[Image above] Scanning electron microscope images revealed that magnesium aluminate spinel created from fused magnesia experienced improved bending strength after thermal shock because of grain refinement. Credit: Wu et al., International Journal of Applied Ceramic Technology
As manufacturers are well aware, the techniques used to synthesize or shape a material can significantly impact the final product’s properties. Yet even before those steps in the fabrication process, manufacturers must pay close attention to their starting materials.
Starting materials, or the substances used to produce a product, can portend poor properties if they are of low quality. But it is not only the starting material’s quality that can impact properties—so can its source.
Starting materials can often be derived from different sources. For example, lithium can be extracted from both brine (highly concentrated saline groundwater) and ores (hard rock mining). The product of both brine and ore-based lithium extraction is most often lithium carbonate, but in the latter case, it can result in lithium hydroxide as well.
Lithium hydroxide is better suited for battery production than lithium carbonate because it decomposes at a lower temperature. In this case, then, ore-derived lithium is a better starting material than brine-derived lithium, even if both materials are of equally good quality.
The impact that material source has on a product’s properties is generally less studied than other factors. In a recent study, researchers from Wuhan University of Technology in China considered this factor by exploring the effect of different magnesium sources on the production of magnesium aluminate spinel (MgAl2O4).
Magnesium aluminate spinel is a widely used refractory oxide that often serves as the lining in steel-making furnaces or cement rotary kilns. This material is rarely available in nature, and so is synthetically prepared through different routes using various starting materials.
As a 2022 review paper shows, there is much research on how synthesis techniques can affect the properties of magnesium aluminate spinel. But fewer studies have explored the effect that starting materials have on the final material’s performance.
The researchers of the new study evaluated the effect of using three common sources of magnesium to create magnesium aluminate spinel.
- Magnesite: a naturally formed magnesium carbonate mineral (MgCO3).
- Fused magnesia: a magnesium oxide that is manufactured by melting and recrystallizing the starting materials (often magnesite or calcined magnesia) in an electric arc furnace.
- Light burned magnesia: a magnesium oxide obtained by calcining a magnesium ore, i.e., thermally treating it to remove volatile substances or to oxidize a specific amount of mass.
In addition to the three magnesium sources, α-Al2O3 (aluminum source) and kaolin (additive) were used as starting materials. All samples were prepared via the pressureless sintering method.
As can be seen in the scanning electron microscope images, there were noticeable differences in the phase composition and microstructure of each magnesium aluminate spinel sample depending on which magnesium source was used and if kaolin was added.
- Fused magnesia-based samples. For the sample without kaolin (A1), there is no amorphous silica phase in the fracture surface, pores are difficult to observe, and grains are similar in size. For the sample with kaolin (A4), the fractured surface is covered by an amorphous silica phase, pores are clearly observed, and large grains are surrounded by small grains.
- Magnesite-based samples. For the samples both without (A2) and with (A5) kaolin, pores and an amorphous silica phase are observed.
- Light burned magnesia-based samples. For the samples both without (A3) and with (A6) kaolin, the number of pores increased compared to the magnesite-based samples, and an amorphous silica phase formed as well.
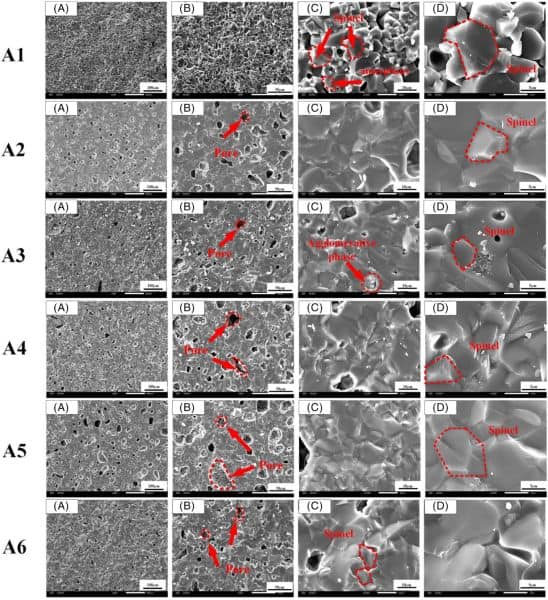
Scanning electron microscope images of the fractured surface of magnesium aluminate spinel samples fired at the optimal temperatures. Magnesium sources used for each sample are fused magnesia (A1, A4), magnesite (A2, A5), and light burned magnesia (A3, A6). Samples A1–A3 did not contain kaolin while samples A4–A6 did. Credit: Wu et al., International Journal of Applied Ceramic Technology
These differences in phase composition and microstructure led to the samples exhibiting different physical properties. For example, sample A1, with its compact microstructure, had the highest bulk density (3.31 g/cm3) and outstanding bending strength (104.35 MPa). In contrast, sample A4, with its pores and amorphous silica phase, had a lower bulk density of 3.21 g/cm3.
Perhaps surprisingly, subsequent thermal tests carried out on the samples were not used to determine the spinels’ potential in a traditional application, such as a steel furnace. Instead, the researchers used the results to determine the potential of magnesium aluminate spinel as a solid thermal storage material.
Current thermal storage systems for stockpiling solar energy are typically based on liquid-phase materials, such as water, heat transfer oil, and molten salt. It is believed that solid-phase materials could improve the working temperature and efficiency of thermal storage systems.
Several ceramics have been investigated as thermal storage materials, such as mullite, cordierite, anorthite, and silicon carbide. This study adds magnesium aluminate spinel to the list.
The researchers determined that the kaolin-free sample created from fused magnesia (A1) demonstrates the best properties for thermal storage applications. Specifically, the bending strength of the sample increased by 7.71% after 30 thermal shock cycles, plus the specific heat capacity reached 1.05 J/(g • K).
“Therefore, the MgAl2O4 ceramics exhibited great potential as high-temperature thermal storage materials,” the researchers conclude.
The paper, published in International Journal of Applied Ceramic Technology, is “Preparation of MgAl2O4 solar thermal storage ceramics from different magnesium sources” (DOI: 10.1111/ijac.14407).
Author
Lisa McDonald
CTT Categories
- Basic Science
- Manufacturing