[Image above] These scanning transmission electron microscope images show how the crack in a crystal of titanium dioxide begins to “heal” with increasing electron doses. Credit: Guo et al., Nature Communications (CC BY 4.0)
I along with almost everyone have experienced the dread of watching a ceramic container falling to the ground, knowing it is too late to save the brittle object. While it may be possible to piece the object back together, such as through the beautiful Japanese art of kintsugi, it will not be exactly the same as it was before.
While this example demonstrates immediate, catastrophic failure of a ceramic, what is more concerning to manufacturers are the small, slow cracks that develop in a ceramic component as it undergoes repeated mechanical and thermal stresses. With time, the component will experience strength degradation and finally delayed failure.
Ceramic materials that can self-heal these cracks and recover initial properties may sound like a fanciful desire, but self-healing ceramics is a very real area of research.
There are several ways to encourage self-crack-healing in ceramics. Typically, though, healing is based on a chemical oxidative reaction that is triggered when the ceramic is sintered or heat-treated.
In a recent open-access study, researchers at the University of Minnesota Twin Cities made a counterintuitive discovery of a new way to self-heal cracks in ceramics—through electron beam radiolysis.
Radiolysis is the dissociation of molecules by ionizing radiation. One or several chemical bonds will be cleaved due to exposure to the high-energy flux.
Radiolytic bond breakage is well documented in many materials, including halides, silicates, and zeolites. As such, when chemical engineering and materials science Ph.D. student Silu Guo placed crystals of titanium dioxide under an electron microscope to study some naturally occurring narrow cracks, she expected that the ceramic may experience some degradation.
Instead, much to her surprise, “these cracks kept filling in,” she says in a University of Minnesota press release.
Guo immediately set to work with other University of Minnesota students and professors, including lead researcher and chemical engineering and materials science professor Andre Mkhoyan, to understand why the cracks were filling in. In the new paper, they detail the mechanism behind this unusual observation.
As expected, the electron beam irradiation caused extensive breaking of the titanium–oxygen bonds along the edge region of the crack. However, this release of the titanium and oxygen atoms enabled them to move into the crack and reform bonds. As the beam dose increased, the crack was gradually bridged via these “two-step” rolling movements (illustrated in the accompanying figure).
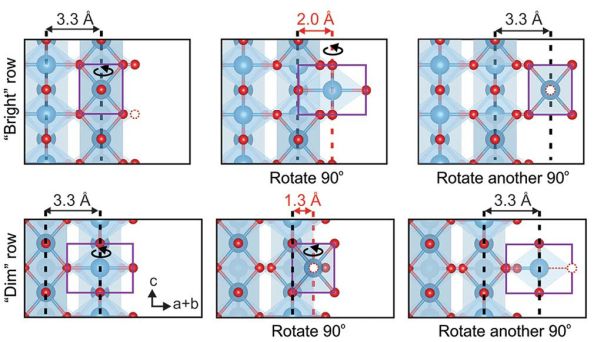
Illustrations of the “2-step rolling” model showing how an octahedral unit (highlighted in purple) at the edge of the crack from the “bright” (contains titanium and oxygen atoms) and “dim” (contains only titanium atoms) columns can rotate 90° and occupy an interstitial site in the first step and then reach its final site after another 90° rotation in the second step. Axes of rotation are indicated. Each interstitial site can be characterized by the distances from the nearest neighboring atomic column (highlighted by red dashed line). The red dashed open circles indicate oxygen vacancies. Credit: Guo et al., Nature Communications (CC BY 4.0)
Excitingly, the bridges within the crack had the same rutile structure as the bulk. In other words, the material was restored to its original structure.
Notably, the bulk region of the titanium dioxide did not appear affected by the electron beam irradiation, except at very high doses.
“In conclusion, analysis of high-resolution HAADF-STEM images [high-angle annular dark-field scanning transmission electron microscopy] combined with core-level EELS spectra [electron energy-loss spectroscopy] shows that high-energy (80–300 keV) electron beams at high doses (≥107 e/nm2) can radiolytically restructure a crystalline material instead of amorphizing it,” the researchers write.
They predict that similar radiolysis-driven restructuring would be possible in other oxides with crystal structures consisting of octahedral or tetrahedral building blocks, as long as the oxides satisfy the requirements for significant radiolysis.
The researchers are now investigating ways to improve or speed up the process, such as by changing the electron beam conditions or changing the temperature of the crystal.
The open-access paper, published in Nature Communications, is “Mending cracks atom-by-atom in rutile TiO2 with electron beam radiolysis” (DOI: 10.1038/s41467-023-41781-x).
Author
Lisa McDonald
CTT Categories
- Material Innovations