[Image above] Princeton University mechanical and aerospace engineering professor Michael McAlpine holds a contact lens 3D printed with LED lights. Credit: Frank Wojciechowski; Princeton
Researchers at Princeton University want to give you googley eyes.
Using additive manufacturing—a.k.a. 3D printing—they have printed LED lights directly into a hard contact lens to prove that active electronics of varied materials can be printed into complex shapes.
While you may already be dreaming of a real-life Cyclops from X-Men (it’s okay, I was, too), don’t get your hopes up—the engineers created the device soley as of a proof of principle. [But speaking of a real-life Cyclops, definitely do not try this at home.]
But, since your mind was already wandering, let’s entertain that thought for a mo. Others have previously designed prototypes for smart contact lenses that can provide infrared vision or project a virtual display. Fun for conveying superpowers to mere mortals, but even more exciting for the possibilities they suggest for people with impaired vision. I’m not really sure how LED-light emitting contact lenses might do much useful (other than lend a hand to your Terminator costume at Halloween next year), but they do inspire musings of the possibilities of printing complex materials and products.
“This shows that we can use 3D printing to create complex electronics including semiconductors,” says Michael McAlpine, mechanical and aerospace engineering professor and senior author of the new research, in a Princeton press release about the work. “We were able to 3D print an entire device, in this case an LED.”
The researchers used additive manufacturing to print cube-shaped LEDs into hard plastic contact lens, using quantum dots as the “ink.” In total, they printed together five different materials: “(1) emissive semiconducting inorganic nanoparticles, (2) an elastomeric matrix, (3) organic polymers as charge transport layers, (4) solid and liquid metal leads, and (5) a UV-adhesive transparent substrate layer,” according to the paper’s abstract, published in Nano Letters.
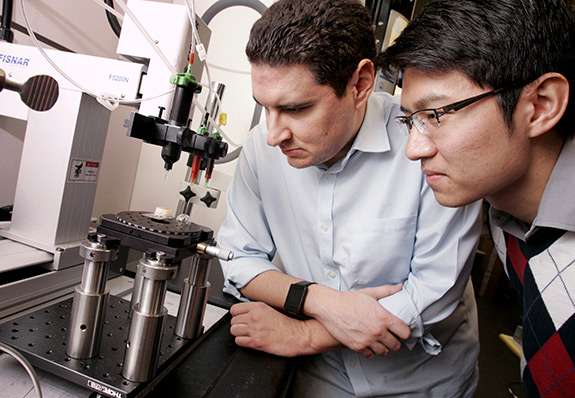
McAlpine (left) and Kong (right) keeping watch over the custom 3D printer used to build active electronics. Credit: Frank Wojciechowski; Princeton
Part of the novelty of this project and its indication for future electronics is that the team printed complex electronics from diverse materials, which can be a challenge due to varying properties of each material.
“The materials were often mechanically, chemically, or thermally incompatible—for example, using heat to shape one material could inadvertently destroy another material in close proximity,” states the press release. “The team had to find ways to handle these incompatibilities and also had to develop new methods to print electronics, rather than use the techniques commonly used in the electronics industry.”
According to Yong Lin Kong, lead author and mechanical and aerospace engineering graduate student, “For example, it is not trivial to pattern a thin and uniform coating of nanoparticles and polymers without the involvement of conventional microfabrication techniques, yet the thickness and uniformity of the printed films are two of the critical parameters that determine the performance and yield of the printed active device.”
Although the scientists don’t envision 3D-printed electronics taking the place of conventional manufacturing techniques—which primarily use lithography, a technique that is fast, efficient, and reliable—3D printing could be used in the future to create complex and customized electronics for particular applications, like custom-fitted medical devices.
“Trying to print a cellphone is probably not the way to go,” McAlpine says in the release. “It is customization that gives the power to 3D printing.”
The paper is “3D printed quantum dot light-emitting diodes” (DOI: 10.1021/nl5033292).
Author
April Gocha
CTT Categories
- Electronics
- Manufacturing
- Material Innovations
- Optics
- Weekly Column: “Other materials”