[Image above] Bioglass encapsulated RFID devices are great for tracking pets, but not so great for tracking animals that butt heads. How can bioglass capsules be made less brittle? Credit: Godwingk, YouTube
What do electronic toll payment devices, inventory control tags, and “chips” for pets have in common? All use radio frequency identification (RFID) transponders to store and transmit important information.
RFID devices are widely used in data storage applications, as they have larger memories than barcodes. In RFID devices, a transponder receives power via electromagnetic radio waves emitted by an electronic reader, and then the transponder sends back the requested information to the reader.
You might think this blog post is about some cool new ceramic used for the RFID device. But it’s not. It is about the container used to protect the device. Specifically, the bioglass capsule protecting transponders in RFID devices used for tagging animals.
You probably have seen pictures of livestock with ear tags. These tags do not work very well for highly active animals, such as household pets and large animals, in their natural habitats. In these cases, RFID devices are implanted into the animals. Not only must the implanted container protect the device from physical damage and corrosion, it must also be biocompatible to prevent harming the animal.
Bioglass meets these requirements, and bioglass encapsulated RFID devices have been successfully deployed in pets for quite some time. But the brittleness of bioglass is a serious shortcoming when implanted into animals that butt heads for dominance, like sheep and oxen.
Unfortunately, there is not a wealth of information on the mechanical properties of bioglass in general, and of the capsule configuration specifically. However, a recently published article helps fill that knowledge gap.
Researchers from Florida A&M University took on the challenge of understanding the causes of the high failure rates of trackers implanted in blackbuck antelopes at a local wildlife preserve. Their findings are published in the most recent issue of the International Journal of Ceramic Engineering & Science (IJCES).
Because of the very strong atomic bonding within ceramics and glasses, the primary failure mode in these materials is crack propagation (growth) to relieve internal stresses that arise from external forces. A significant challenge of failure testing in ceramics is separating material properties from conditions created by design and processing of physical parts.
Given the complexity of transponder design, the researchers chose three-point bending for failure testing. Even with specially designed clamps and static loading, they noted a wide variation in flexural strength of the bioglass capsules.
With the flexural strength of the capsule, and the peak forces produced by the antelope while fighting, the researchers used finite element analysis to stress maxima within the capsules. They used three different force distribution models to represent possible force modes in the animals:
- Three-point bending for a single point of external contact on a capsule perched on two bones,
- Forces distributed across both sides for broad contact on a capsule laying on a flat spot, and
- Force distributed on one side against two contact points to simulate a mixture of the other two situations.
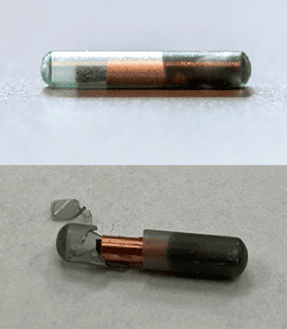
Top: Photograph of a Bioglass 8625 transponder capsule. Bottom: Photograph after the capsule fractured during testing. Credit: Carnrike et al., International Journal of Ceramic Engineering & Science (CC BY 4.0)
Not surprising, all models show that stresses in the capsule exceeded the flexural failure strength when the maximum fighting force is applied. Interestingly, all three models also showed stress concentration at the ends of the capsules where the tube meets the hemispherical cap. However, the capsules broke more toward the middle of the capsule than at the ends, which is predicted by the distributed force models.
The researchers proposed and tested several new designs for the capsules to improve reliability by reducing the internal stresses. One design emerged that met the dimensional requirements for the transponder while reducing stresses to below the failure strength limits.
I chose to write about this article for several reasons. One, the header photo is fascinating and caught my interest immediately. Two, the application is real and useful. The work exemplifies a sound engineering study focused on solving a specific challenge and proposing a workable solution. Three, the methodology used can be applied to similar challenges in other fields. (Had Tesla performed similar testing and modeling, they may have avoided this embarrassing event.)
For these reasons, this article has significant value for ceramic engineers and I’m glad that ACerS now has a platform for publishing this level of research report.
You can read the full article online at https://doi.org/10.1002/ces2.10027. All articles in IJCES are open access, meaning anyone anywhere with an internet connection can download and read the article for free (no membership, subscription, or paywall payment required).
For more information about IJCES, visit “Overview” under the “About” menu on the IJCES page on ACerS Publication Central, or click this link for quick access.
The open-access paper, published in the International Journal of Ceramic Engineering & Science, is “Understanding the failure of Bioglass 8625 transponder capsules used in tracking blackbuck antelopes” (DOI: 10.1002/ces2.10027).
Author
Jonathon Foreman
CTT Categories
- Basic Science
- Biomaterials & Medical
- Glass