[Image above] Morphology of 3D‐printed scaffolds: A) green bodies after 3D printing and B) glass‐ceramic samples after heat treatment at 1,000°C. Credit: Elsayed et al., Journal of the American Ceramic Society/Wiley
It is a rare pleasure to read a journal article that brings together diverse emerging technologies and is written in a style easily understood by the nonexpert. “Biosilicate® scaffolds produced by 3D-printing and direct foaming using preceramic polymers” does just that.
Having recently returned from Ceramics Expo, I am very interested in methods for improving ceramic and glass manufacturing. When I found this article, which provides insights into manufacturing glass-ceramics in a sustainable fashion for biomedical applications, I immediately thought ahead to the International Congress on Glass and GFMAT-2/Bio-4, two conferences that include talks and sessions on such topics. This article gives a look at one important way to improve ceramic and glass manufacturing, and it is therefore at the forefront of relevant ceramics research and development.
Bioactive glass is an emerging technology that has many properties required for effective tissue engineering, particularly bone replacement. Unfortunately, bioactive glasses are limited by their inherent brittleness.
One method for improving the mechanical properties of bioactive glass—crystallization to glass-ceramic—can lead to reduced or delayed bioactivity, thus hindering growth of new bone. Fortunately, researchers have found a way to successfully form partially or fully crystalline bioactive glass-ceramic without losing bioactivity.
Biosilicate® glass-ceramics were specifically conceived to successfully unite the bioactivity of glass with the strength of glass-ceramics. The starting glass formulation is close to that of “gold standard” Bioglass® 45S5, and controlled double-stage heat treatments causes the glass to undergo internal crystallization.
In addition to Biosilicate glass-ceramics retaining biocompatibility and antibacterial properties comparable to Bioglass, these glass-ceramics also ensure easy machinability and workability. Bioactive glasses cannot be produced in complex shapes nor foams in a cost-effective manner, and so are limited commercially to powder, granule, or small monolith forms. In contrast, Biosilicate glass-ceramics allow manufacturers to obtain different geometries, albeit through expensive post-processing.
The study conducted by researchers from the University of Padova (Italy), the National Research Centre (Egypt), the Federal University of São Carlos (Brazil), and The Pennsylvania State University aimed to explore the low-cost fabrication of bioactive glass-ceramics with complex geometries and foams.
In their study, the researchers, including ACerS Fellows Edgar D. Zanotto and Paolo Colombo, used polymer-derived ceramics (PDCs) to obtain bioactive glass-ceramic scaffolds through 3D-printing and direct foaming. PDCs have the potential to reduce raw material and processing costs and cut emissions of volatile organic compounds. Also, the single-step firing of PDCs shorten cycle times and improve reproducibility.
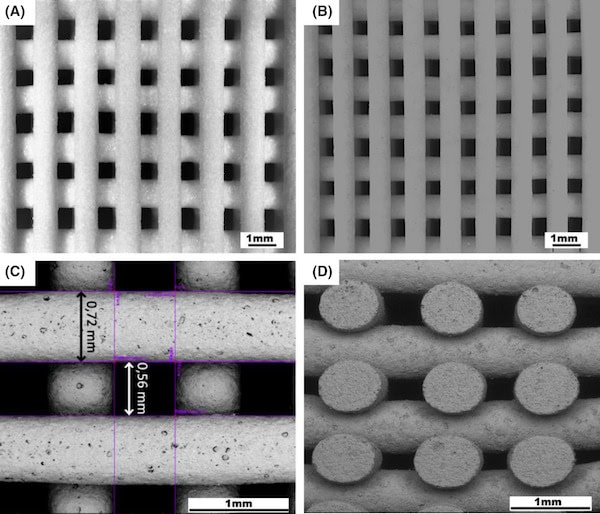
Structure of 3D-printed scaffolds: A) Before firing (preceramic) top view; B) After firing (ceramic) top view; C) Details of line size and spacing after firing; D) After firing edge view. Credit: Elsayed et al., Journal of the American Ceramic Society/Wiley
Starting from inexpensive commercial silicone resins, calcium and sodium carbonates, and sodium phosphate dibasic, the researchers produced compositions similar to Biosilicate. They then employed direct-ink 3D-printing and direct foaming to create complex glass-ceramic scaffolds and molded foams.
Their fired test parts had high porosities (60 to 75 percent) and compressive strengths around 7 MPa for scaffolds and in the range of 1.5–6 MPa for foams. As the researchers note in their conclusion, “we demonstrated that preceramic polymers containing suitable oxide precursor fillers could be employed for the direct synthesis of Biosilicate glass‐ceramic in a fast and simple route, with nearly identical crystalline phases.”
Want to read more about advances in glass and glass-ceramics? Read more here about glass science and technology in the ICG2019 Conference Collection, which is a compilation of recent articles written by the conference leaders.
The paper, published in Journal of the American Ceramic Society, is “Biosilicate® scaffolds produced by 3D-printing and direct foaming using preceramic polymers” (DOI: 10.1111/jace.15948)
Author
Jonathon Foreman
CTT Categories
- Biomaterials & Medical