[Image above] Credit: ESA–G. Porter, CC BY-SA 3.0 IGO
Ever since U.S. astronauts walked the moon between 1969–1972, the science community has been fascinated with returning. Earlier this year Time reported that the U.S. has a goal of establishing a mini space station that would orbit the moon, providing a base from where astronauts could venture down to the moon’s surface and back. Named the Lunar Orbital Platform-Gateway, the international collaboration will involve many countries, including Canada, Japan, Russia, and members of the European Space Agency (ESA).
But if astronauts want to build things on the moon, they will need a means to repair or replace things on the fly, as well as suitable materials from which to make the parts. And the most suitable material would be lunar regolith—the soil and dust that covers the moon’s surface.
One Austrian company is already 3-D printing ceramic nuts, bolts, screws, and other parts in preparation for supporting research activities on the moon.
Lithoz, a company specializing in additive manufacturing of high-performance ceramics, has created a collection of spare parts using a 3-D printing process with simulated lunar regolith as the “ink.” The company is working with ESA to create components and parts for a lunar base so that astronauts wouldn’t have to leave the base and return to Earth just to pick up replacement parts.
“These parts have the finest print resolution ever achieved with objects made of regolith simulant, demonstrating a high level of print precision and widening the range of uses such items could be put to,” ESA materials engineer Advenit Makaya explains in an ESA article. “If one needs to print tools or machinery parts to replace broken parts on a lunar base, precision in the dimensions and shape of the printed items will be vital.”
Simulated regolith is composed of primarily silicon oxide, but also includes other oxides such as aluminum, calcium, and iron oxide, according to Makaya. Once the parts are printed, an additional process includes grinding the regolith into small-sized particles, mixing with a binding agent, layering, and hardening. Sintering is the final step in the process.
“Thanks to our expertise in the additive manufacturing of ceramics, we were able to achieve these results very quickly,” Lithoz CEO Johannes Homa says in the article. “We believe there’s a huge potential in ceramic additive manufacturing for the Moon.”
To learn more about 3-D printing technology for lunar habitats, watch the video below.
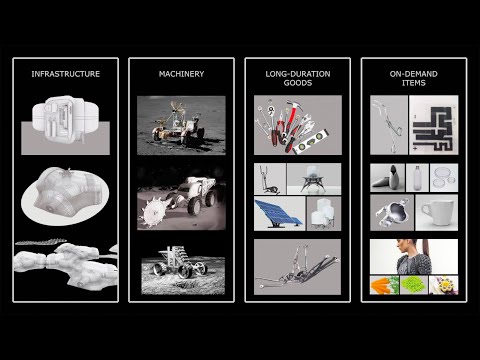
Credit: LIQUIFER Systems Group Vienna, YouTube
Author
Faye Oney
CTT Categories
- Aeronautics & Space
- Manufacturing