[Image above] Airman at MacDill Air Force Base working on a solar-powered microwave antenna system. Credit: U.S. National Archives
The final topic for this month’s ACT @ 20 collection is piezoelectric and dielectric ceramics. Interestingly, ceramics for these applications are both mature and the subject of large amounts of research. Commercial piezoelectric and dielectric materials are found in resonant devices (buzzers) and actuators to communications electronics and energy storage devices, among many other applications.
However, lead is commonly used to create high-performance ceramics with reliable performance. The negative environmental and health impacts of lead provide the impetus for research into reduced-lead or lead-free materials and fabrication techniques.
The article by Chen et al., for example, explored the effects of doping and processing methods on the structure and performance of calcium–bismuth–niobate for high-temperature piezoelectric applications. They found a strong correlation among composition (dopant amount), crystallographic lattice parameters, and properties, such as Curie temperature, resistivity, and dielectric and piezoelectric performance.
Furthermore, the authors showed that fabrication methods affect structure and performance. They used texturing, a method that employs seed crystals, to encourage in-plane crystal growth. The highly oriented doped material exhibited superior performance, making it a promising candidate.
As the complexity of applications has grown, so have methods for fabricating 3D structures. In low-temperature co-fired ceramic (LTCC) techniques, tapes of different materials with different functionalities, such as substrates, electrodes, and active elements, are cut and stacked and then fired as a unit. The key to LTCC processing is deriving a singular sintering schedule for materials with different sintering behaviors and mechanisms. Unmatched sintering, with differential shrinkage rates, leads to devices warping, delamination, and cracking, among other undesirable effects.
Zhang and Eitel discussed the use of master sintering curves to find the sweet spot where a reduced-lead piezoelectric material will co-fire with commercial LTCC systems. Master sintering curves are derived from densification data (as a proxy for the work of sintering) for each measured over a range of heating rates. This kinetics model assumes a singular sintering mechanism for each material.
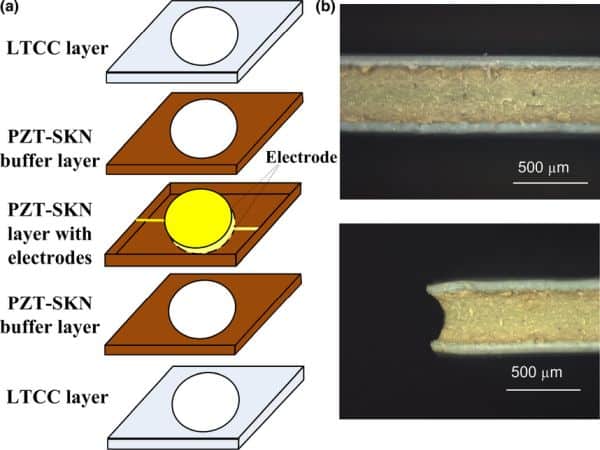
Using this model, the authors found the sintering behavior of the materials to be sufficiently similar in the temperature range of 870–900°C. From there, they refined the sintering program via experimentation. They successfully employed these processes to fabricate a resonant-frequency microbalance.
Baker et al. demonstrated fabrication of a band-pass filter, a miniaturized antenna, and a microfluidic device using LTCC techniques. Shown below is a demonstration of the microfluidics device.
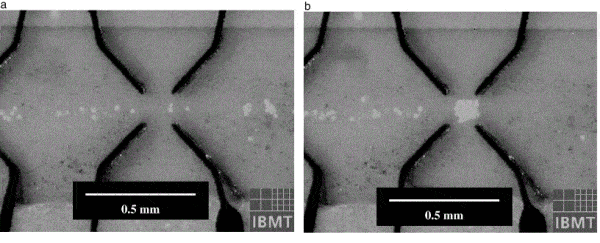
Actuators rely on stresses and strains that develop when voltage is applied across a piezoelectric device. High-strain, low-stress applications include camera autofocus mechanisms, while fuel injection systems rely on high forces that can be developed. Reichmann et al. measured the properties of neodymium-doped bismuth/mixed alkali titanates to determine its potential as an actuator. The material developed strains in the range of 0.1–0.2% with stresses up to 80 MPa.
Electronics packaging for microwave substrates requires robust materials with low permittivity and low dielectric loss. Many ceramic materials meet the dielectric property requirements, but their brittle nature limits their robustness. Polytetrafluoroethylene (PTFE), often called by the trade name Teflon, meets the dielectric and mechanical requirements. But it has low surface energy (which leads to its nonstick quality) and high thermal expansion, which limits its compatibility with the devices.
Anjana et al. fabricated ceria-PTFE composites with varying compositions and measured the density and dielectric properties. They then compared the experimental results to different mixing models.
Key to their work was the surface treatment of the ceria to enhance compatibility between these very different materials. Even so, they found substantial porosity formed when ceria content was at or more than 30%. Nonetheless, their results indicate that PTFE/Ceria 40/60 exhibited dielectric properties at room and elevated temperatures that make this composite attractive as a microwave substrate.
You can read these articles for free during the month of December. Visit https://ceramics.org/act-at-20 to view these articles along with a list of all the other articles in the ACT @ 20 collection.
Articles for Piezoelectric and dielectric ceramics
Author
Jonathon Foreman
Spotlight Categories
- Journal and Bulletin Updates