[Image above] The Smart Slab segments being placed piece by piece on the 12cm wide mesh mould wall. Credit: © Digital Building Technologies, ETH Zürich/Tom Mundy
Digital technologies have enabled architects and designers to build some pretty cool buildings. And concrete seems to be the latest material that designers are employing, along with additive manufacturing, to build impressive structures such as bridges, concrete houses, and even castles.
Now, led by assistant professor for digital building technologies, Benjamin Dillenburger, researchers at ETH Zurich have developed a new type of architectural construction technology that combines the “structural strength of concrete with the design freedom of 3D printing,” according to an ETH Zurich news release.
Smart Slab is comprised of a 3D sand-printed mold, or formwork, along with fiber-reinforced concrete that is sprayed over the formwork. ETH Zurich researchers created the structure using special software that designs every feature with detailed accuracy—down to the millimeter.
“It would not have been possible to coordinate all these aspects with analogue planning, particularly with such precision,” Smart Slab project lead and senior researcher in the Digital Building Technologies group Mania Aghaei Meibodi says in the release.
The Smart Slab weighs less than half of what a comparably-sized regular concrete slab would weigh. At its thinnest point, it is only 20 mm (a little over ¾”) thick, and provides the required stability with far less material, according to an ETH Zurich video.
What’s different about the creation of Smart Slab is that only the frame, or formwork was printed with a 3D sand printer. So the production method uses less concrete, and hence, generates a lower carbon footprint.
The crucial component of the technology is the software Dillenburger’s group developed that fabricates elements of the formwork and creates production parameters—including dimensions, support loads, acoustics, and a bunch of other specifications. “We didn’t draw the slab; we programmed it,” Meibodi adds.
It takes a team
After the design work is completed, industry partners contribute their role in Smart Slab’s production—from printing the sand formworks, laser cutting the timber formwork, spraying layers of fiber-reinforced concrete into the sand formwork, casting remaining concrete into the timber formwork, transporting, and installation.
A total of 11 Smart Slab segments were installed at the DFAB House, a collaborative project of the Swiss National Centre of Competence in Research at Empa’s and Eawag’s research and innovation platform NEST in Dübendorf, Switzerland.
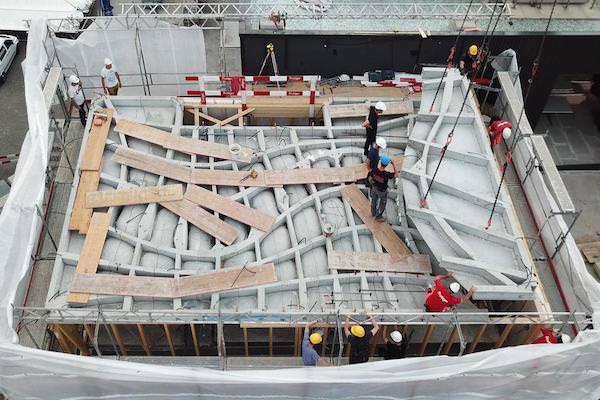
The final and largest segment of the Smart Slab—weighing almost 2.5 tonnes—being installed on site. Credit: © Digital Building Technologies, ETH Zürich / Andrei Jipa
“Smart Slab has demonstrated that a strategic use of 3D printing can increase the design space and lead to more sustainable constructions,” Dillenburger writes in an email. “Slabs will stay a focus of our research as up to 80% of the mass of the building-structure is concentrated. We are currently developing new intelligent design instruments which will help us to fully benefit from this new freedom in fabrication.”
To learn more about the Smart Slab project, visit the Digital Building Technologies page at this link.
Watch the video below to see highlights of the entire project.
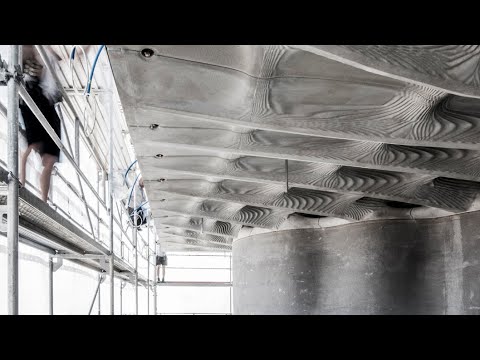
Credit: © NCCR Digital Fabrication/ETH Zürich, YouTube
Want to read more articles like this? Subscribe to the Ceramic Tech Today newsletter to continue to receive the latest news in the ceramic and glass industry right in your inbox! Visit this link to get started.
Author
Faye Oney
CTT Categories
- Cement
- Construction
- Education
- Energy
- Environment
- Manufacturing
- Material Innovations