[Image above] Credit: Lightweight hexagonal and triangular honeycombs 3-D-printed using a ceramic foam ink. Credit: James Weaver; Wyss Institute
Researchers at Harvard University and Massachusetts Institute of Technology seem to have taken inspiration from the kitchen.
Which may not be all too surprising—there are a lot of similarities between following a protocol in the lab and a recipe in the kitchen.
So in a process that resembles whipping egg whites into a meringue, the researchers have devised a procedure for fabricating ceramic foams that can be used to 3-D print cellular materials that combine both microscale and macroscale porosity.
See for yourself.
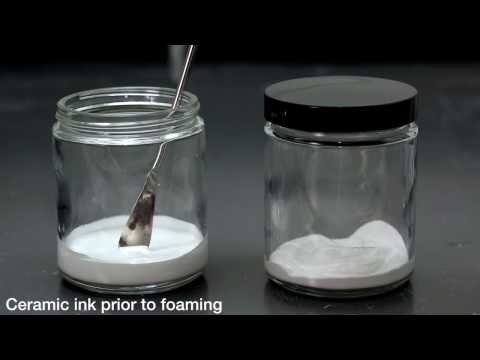
Credit: Harvard John A. Paulson School of Engineering and Applied Sciences; YouTube
Using a ceramic ink of alumina particles suspended in water, the team simply whips air bubbles into the mixture to create a fluffy ceramic slurry that can be 3-D printed—via a process called direct foam writing—into a low-density, high-strength architecture.
“By expanding the compositional space of printable materials, we can produce lightweight structures with exceptional stiffness,” Jennifer Lewis—ACerS Fellow, Hansjorg Wyss Professor of Biologically Inspired Engineering at Harvard’s School of Engineering and Applied Sciences, and senior author of a recent paper published in Proceedings of the National Academy of Sciences describing work—says in a Harvard press release.
According to the paper’s abstract, the printed and sintered alumina foam honeycomb structures have a relative density of just ~6%, making them incredibly lightweight.
But what’s really fascinating about these 3-D-printed ceramic foam structures is that their properties can be controlled on two different levels.
“Foam inks are interesting because you can digitally pattern cellular microstructures within larger cellular macrostructures,” first author and Lewis lab graduate student Joseph Muth says in the release. “After the ink solidifies, the resulting structure consists of air surrounded by ceramic material on multiple length scales. As you incorporate porosity into the structure, you impart properties that it otherwise would not have.”
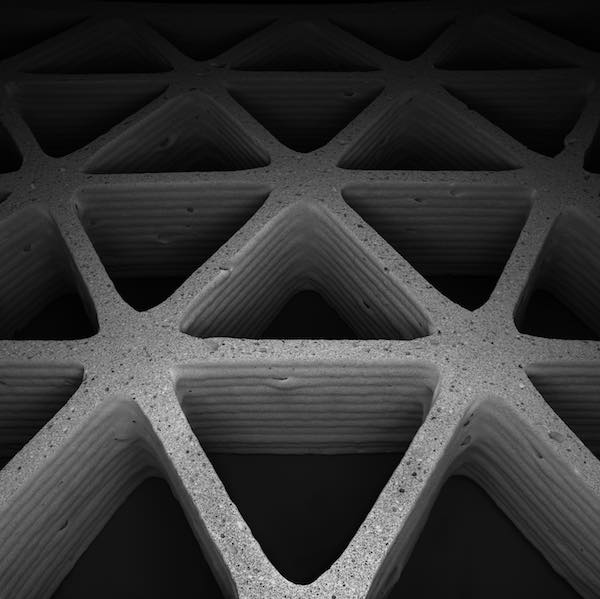
Lightweight hexagonal and triangular honeycombs 3-D-printed using a ceramic foam ink. Credit: James Weaver; Wyss Institute
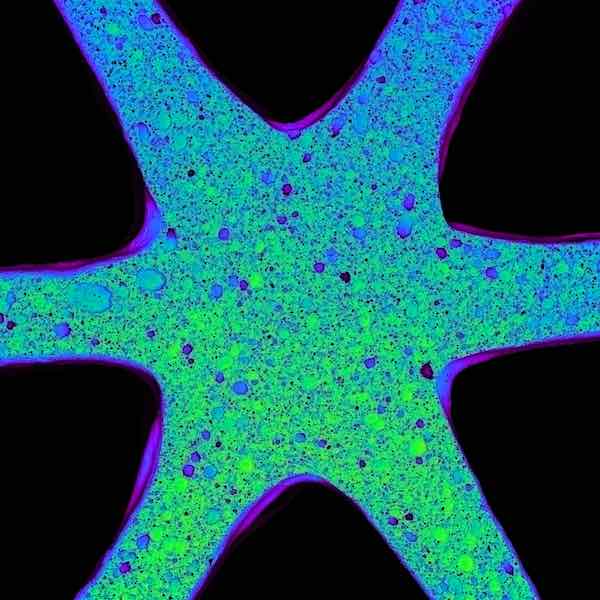
Close-up image of one node of the triangular honeycomb, consisting of air surrounded by ceramic particles. Credit: James Weaver; Wyss Institute
So while adjusting the foaming process controls the final product’s microscale porosity, its macroscale porosity can also be adjusted by simply varying the 3-D print design.
“This process combines the best of both worlds,” coauthor Lorna Gibson, the Matoula S. Salapatas Professor of Materials Science and Engineering at MIT, says in the release. “You get the microstructural control with foam processing and global architectural control with printing. Because we’re printing something that already contains a specific microstructure, we don’t have to pattern each individual piece. That allows us to make structures with specific hierarchy in a more controllable way than we could do before.”
And that means that the researchers can specifically adjust the structures’ mechanical properties, too, varying their mode of deformation and specific stiffness by varying the individual levels of porosity.
“We can now make multifunctional materials, in which many different material properties, including mechanical, thermal, and transport characteristics, can be optimized within a structure that is printed in a single step,” Muth adds in the release.
Such strong, lightweight, and tailorable materials have incredibly wide-ranging potential applications. The authors indicate that a few possibilities are thermal insulation, tissue scaffolds, catalyst supports, and electrodes.
That last potential application may be the first to see reality, because some of the technology and talent already developed in the Lewis lab have founded a company called Voxel8 that is pioneering 3-D printed electronics.
What do you think—what are some other potential applications of 3-D printed cellular ceramic foams?
The paper, published in Proceedings of the National Academy of Sciences, is “Architected cellular ceramics with tailored stiffness via direct foam writing” (DOI: 10.1073/pnas.1616769114).
Author
April Gocha
CTT Categories
- Electronics
- Material Innovations