[Image above] Schematic of SAM (Sample Analysis at Mars) soil and atmospheric analysis unit, part of Curiosity’s Mars Science Laboratory. Credit: NASA.
If you have spent any non-shopping time on the Internet over the last week, chances are you probably read or heard something about a pesky interview National Public Radio correspondent Joe Palca did with the principal investigator of the NASA Mars Curiosity rover mission, John Grotzinger, in which the latter mentioned that something remarkable popped up in a recent Martian soil sample—remarkable enough for Grotzinger to tell Palca, “This data is gonna be one for the history books. It’s looking really good.”
Grotzinger refused to elaborate even a smidgeon, begging off any details for NPR or any other news outlet until the tests could be confirmed. This, unsurprisingly, set off all sorts of speculation about what is up NASA’s sleeve that has ranged from the reasoned to the wild to the humorous (insert your own DB Cooper, Jimmy Hoffa or birth certificate joke here).
The mystery behind Grotzinger’s comments is expected to be revealed in the near future, and he and Palca probably hope it’s sooner rather than later because both have received substantial criticism for whether they exceeded the professional bounds of science and journalism by letting this quasi-story see the light of day. In fact, details may be forthcoming next week when an announcement is expected at a press conference at American Geophysical Union Annual meeting, but NASA yesterday formally attempted to lower expectations.
Regardless of what NASA eventually reveals, it turns out there is a piece of ceramic, formed by an additive manufacturing process—stereolithography—that will have played a significant role in the soil analysis. This piece is a special alumina ceramic heater housing produced by Technology Assessment and Transfer Inc., a small defense and government contractor based in Annapolis, Md.
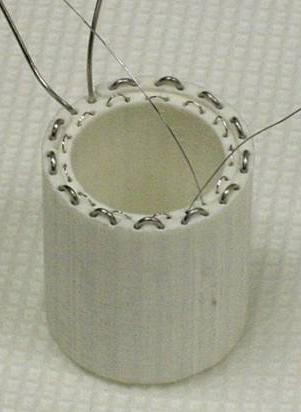
Alumina heater housing formed via stereolithography. Credit: TA&T Inc.
The ceramic heater housing is an indispensable component of the rover’s SAM (Sample Analysis at Mars) instrument suite. SAM’s meat-and-potatoes work occurs when volatile materials from the Mar soil samples are fed into the suite’s six-column gas chromatograph, a quadrupole mass spectrometer and a tunable laser spectrometer.
However, before the GC, QMS and TLS can do their important work, the soil must be carefully prepared to release the volatile components—and that is where the ceramic heater body comes in. It is a dimensionally small-but-central part (only 0.75″ long with an external diameter of 0.5″ and an internal diameter of 0.38″) of several ovens in SAM’s Sample Manipulation System where solid phase materials are sampled by transporting finely sieved materials to one of 74 SMS quartz sample cups. The cups are inserted into the special oven and heated to release volatiles. The ovens also help clean the cups for reuse.
While one might assume that the alumina housing fabrication was simple, it was not. NASA engineers designed it to support a network of channels with 52 heating elements allowing it to serve as an oven capable of reaching 1,000°C.
In an email interview with me, Walter Zimbeck, manager of TA&T’s Ceramic Micro Devices Group, described some of the details and considerations about making the oven housings via the stereolithography route:
What was the compelling reason for using stereolithography versus some alternative rapid prototyping technique?
Zimbeck: I never heard that they had found other ceramic rapid prototyping suppliers to bid on the parts, maybe back in the 2007 timeframe there were not any others. Goddard did have some prototypes made by plasma spraying alumina onto a mandrel and around pre-placed heating element wires, but apparently those prototypes failed during the first heating cycle (room temperature to ~1,000°C in several minutes). The ceramic cracked and the wires broke.
That’s a very challenging thermal shock event for any ceramic, so I was actually surprised that our fully dense high purity alumina housings showed no signs of degradation after the first, nor after many test cycles. The NASA pyrolysis oven team was elated because they were on the hook to provide the ovens and had no other solutions.
The difficult part (why no conventional processes were viable) is the high aspect ratio holes that run the length of the cylinders. The inner ring of holes have a 0.008″ diameter and are ~0.75″ long — an aspect ratio of almost 100! The outer ring is larger diameter (~0.002″). The other challenging feature is the minimum wall thickness between holes and between the holes and inner & outer walls of the oven is 0.010″. Goddard was not able to find anyone who would bid the design using conventional ceramic machining, injection molding or extrusion plus machining.
Once the piece is initially formed via stereolithography, does it need to be sintered or modified in any way?
Yes, definitely. When it comes out of the stereolithography machine it’s a green-state ceramic and must go through binder burnout and sintering, analogous to an injection-molded ceramic. The material we used for the ovens is a fine-grained, high-purity alumina that sinters very well to near theoretical density.
Prior to debinding, the parts also have to be cleaned of the uncured resin [which accumulates during the stereolithography process]. It turned out this required “good hand skills” to ensure the small holes were cleared. We initially used summer interns who were top-notch ceramic engineers from really good university material science programs, but they kept breaking the parts. We eventually assigned the detailing work to two technicians who were recent graduates of Maryland Institute College of Art in Baltimore. They had great hand skills and were very attentive to detail. They really made the process work. The [stereolithography] machine is a high-tech marvel that can make high-quality ceramic parts (relative to other additive manufacturing processes), but you still need good people to maintain that quality throughout the process.
How many of the heater housings did TA&T prepare?
We probably delivered 30 total parts over a year and half period from 2006–2008. There were two or three design iterations they made during that time, which is an advantage with ceramic stereolithography because it’s a tool-less process.
Overall, what’s the experience been like working on this project?
[NASA’s] lead technician for the pyrolysis ovens came by our facility often since we are located less than an hour from Goddard. It was fun, we felt like we were part of the pyrolysis oven team, so when we Curiosity landed successfully, we were pretty excited—parts we made are on freakin’ Mars! Our excitement is amped up further now that we know the pyrolysis ovens are working and they may be essential to producing significant scientific findings.
I don’t mean to imply that the heater housing is the only ceramic-oriented component on Curiosity (if nothing else, the rover is filled with semiconductors). Further, many of the analytical components in the SAM system (and in Earth-based labs working to troubleshoot and confirm Curiosity’s findings) were contributed by companies familiar to ceramists and other materials scientists and engineers. For example, if the following brief video shows frequent glimpses of equipment made by Netzsch Analyzing and Testing:
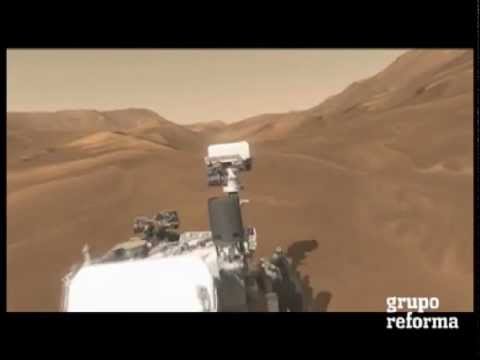
Credit: Netzch Analyzing and Testing; YouTube
CTT Categories
- Aeronautics & Space
- Manufacturing
- Refractories
- Thermal management