[Image above] Examples of glass items created using a new low-temperature 3D printing process developed by researchers in the Massachusetts Institute of Technology Lincoln Laboratory’s Advanced Materials and Microsystems Group. Credit: Nicole Fandel, MIT Lincoln Laboratory
3D printing, otherwise known as additive manufacturing, has revolutionized the design and production of complex parts. Traditionally used to print metals and polymers, these techniques have made significant headway in the ceramics market as well.
The adoption of additive manufacturing in the glass community has been a slower process, however. In the 2000s, some groups, such as here, found success 3D printing glass from a powder form. Then in 2015, two groups here and here announced the successful printing of glass in a molten form.
These groups and others advanced several other glass 3D printing processes in the succeeding years, as described in a 2019 CTT. But some groups also decided to discontinue their work because they “cannot clearly pinpoint the market yet.”
Today, there are a few companies that commercially offer glass 3D-printing products and services, such as Evenline (Rochester, N.Y.) and Maple Glass Printing (Northcote, Australia). There are also academic groups that continue to research these processes, and the sections below summarize some recent work done by several groups at Massachusetts Institute of Technology (MIT).
Low-temperature glass 3D printing
Most methods for 3D printing glass rely on a high-temperature processing step, generally greater than 1,000°C, to create the final glass object. These high temperatures limit the deposition of the glass onto certain substrates that cannot take the heat, such as microelectronic components, which can be irreparably damaged above 400°C.
In September 2022, researchers in the MIT Lincoln Laboratory’s Advanced Materials and Microsystems Group announced a new 3D printing process that allows complex glass structures to be produced at temperatures of no more than 250°C.
The process is based on the direct ink writing technique, which involves extruding liquid or semisolid colloidal inks layer by layer into the desired form. In this case, the Lincoln Laboratory researchers developed a multimaterial glass ink composed of a silicate solution and nanoparticles of other inorganics.
After the ink is printed in filament form and dried, it is submerged in a mineral oil bath heated to 250°C. This process evaporates the water from the ink and causes the glass molecules and particle components to condense and harden. Rinsing in an organic solvent then removes residual mineral, leaving a fully inorganic silica item.
In an innovation highlight report, the researchers confirm that the printed glass is a self-supporting structure with a high degree of resolution and high thermal stability. It can also be printed on multiple substrates, including microelectronic components, “and its properties more closely match silicon-based microelectronics,” says Bradley Duncan, a technical staff member who lead the research, in an MIT press release.
Thus, the glass system has the potential to displace plastics widely used for 3D printing, while improving recyclability of electronic components. Achieving optical clarity, however, remains a major challenge. A patent for this process can be found here.
3D-printed glass bricks for construction
Glass has been used in architectural applications for centuries, whether as exterior windows or as internal partitions in buildings. It has also been used in brick or block form to maximize natural light while still providing privacy.
In September 2024, researchers in the MIT Mediated Matter Group announced the development of a new kind of reconfigurable masonry made from 3D-printed, recycled glass. They used cast glass masonry as the design inspiration because of its structural load-bearing properties.
The researchers used a custom 3D glass printing technology (G3DP3) provided by MIT spinoff Evenline. This latest version of the company’s glass printer can print a maximum volume of 32.5 × 32.5 × 38 cm, which is suitable for producing full-size masonry units. It pairs with a furnace to melt crushed glass bottles into a molten, printable form that the printer then deposits in layered patterns.
The multilayered glass bricks, each in the shape of a figure eight, are designed to interlock by incorporating two round pegs onto each printed brick, similar to LEGO bricks. Another material placed between the bricks prevents scratches or cracks between glass surfaces. This interlayer can be removed if a brick structure were to be dismantled and recycled, also allowing bricks to be remelted in the printer and formed into new shapes.
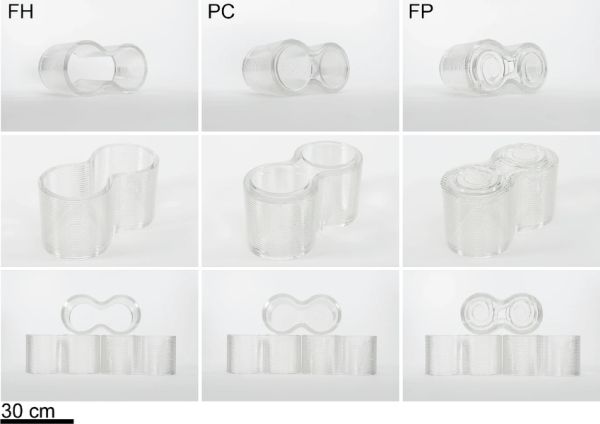
Each manufacturing method, shown from left to right: fully hollow (FH), print-cast (PC), and fully printed (FP). Credit: Ethan Townsend, Massachusetts Institute of Technology
In an open-access paper, the researchers used geometric analysis, surface roughness, and mechanical testing to compare glass bricks created using three fabrication methods: fully hollow, print-cast, and fully printed. Overall, the bricks ranged in average strength from 3.64−42.3 MPa for initial fracture and 64.0–118 MPa for ultimate strength, which is comparable to concrete blocks. More specifically,
- Fully hollow units yielded the highest load to failure, the shortest production time, and the most accurate and repeatable manufacturing process. This masonry provides a more immediate path to implementation.
- Print-cast units had moderate strength, took far longer to produce, and had less accurate and precise geometries.
- Fully printed units demonstrated favorable outcomes in terms of production time and precision, but they had a low first fracture strength, which was attributed to defects resulting from the production process. However, this type of masonry, once optimized, has potential to provide an entirely glass, transparent, and circular building component fabrication method.
In a press release, lead researcher Kaityln Becker, assistant professor of mechanical engineering at MIT, says this development “builds into our idea of a sustainable, circular building material.”
According to the researchers, they plan to develop improved tested methods, including the use of finite element analysis, and also develop reclaimable interlayers that eliminate glass-to-glass contact between masonry units. They also hope to use other types of post-consumer recycled glass for production.
The open-access paper, published in Glass Structural Engineering, is “Additive manufacturing of interlocking glass masonry units” (DOI: 10.1007/s40940-024-00279-8).
Author
Laurel Sheppard
CTT Categories
- Construction
- Glass
- Manufacturing
- Material Innovations