[Image above] Credit: PxHere
When we think of key applications of ultrahigh-temperature ceramics, one need look no further than the General Electric blog post from 2019 entitled “Ceramic matrix composite technology is GE’s centerpiece jet propulsion strategy for the 21st century.”
CMCs offer lower mass and higher operating temperatures than metal alloys, which enables the engine to run more efficiently at higher thrust. So, “In total, CMCs bring better fuel efficiency, lower emissions, and greater durability,” the GE blog post states.
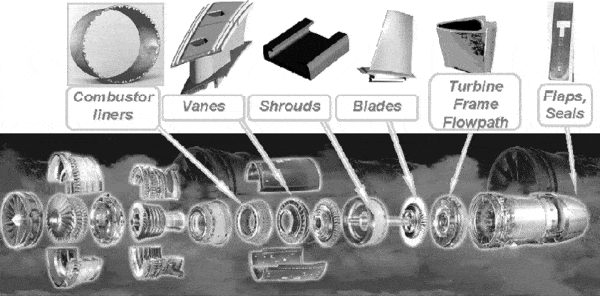
But the environment in turbine engines is challenging, to say the least. In addition to high temperatures, the components are exposed to oxygen and water vapor along with external contaminants, such as sand and silicate-rich dusts. Furthermore, engine manufacturers are seeking to raise the operating temperatures. The current limitation is 1,414°C, the melting point of silicon.
With these challenges in mind, we are excited to present you with a collection of articles on thermal and environmental barrier coatings (T/EBC) for this month’s ACT @ 20.
As the name suggests, T/EBC materials provide protection of underlying materials from heat and chemical attack. Though T/EBCs are also developed for metals, the chosen articles focus on protecting ceramic matrix composite substrates, formed mainly from carbon/carbon, carbon/silicon carbide, and other similar materials.
The requirements for these barrier coatings are straightforward in concept though difficult in practice. Among the most important criteria are high phase stability and melting points, high mechanical strength and fracture toughness, low reactivity and permeability with oxygen and contaminants, and thermal expansion compatible with the substrates. These design criteria and some solutions are detailed in “Thermal and environmental barrier coatings for SiC/SiC CMCs in aircraft engine applications.” The authors from GE Aircraft Engines further demonstrated in their lab test rigs the feasibility of using T/EBCs at temperatures around 1,700°C.
Currently no materials are known to fulfill all the design requirements. Researchers have resolved this conundrum using multiple materials applied in layers. At a minimum, there are bond coats and protective layers. The bond coats provide transitional thermal expansion behavior since many protective materials have higher expansion coefficients than the substrate materials. They also provide a modicum of thermal and chemical protection, though they are generally not sufficient on their own. Zhang et al. authored a detailed review of current state-of-the-art materials and deposition methods for bond coats.
Choi et al. provided a database of mechanical properties for free-standing pieces of yttria-stabilized zirconia (YSZ) films. YSZ and other zirconates are widely tested for environmental coatings. Because the materials are generally coated onto substrates, discerning each material’s properties is difficult. The Choi article is unique in that the authors plasma-sprayed the material onto graphite and removed the graphite through low-temperature oxidation. The resulting pieces had about 10% porosity, and their mechanical properties were quite different from fully densified YSZ. Interestingly, even though the materials were deposited on a substrate, their properties exhibited minimal directionality. The researchers further tested some properties as a function of annealing and densification to simulate in-use property changes.
In addition to densifying, YSZ changes crystal structure as it is heated and cooled. This change creates extra stress in the material, causing the coatings to spall. Vaßen et al. fabricated lanthanum and gadolinium zirconates along with YSZ in single layers and in double layers of zirconate over YSZ. Their thermal cycling/spallation testing showed that lanthanum zirconate/YSZ samples outperformed YSZ and other combinations, particularly at temperatures above about 1,300°C. The authors suggested that these materials could raise operating temperatures by 100°C.
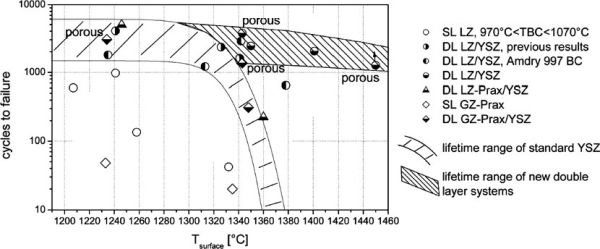
Zhu et al. explored a different route toward increasing temperatures. In their article, the authors use defect engineering to develop coating materials with low thermal conductivities. They fabricated coatings from mixtures of lanthanide and actinide ion dopants, using multiple deformation methods. Thermal conductivity was tested using laser measurements, which better approximate in-use conditions than other methods, and thermal cycling longevity was assessed. While the materials showed admirably low thermal conductivity, they were not as robust as typical YSZ materials. The authors suggested further optimization of composition and deposition methods.
As you can see, thermal and environmental barrier coatings provide substantial challenges for ceramic scientists and engineers. The payoff, however, has the potential to dramatically improve efficiencies in transportation, energy generation, and defense.
Read more about barrier coatings in this month’s articles.
Articles for Thermal and environmental barrier coatings
Author
Jonathon Foreman
Spotlight Categories
- Journal and Bulletin Updates