[Image above] Credit: Massachusetts Institute of Technology, YouTube
The healthcare industry has seen a number of advancements in technologies that have improved many medical procedures as well as the overall the health care of patients.
Take robotics, for example.
A paper in Science Robotics last year describes advances in nanorobot design, fabrication, and operation that enabled more targeted drug delivery and enhanced many complex surgical procedures, among other applications.
The paper also describes a variety of actuation mechanisms that researchers have developed in the past several years, including chemical propulsion, optical, thermal, and electrical energy, as well as magnetic actuation.
Now, engineers at Massachusetts Institute of Technology have designed small 3-D printed devices that can wrinkle, fold, crawl, squeeze, grab, roll, and jump—all controlled by a magnet.
Led by Xuanhe Zhao, Noyce Career Development Professor in MIT’s department of mechanical engineering and department of civil and environmental engineering, the researchers created soft flexible structures out of printable ink infused with magnetic particles. The structures move and instantly shift into complex formations, just by controlling the magnetic orientation of individual sections in the structure, according to an MIT news release.
The researchers say the structures hold great promise for use in remote controlled biomedical devices.
“We think in biomedicine this technique will find promising applications,” Zhao explains in the release. “For example, we could put a structure around a blood vessel to control the pumping of blood or use a magnet to guide a device through the GI tract to take images, extract tissue samples, clear a blockage, or deliver certain drugs to a specific location. You can design, simulate, and then just print to achieve various functions.”
Scientists have already explored magnetically activated materials, but according to the MIT researchers, the materials used involved polymers with limited mobility such as this example or this one.
“People have only made structures that elongate, shrink, or bend,” MIT graduate research assistant and coauthor of the paper Hyunwoo Yuk says. “The challenge is, how do you design a structure or robot that can perform much more complicated tasks?”
The team created several structures, including a spider-shaped grabber, a rippling ring, and a self-squeezing tube. The researchers also printed a ring in which they embedded electric circuits with red and green LED lights that are programmed to light up alternately, depending on which way the magnetic field is oriented.
Zhao suggests that others could use their model to develop their own functional structures. “By programming complex information of structure, domain, and magnetic field, one can even print intelligent machines such as robots,” he says.
“There is no ideal candidate for a soft robot that can perform in an enclosed space like a human body, where you’d want to carry out certain tasks untethered,” graduate student and coauthor Yoonho Kim says. “That’s why we think there’s great promise in this idea of magnetic actuation, because it is fast, forceful, body-benign, and can be remotely controlled.”
The paper, published in Nature, is “Printing ferromagnetic domains for untethered fast-transforming soft materials” (DOI: 10.1038/s41586-018-0185-0).
The spider-like device shown in the video looks life-like—as if it were performing tricks on command. Watch the video below and see for yourself!
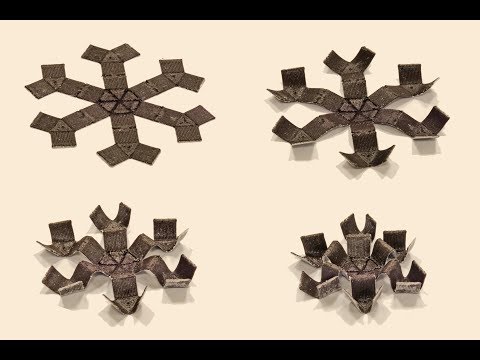
Credit: Massachusetts Institute of Technology, YouTube
Did you find this article interesting? Subscribe to the Ceramic Tech Today newsletter to continue to read more articles about the latest news in the ceramic and glass industry! Visit this link to get started.
Author
Faye Oney
CTT Categories
- Basic Science
- Biomaterials & Medical
- Electronics
- Energy
- Material Innovations
- Modeling & Simulation
- Nanomaterials
Spotlight Categories
- Member Highlights