[Image above] Credit: Adam Greig; Flickr CC BY-SA 2.0
Editor’s note: This story originally appeared in print in the April 2016 ACerS Bulletin.
Smartphones can do practically everything—but they wouldn’t be able to do anything without capacitors.
Simply, capacitors are energy storage devices. Capacitors store energy in electronic circuits, somewhat akin to batteries, although with some important distinctions. Capacitors store much less energy than batteries, but they can discharge that energy much quicker than batteries.
Capacitors come in a wide range of sizes, shapes, and materials, but all consist of two layers of conductive materials separated by a nonconductive dielectric. Multilayer ceramic capacitors in particular can store a significant amount of energy for their compact size, making them useful in a dizzying array of electronic applications—even the touchscreen of your iPhone.
So, in addition to smartphones, most electronic devices in your life wouldn’t be able to do anything without capacitors.
Which is why capacitor failure can be a big problem. They don’t fail often, but when part of a critical device, failure is a significant concern. That concern is especially great if the capacitor is located on a critical device in a hard-to-replace location, such as on an aircraft floating in space or a biomedical device implanted within the body.
Capacitor failure often arises from cracks in the ceramic materials. While cracks are bad enough, the problem is that they can actually begin conducting electricity, completely wrecking the whole electronic device.
Screening techniques such as X-rays, acoustic microscopy, and visual inspection can detect surface cracks in capacitors, but finding smaller defects like subsurface cracks isn’t so easy. And these cracks, over time, can just as readily destroy the entire electronic device.
That’s a bad day if said device is your iPhone, but it can be fatal if the capacitor is in a biomedical device like a pacemaker. It’s usually a matter of life or death that biomedical devices function without fail, or at least with warning of imminent failure.
A Food and Drug Administration report from 2006 found that battery or capacitor abnormalities accounted for 23.6% of failed pacemakers and implanted defibrillators. While only 0.65% of the almost 3 million such devices examined in the study failed, 61 patients died due to device failures. While that’s a small percentage of the overall study population, that’s 61 lives that could potentially have been saved by better materials or better ways to monitor those materials.
Researchers at the National Institute of Standards and Technology may be on to something that can help with better materials monitoring—they have devised a new nondestructive method that may be able to detect cracks in materials before they lead to device failure.
The NIST scientists, in collaboration with scientists at the University of Maryland, NASA Goddard Space Flight Center, and Colorado State University, have developed a testing prototype that they show can detect cracks in barium-titanate-based multilayer ceramic capacitors.
The method uses a brief electric field to make the capacitor vibrate at a particular frequency and then measures how the signal decays over time. Measuring how the frequency shifts in relation to the vibration can provide important clues into the integrity of the capacitor, because cracks in the material create greater frequency shifts.
It’s not just the absolute shifts in frequency that are important—this approach has a significant and integral advantage in that it can assess various capacitors, according to a NIST press release about the work. “This nonlinear approach—focusing on frequency shifts relative to signal strength rather than the frequency shifts alone—is especially useful because it is not affected by slight variations in size of the capacitors.” Read: wider applicability.
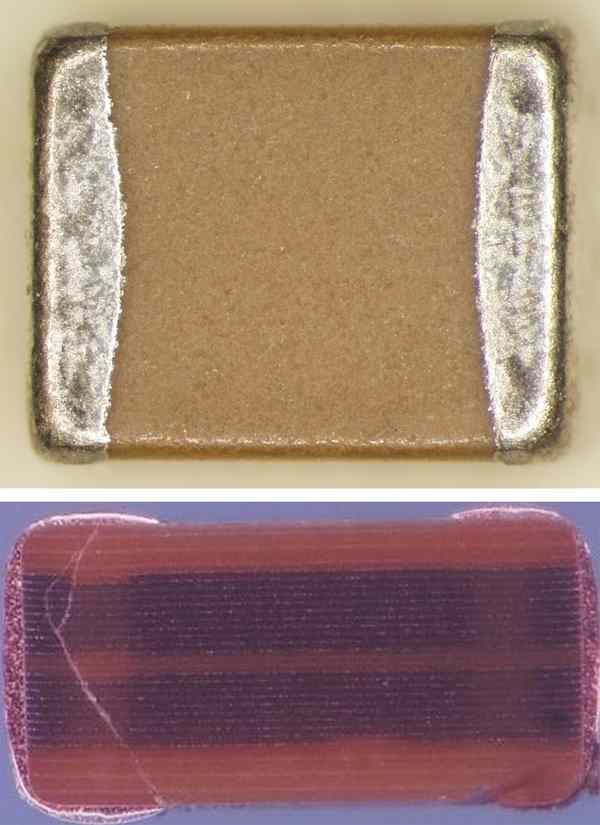
NIST studied 3-mm-long capacitors (top), looking for cracks similar to the one shown in the NASA photo (bottom). Credit: NIST/NASA
To test how well it could work, the scientists applied the technique to 41 barium-titanate capacitors (2mm × 3mm) before and after a round of thermal abuse designed to generate cracks in the ceramic.
Using a box furnace, the scientists heated the capacitors to 189°C and then plunged them into ice water, generating surface-breaking cracks in some of the specimens (27 of the 41), the authors write in the report’s abstract.
Then they compared the before and after acoustic measurements to determine if the data revealed noticeable differences between measurements for visibly-cracked and non-visibly-cracked capacitors.
“The nonlinear acoustic results were strongly correlated with the presence of visible cracks: Measurements on 25 of the 27 visibly cracked capacitors yielded results that were outside the range of those for capacitors without cracks,” according to the NIST release.
While not perfect, the authors say these results show the potential of the method to reliably detect cracks. They call it a “promising approach,” meaning that the results could pan out with further tweaking and optimization of the method.
And, because the authors also noticed consistently different measurements in the non-visibly-cracked capacitors, the authors think that, with further research, the method could identify subsurface cracks as well. “Potential causes of such a shift include quenching-induced changes in ferroelectric-domain structure and the presence of small cracks that were not optically detected,” the authors write in the paper.
In addition to ceramic capacitors, the researchers also say that the method may help detect structural anomalies in other materials as well.
According to the release, the scientists are continuing the research with a capacitor manufacturer, noting that additional work is needed to quantify detection levels of the technique.
The open-access paper, published in conference proceedings from the 2015 Annual Review of Progress in Quantitative Nondestructive Evaluation, is “Time-domain analysis of resonant acoustic nonlinearity arising from cracks in multilayer ceramic capacitors” (DOI: dx.doi.org/10.1063/1.4940511).
Author
April Gocha
CTT Categories
- Electronics
- Material Innovations