Jessica!
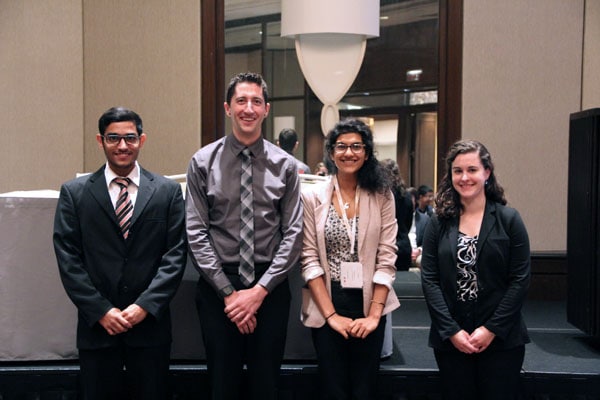
Winners of the Undergraduate Student Speaking Contest (from left): Danish Dhamani, Modeling Resistive and Capacitive Behavior of Knitted Supercapacitors, Drexel University (4th); Kevin Talley, High-throughput Techniques for Materials Discovery, Boise State University (3rd); Utthara Rameshbabu, Nano-Bio Interactions of Concave-Surfaced Gold Nanoparticles, Rensselaer Polytechnic Institute (2nd); and Jennifer DiStefano, Advancing Flexible Elecronics through Novel 2D Materials, Pennsylvania State University (1st). Credit: ACerS
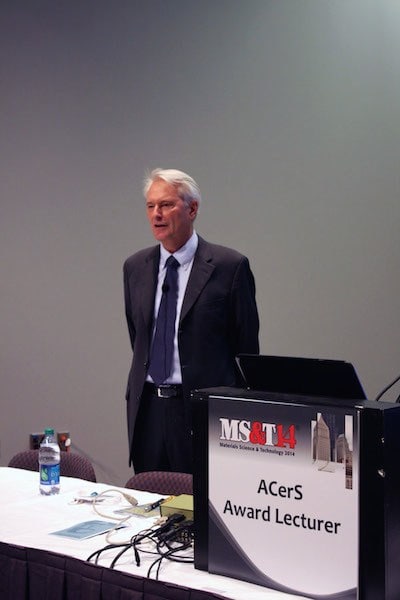
Wolfgang Rossner (Siemens AG) delivered the ACerS Frontiers of Science and Society – Rustum Roy Lecture on Sunday evening, “Ceramics for Innovation and Sustainability.” Credit: ACerS
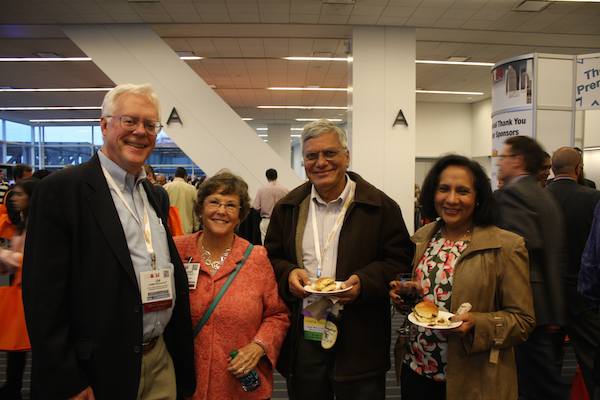
The McCauleys and Varshneyas smiled for the camera at the opening reception on Sunday evening. Credit: ACerS
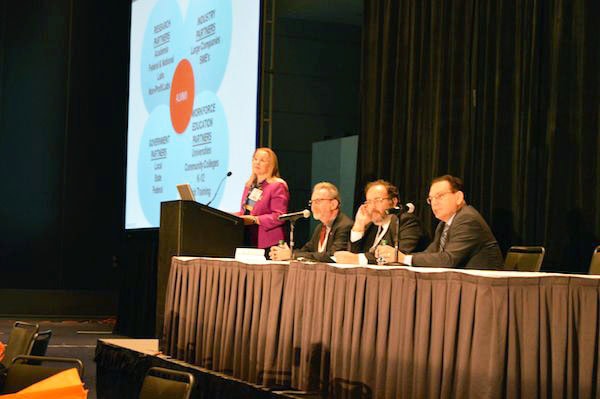
After Monday morning’s excellent plenary talks, Sunniva Collins moderated audience questions for speakers (from left) Alex King (Critical Materials Institute, Ames Lab), Yves Bréchet (Grenoble-INP), and Alan Taub (American Lightweight Materials Manufacturing Innovation Institute). Credit: ACerS
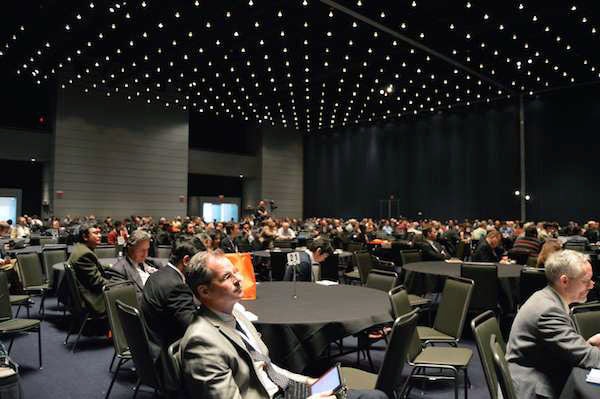
The Monday morning audience was alert, engaged, and ready for a day of serious science at MS&T14. Credit: ACerS
Author
Eileen De Guire
Spotlight Categories
- Meeting Highlights
- Society News