[Image above] Example of a metal-free zirconia dental bridge. Partially stabilized zirconia demonstrates superior mechanical behaviors compared to other biomedical ceramic materials, but obtaining accurate measurements of its fracture toughness can be challenging. Credit: Bin im Garten, Wikimedia Commons (CC BY-SA 3.0)
As average life expectancy for people continues to increase globally, medical procedures that ensure we live our best life grow in importance as well.
One increasingly common group of procedures is restorative dentistry, or management and procedures that keep someone’s mouth healthy and functional, such as putting in dental implants, dentures, fillings, and crowns.
One material used extensively in restorative dentistry in the past 20 years is zirconia, a naturally occurring white crystalline oxide of zirconium. This biocompatible oxide was first discovered in the 18th century, but it took more than 150 years before its use in medical applications began to take off.
Zirconia in medicine: A brief history
Zirconia most often forms in a monoclinic crystalline structure, but upon heating, zirconia starts transforming from the monoclinic phase to a tetragonal phase (between 1,170–2,370°C) and a cubic phase (above 2,370°C).
In 1972, Ronald C. Garvie and Patrick S. Nicholson at McMaster University found they could stabilize the tetragonal and cubic phases of zirconia by alloying it with oxides like calcia, yttria, and magnesia. This partially stabilized zirconia demonstrated remarkably good mechanical properties—and opened the door to zirconia’s use in medical applications.
Partially stabilized zirconia started being used as an alternative to cobalt-chrome alloy in hip and knee replacements in the 1980s. And in the 1990s, such zirconia broke onto the dental scene as material for endodontic posts, i.e., restorations that help restore or reinforce damaged tooth structure and root systems.
Today, zirconia—typically yttria-stabilized zirconia—is often used in dental crowns and bridges, and much research looks to establish dental implants made out of zirconia as an alternative to titanium implants, the current gold standard.
Fracture toughness of zirconia: Achieving a reliable measurement
As mentioned above, one reason for the adoption of yttria-stabilized zirconia in dental applications is its superior mechanical behaviors compared to other biomedical ceramic materials. However, accurately measuring zirconia’s fracture toughness, or its resistance to crack extension, can be challenging.
Typically, fracture toughness of advanced ceramics is measured using one of the three methods introduced in ASTM C1421–18: single-edge pre-cracked beam (SEPB), surface crack in flexure (SCF), or single-edge V-notched beam (SEVNB). But for yttria-stabilized zirconia, the SEVNB method is not recommended.
“For the SEVNB method to be comparable to other standard methods, such as the SEPB and SCF methods, it is critical to create a notch-tip that closely approximates a sharp crack,” researchers write in a recent open-access paper. However, due to yttria-stabilized zirconia’s fine grain size of a few hundred nanometers, “machining a notch-tip radius of sufficient sharpness in 3Y-TZP [3 mol% yttria stabilized tetragonal zirconia polycrystal] for the SEVNB method [is difficult].”
The researchers come mainly from the American Dental Association Science & Research Institute in Chicago. And in collaboration with a colleague from Argonne National Laboratory, they explored preparing yttria-stabilized zirconia samples for SEVNB measurements by creating nanometer-sized notches using focused ion beam (FIB) milling.
FIB is a technique commonly used in the semiconductor industry but is gaining use in biological fields. It involves using a focused ion beam to either image a sample (low beam) or sputter/mill small volumes of materials at specified locations (high beam).
Use of FIB to improve fracture toughness measurements of dental ceramics was first reported in 2008, when researchers in Germany reported fracture toughness test results from FIB-notched ceria-doped zirconia. In the recent paper, the researchers note rapid progress of instrumentation has made FIB systems more accessible in both academia and industry today, and thus they wanted to investigate preparing zirconia samples using FIB milling as well.
They created a V-shaped notch at the center of each yttria-stabilized zirconia specimen before sintering using a modified saw blade technique. After sintering, they added an additional notch to six of the 11 specimens using the FIB technique.
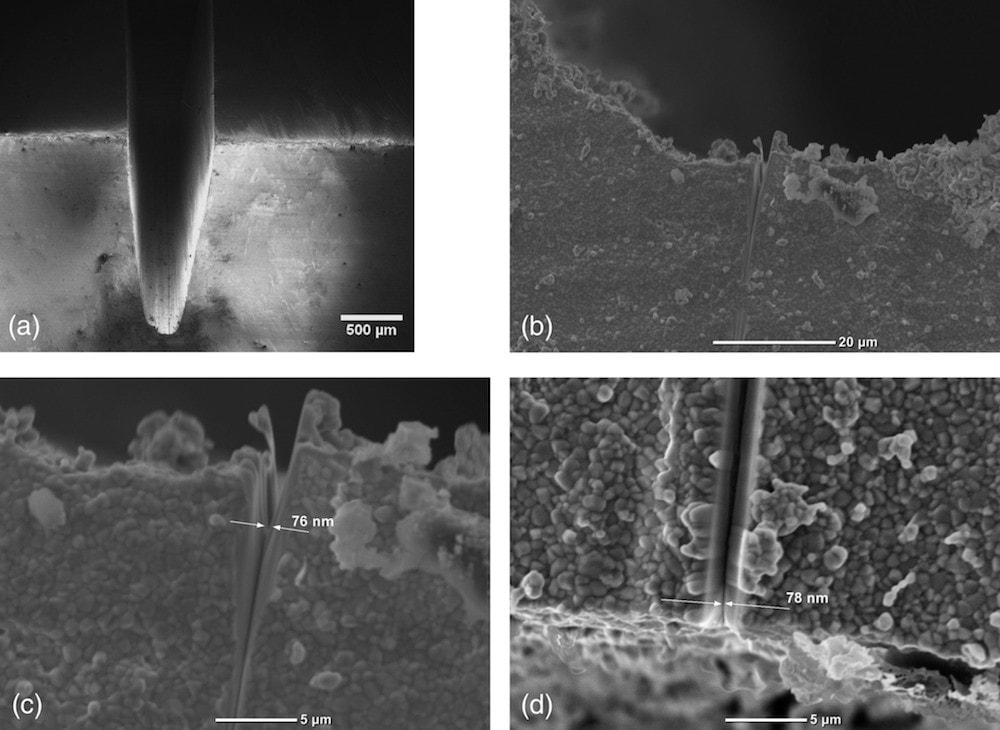
SEM images of the V-notch with additional FIB-notch milled into the center. (a) Overview of the V-notch. (b,c) Side views of the FIB-notch at higher magnifications. (d) Top view of the V-notch with FIB-notch in the center. Credit: Liao et al., Journal of Biomedical Materials Research Part B: Applied Biomaterials (CC BY 4.0)
Analysis of the samples found the FIB-notched specimens demonstrated lower fracture toughness values (5.64 ± 1.14 MPa√m) compared to specimens with saw blade‐notches only (8.90 ± 0.23 MPa√m). This finding aligned with the results from the 2008 study, which also observed a decrease in fracture toughness values as notch root radius decreased.
In 1994, round robin testing on the same type of yttria-stabilized zirconia using the SCF method yielded a fracture toughness of 4.36 ± 0.44 MPa√m. This finding would appear to support the hypothesis that FIB-notched samples are more accurate than traditionally notched samples. “However, it is not possible to make conclusive statements about the comparability of this method with other standard methods, such as the SCF and SEPB methods, without further testing,” the researchers write.
In the discussion section, the researchers note one factor that may be affecting measurements of FIB-notched specimens is the formation of a 20–30-nm thick amorphous layer as a result of ion bombardment. Fortunately, Raman analysis showed another factor the researchers feared may contribute to inaccurate measurements—introduction of a monoclinic phase by FIB milling—did not occur at detectable levels.
Though further testing is needed to fully understand the effects of notch geometry on measurements, as well as comparability of the FIB-milling technique with other methods, “FIB‐milling may be promising as a technique to generate nanometer-sized notches in ceramics for fracture toughness measurements,” they conclude.
The open-access paper, published in Journal of Biomedical Materials Research Part B: Applied Biomaterials, is “Fracture toughness of zirconia with a nanometer size notch fabricated using focused ion beam milling” (DOI: 10.1002/jbm.b.34668).
Author
Lisa McDonald
CTT Categories
- Biomaterials & Medical