[Image above] Alloyed metals being poured from a furnace into a ladle, to be used to fill molds. Credit: Zachary Sims; ORNL
About a year ago, the only rare-earth mine in the U.S. filed for bankruptcy. Domestic rare earth production became doomed.
But not because rare earths aren’t in demand—quite the opposite, actually. They’re in high demand because the materials find use in so many high-tech applications, including solar cells, consumer electronics, hybrid cars, and much more.
However, the rare-earth market isn’t so favorable. For one, China controls the market, mining and exporting the bulk of the world’s supply. The country supplies some fierce competition, and, to add insult to injury, it’s willing to tighten and loosen its hold on the market supply completely at will, throwing an air of unpredictability into the landscape.
Rare-earth mining operations can also be very unfriendly to the environment. And—if that wasn’t enough—despite the demand for rare earth minerals, profitability can be tricky.
That’s because a bulk of the minerals mined from rare-earth mixed ores aren’t the super valuable ones—those come in small supplies. The bulk of most rare-earth ores is composed of cerium and lanthanum, materials that aren’t invaluable but that don’t have much in the way of high-volume applications.
So mining and processing enough rare-earth ores to produce marketable amounts of other, more valuable rare earths means that there’s often a hard-to-market pile of cerium and lanthanum in the background.
The rare earth content of most mined rare earth ores is up to half cerium, according to Oak Ridge National Lab (Oak Ridge, Tenn.). “The United States’ most common rare earth ore, in fact, contains three times more cerium than neodymium and 500 times more cerium than dysprosium.”
So what if we could make new uses for those piles of the most abundant minerals mined form rare-earth ores?
Scientists at Oak Ridge, Lawrence Livermore National Lab (Livermore, Calif.), and Eck Industries (Manitowoc, Wis.) are doing just that. Together, the team has developed a new super-strong aluminum alloy that incorporates cerium, providing a potentially significant use for that surplus—and it just may be able to make mining of rare-earth elements here in the United States a go again.
“The aluminum industry is huge,” ORNL scientist Orlando Rios says in an ORNL press release. “A lot of aluminum is used in the auto industry, so even a very small implementation into that market would use an enormous amount of cerium.” Rios says that incorporating cerium into just 1% of the aluminum alloy market means equates to a use for 3,000 tons of cerium.
In addition to creating a market value for cerium, however, the new alloy also offers some important material benefits—namely higher heat tolerance.
That heat stability is because aluminum and cerium form an intermetallic compound inside the alloy as it melts, and that intermetallic has a high melting point above 2000ºF.
Because it’s so stable at high temperatures, the team thinks the alloy could be particular useful in internal combustion engines.
Tests show the aluminum–cerium alloy is stable at 300ºC, the researchers report, and is lighter than traditional materials used in the hot parts of engines, such as cast iron. So engines could not only run hotter, which means more efficiently, but also would weight less—affording fuel and energy savings in itself.
In addition to being really heat-tolerant, another important attribute of the new alloy is that it’s easy to work with.
“Most alloys with exceptional properties are more difficult to cast, but the aluminum–cerium system has equivalent casting characteristics to the aluminum–silicon alloys,” David Weiss, vice president for engineering and research and development at Eck Industries, says in the ORNL release.
The scientists have already cast prototype cylinder heads for an aircraft and electric generator by pouring the new castable alloy into 3-D-printed sand molds. They even tested the parts in a test engine, which handled exhaust temperatures that reached over 600ºC.
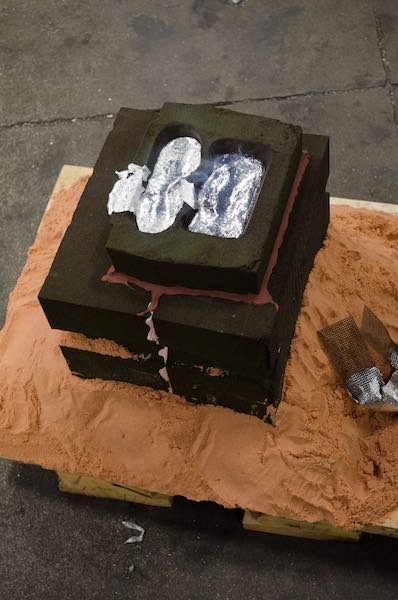
Green sand mold of an aerospace engine head. Molten metal is poured in and allowed to cool. Credit: Zachary Sims; ORNL
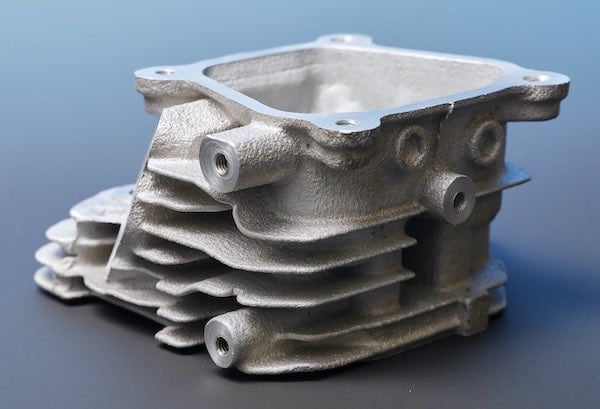
Aluminum–cerium–magnesium engine head. Credit: Carlos Jones; ORNL
At a time when many scientists are evaluating alternative sources of rare earths and alternatives to rare earths themselves, rare-earth mining in the U.S. just might get a second wind.
The research paper, published in JOM, is “Cerium-based, intermetallic-strengthened aluminum casting alloy: High-volume co-product development.”
Author
April Gocha
CTT Categories
- Electronics
- Energy
- Environment
- Manufacturing
- Material Innovations
- Thermal management