[Image above] Credit: William Cho, Flickr (CC BY-SA 2.0)
Armor for protecting warriors and their conveyances can be traced back more than 3,000 years across Europe and Asia. Though you are probably most familiar with the metal chains and plates used in medieval times, armor has been fashioned from many materials over the years, including leather and bamboo. The 20th century saw the rise of polymeric (e.g., Kevlar and other aramids) and ceramic armor in our quest to maximize stopping power while minimizing weight and volume.
Armor functions by altering the concentrated energy of a projectile or blade so that it dissipates more slowly and over wider areas than it is delivered. For example, the energy of a sword is concentrated at its sharp edge, which breaks bonds to penetrate clothing and flesh. However, when a sword contacts metal armor, its energy is spread out and results in a dent or other broad deformation.
Modern day bullet-proof vests use similar mechanisms for spreading the energy of a bullet without breaking through the layers of woven polymer. But woven polymer armor tends to fare poorly against stabbing attacks because sharp points can penetrate the fabric.
Current stab-resistant polymeric armor tends to be bulky and heavy. However, in theory, a ceramic-coated fabric can provide equivalent stopping power to an uncoated fabric while weighing about 60% less.
To test this theory, Gadow and Von Niessen used atmospheric plasma spraying to coat aramid fibers with ceramic and cermet coatings. The hardness of the coatings increased penetration resistance of the fabric five-fold while the mass gain only doubled the areal density. Plus, their process has the potential to be used in roll-to-roll manufacturing.
This paper is part of this month’s ACT@20 collection on developments in ceramic armor. The remainder of the articles chosen by the editors of International Journal of Applied Ceramic Technology focus on the development of measurements to qualify ceramic armor under ballistic conditions.
The key goals of these studies are improving energy dissipation, maintaining structural integrity, and minimizing weight and volume. For example, Shockey, Simons, and Curran mention that bulletproof windows on Humvee personnel carriers during the Gulf Wars were fabricated from 10-cm-thick soda-lime glass and weighed 40 kg each. Imagine how much better this vehicle could perform and endure with lighter weight windows!
Qualifying the ballistic performance of ceramic armor materials is not trivial. For example, standard mechanical property tests are carried out at low strain rates, which are very different from the mechanical conditions arising from stopping ballistic projectiles. Yet, the standard tests are ubiquitous, (mostly) well understood, and rather inexpensive.
The article by Swab provides key insights into qualifying mechanical test methods for armor materials, specifically hardness testing. His work establishes that Knoop hardness testing is most appropriate for armor materials. It provided consistent results across different materials, which followed theoretical aspects of hardness testing. Vickers hardness testing is less consistent and more difficult to interpret at high stress levels due to the type of cracking it induces.
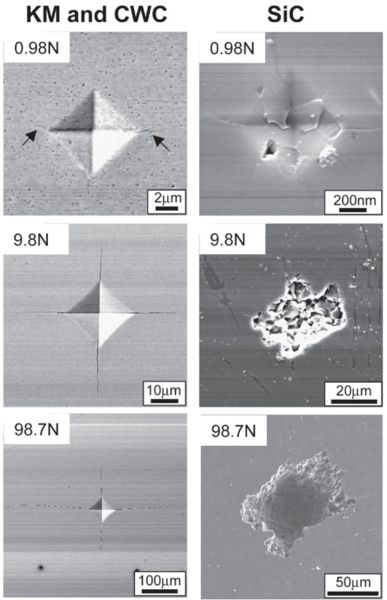
Vargas-Gonzalez, Speyer, and Campbell mention that hardness is generally (though not universally) thought to be a good indicator of a material’s ability to stop a projectile. Other mechanical factors such as toughness and strength are also important, though more for manufacturing and handling.
Their article goes on to measure a host of mechanical properties for commercial silicon and boron carbide materials and compare them to the microstructures of the as-produced samples. It is good to note that the authors measured the properties according to the pertinent ASTM procedures.
Where hardness testing and ballistics testing measure the penetration of a pointed object into materials, the penetration rates differ by many orders of magnitude. Lankford noted that ceramic armor’s compressive strengths are relatively constant up to strain rates of approximately 200 s–1. Above this range, strengths increase exponentially with increasing strain rates.
Lankford explains that at the high stresses arising from strain rates and confinement, ceramics experience plastic deformation. This deformation is due to a combination of cracking and intragranular motion along slip planes. It is noted that the particle size of the damaged ceramic decreases as strain rate increases.
Shockey et al. continue down this path. They describe and use the cracking patterns to infer mechanisms of ballistic penetration, including the zones of deformation and the resulting damage, specifically the formation of cone and lateral cracks. These cracks consolidate and lead to comminution or pulverization. The last step of the penetration is by extrusion, which is the movement of the particles both sideways into the cracked ceramic and upwards.
Shockey et al. model these failures and suggest better armor materials can be designed to resist the above processes. They focus on materials that are more difficult to comminute or result in fragments that flow less readily.
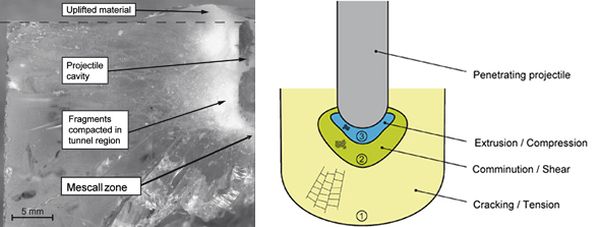
Read more about these advances in this month’s ACT @ 20 articles.
Articles for Ceramic armor
The role of dynamic material properties in the performance of ceramic armor | J. Lankford Jr |
Recommendations for determining the hardness of armor ceramics | J. J. Swab |
Lightweight ballistic with additional stab protection made of thermally sprayed ceramic and cermet coatings on aramide fabrics | R. Gadow, K. Von Niessen |
Flexural strength, fracture toughness, and hardness of silicon carbide and boron carbide armor ceramics | L. Vargas‐Gonzalez, R. F. Speyer, J. Campbell |
The damage mechanism route to better armor materials | D. A. Shockey, J. W. Simons, D. R. Curran |
Author
Jonathon Foreman
Spotlight Categories
- Journal and Bulletin Updates