[Image above] Mars Science Laboratory, aka the rover Curiosity, is powered by the Multi-Mission Radioisotope Thermoelectric Generator. Credit: NASA/JPL-Caltech
Not long ago, small electric thermal containers were introduced to consumers. These devices, typically having four-liter storage capacity with a small footprint, are sold as convenient active coolers or warmers for offices, vehicles, and other uses.
Because these devices are too small for conventional compressed gas operations, the Peltier element is the key technology at the heart of these devices. Peltier elements take advantage of the thermoelectric effect, which is the direct conversion of thermal energy to electricity and vice versa.
The generation of a voltage across dissimilar materials subjected to a temperature gradient was first noticed by Alessandro Volta and rediscovered by Thomas Seebeck. It is the operating principle of thermocouples and thermoelectric generators.
Jean Peltier discovered the reversibility of the thermoelectric effect, where applying currents across these junctions can cause them to increase or decrease temperature, making this effect quite different from resistive heating.
While thermoelectric containers provide a degree of convenience, thermoelectric generators use the same principles, though in reverse, to harvest electrical energy directly from thermal energy. For example, NASA and the U.S. Navy have employed radioisotope thermoelectric generators since the 1960s for long-duration, remote power generation, such as the Mars Rover pictured at top.
Beyond these mission critical applications, transportation and industrial operations generate substantial amounts of waste heat that can readily be used as free energy sources for thermoelectric generation.
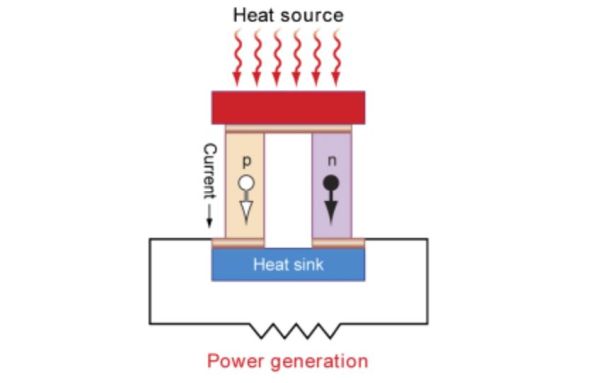
Thermoelectric generation is challenged by relatively low efficiencies. Furthermore, the materials used in these devices must be abundant, nontoxic, and chemically stable in air up to high temperatures.
As reported in this month’s ACT @ 20 collection, much work has been done not only on the development and characterization of the thermoelectric materials but also in fabrication of practical thermoelectric devices.
In the paper “Critical overview of recent approaches to improved thermoelectric materials,” Sales discusses which material properties affect the efficiency of thermoelectrics and which can be effectively adjusted.
The three major properties of thermoelectric materials are the Seebeck coefficient (also called thermopower), electronic conductivity, and thermal conductivity. The first two should be maximized while thermal conductivity should be minimized.
Unfortunately, these three properties are not independent; adjusting one affects the others. For example, materials with electronic structure designed to enhance electronic conductivity showed reductions in thermopower.
In his paper, Sales discussed materials designed to minimize lattice thermal conductivity, such as nanoscale phonon disrupters, and showed how they enhanced thermoelectric efficiency as a result.
In the paper “Effect of excess Ge and Te on Thermoelectric performance of GeTe,” Dong et al. explored how altering the relative amounts of germanium and tellurium affects the Seebeck coefficient and the two conductivities.
Because germanium vacancies lead to electronic conductivity increases and thermal conductivity decreases, one would expect increasing thermoelectric efficiency with increasing amounts of tellurium.
However, the benefits from the conductivity trends are offset by the decrease in Seebeck coefficient with increasing tellurium content. Similarly, the benefit of higher Seebeck coefficient with excess germanium is offset by lower electronic and higher thermal conductivity.
The best performance appeared at the 1:1 ratio of germanium to tellurium in GeTe. Dong et al. mentioned that they had a slight improvement with high pressure sintering compared to spark plasma sintering.
As is implied in Sales, microstructure has a significant effect on thermoelectric properties. So, Kenfaui et al. explore the effects of uniaxial pressure on the sintering of a typical oxide thermoelectric material in their paper “Anisotropy of the mechanical and thermoelectric properties of hot‐pressed single‐layer and multilayer thick Ca3Co4O9 ceramics.”
Notably, under pressure, the grains grew larger in the a-b plane (normal to the pressing direction), leading to a greatly reduced density of grain boundaries. In the c (pressing) direction, thickness decreased substantially as pressure increased. As a result, electronic resistivity decreased in the a-b plane and increased in the c-direction. The Seebeck constant was relatively unchanged.
All mechanical properties increased with sintering pressure, though the increases were greater in the c direction. Due to the thinness of the highest-pressure sintering, the authors stacked several layers and sintered a second time to achieve mechanical stability. In-plane (a-b) resistivity of the multilayer sample was similar to that of a single sheet of the material sintered into the multilayer sample. Interestingly, resistivity in the c direction was less than that for the single sheet.
As with solid oxide fuel cells, the process for mating the active high-temperature ceramics to electrical connections requires specialized electrode materials and fabrication techniques. In the paper “Microstructure contact studies for skutterudite thermoelectric devices,” Zhao et al. used spark plasma sintering to mate a copper–molybdenum electrode to a cobalt–antimony thermoelectric material with titanium foil in between.
They found that interdiffusion of antimony and titanium during subsequent aging tended to increase electrical resistance and decrease thermal conductivity. Due to the respective effects of these changes, the overall thermoelectric efficiency was minimally affected.
Wrapping up this collection, Funahashi and Urata discuss factors to be considered when creating practical thermoelectric energy harvesting devices in the paper “Fabrication and application of an oxide thermoelectric system.”
Oxides have the benefit of good chemical resistance to hot air and steam and are used as coatings for steel heat exchangers in steam generators. While oxide thermoelectric materials share these benefits, they also share potential pitfalls from thermal expansion mismatches. Additional considerations include high electrode contact resistance.
The authors overcame these challenges and fabricated proof-of-concept practical planar and tubular devices that survived multiple cycles with low degradation.
You can read these articles for free during the month of November. Visit https://ceramics.org/act-at-20 to view these articles along with a list of all the other articles in the ACT @ 20 collection.
Articles for Thermoelectrics
Author
Jonathon Foreman
Spotlight Categories
- Journal and Bulletin Updates