[Image above] Oobleck, seen above, is an example of a shear-thickening fluid, a material that can complicate manufacturing by jamming pumping and mixing equipment. Could acoustics make these fluids easier to handle? Credit: The Slow Mo Guys, YouTube
As a former high school tech crew nerd, when I hear the word “acoustics,” I think of how walls are constructed and mics are designed to optimize sound quality in the theater. In my world, materials were manufactured to improve acoustics. It did not occur to me that acoustics could be used to manufacture other materials.
In June, I looked at how Australian researchers used acoustics to fabricate metal-organic frameworks. Now, four researchers from Cornell University have used acoustics to manipulate a different material—dilatant fluids.
Dilatant fluids, commonly termed shear-thickening fluids, are a type of non-Newtonian fluid in which viscosity increases with the rate of shear strain. Oobleck, a popular grade-school project made from cornstarch and water, is a good example of a dilatant fluid—it flows like liquid when poured slowly but solidifies when squeezed or sheared.
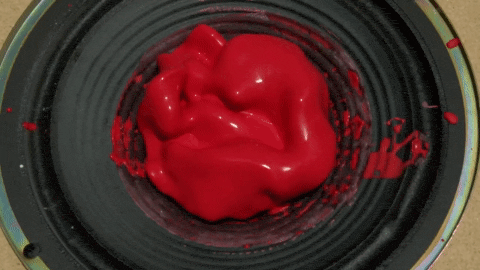
In this video by The Slow Mo Guys, you can see Oobleck return to its fluid state once external strain is removed. Credit: The Slow Mo Guys, YouTube
In addition to grade-school projects, dilatant fluids have more practicable applications as well, including in soft body armor and astronaut suits. But in some applications, such as food processing and 3D printing of ceramics and metals, dilatant fluids are troublesome.
The more a dilatant fluid is manipulated, the more it solidifies. So in applications that involve pumping and mixing fluids, this property can lead to blocked nozzles and jammed hoppers.
Itai Cohen, professor of physics at Cornell University, and collaborators previously found perpendicular oscillation could break apart the rigid structures (“force chains”) formed by particles in dilatant fluids, making the fluids flow more easily. However, designing a shakable, twistable factory pipe is not easy and thus renders this approach impractical.
In the recent paper, Cohen and Ph.D. student Meera Ramaswamy partnered with Meinig Family Professor of Engineering Brian Kirby and Ph.D. student Prateek Sehgal to test a different approach to breaking apart the force chains, an approach based on acoustic transducers.
Before this collaboration, Kirby and Sehgal were using acoustic transducers to manipulate microscale and nanoscale particles in Kirby’s lab. “We started by solving a biological problem, which was how do we use acoustics to separate out different nanoparticles of different sizes?” Kirby says in a Cornell press release. “This [shear-thickening research] was closely related. Rather than having a very sparse suspension of tiny little particles and trying to move them to a specific spot, now you have a very dense suspension of many particles, and you’re trying to change its material properties.”
For their experiment, the researchers placed their dilatant fluid, a dense silica colloidal suspension, on an aluminum plate bonded to a piezoelectric disk. Then, they generated acoustic perturbations by exciting the piezoelectric crystal.
“As hypothesized, the viscosity response of the thickened suspension depends sensitively on the acoustic perturbations,” they write in the paper.
In particular, they found a threshold-like behavior at very low powers, “where the viscosity decrease is very slow and negligible up to powers ~5 mW.” Beyond that threshold, viscosity initially decreased rapidly at powers up to about 0.08 W, after which the viscosity decreased more slowly again.
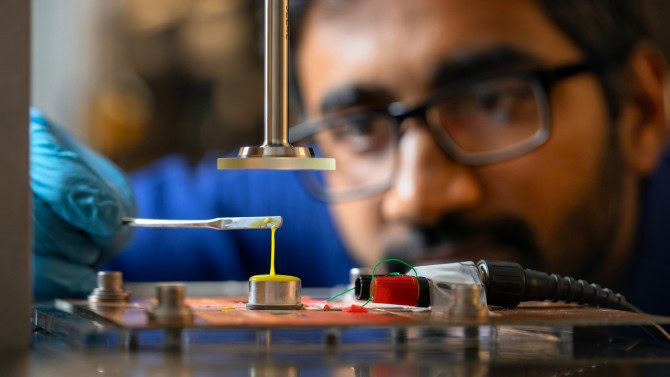
Doctoral student Prateek Sehgal manipulates the viscosity of shear-thickening materials by using an acoustic transducer—called a piezo—that generates ultrasonic waves. Credit: Jason Koski, Cornell University
“This non-linear evolution suggests that although a higher power is required to completely eliminate the thickening effects of force chains, a large fraction of dethickening can be achieved by just small input power,” they conclude.
In the press release, Cohen explains the importance of this discovery. “This is the key insight that allowed us to think about applying these kinds of perturbations and getting it to work,” he says. “Basically, any geometry where you have a flow that’s thickened, you can now just slap a piezo on and dethicken that region. This strategy just opens up the applicability to a much broader range of applications.”
While the researchers experimented on dilatant fluids up to 1.3 mm thick, Kirby anticipates the technique being used on pipes as wide as 1 ft because of ultrasonic waves’ ability to propagate long distances in material.
“Overall, our method has laid a strong foundation to robustly design smart transport systems that handle shear-thickening fluids,” the researchers conclude in the paper.
The paper, published in Physical Review Letters, is “Using acoustic perturbations to dynamically tune shear thickening in colloidal suspensions” (DOI: 10.1103/PhysRevLett.123.128001).
Author
Lisa McDonald
CTT Categories
- Basic Science
- Manufacturing