[Image above] Lead wires (C) disconnected from the ceramic matrix. Two recent papers explore how materials come apart in order to improve ceramic bonds. Credit: Zhu et al., International Journal of Applied Ceramic Technology
William Gibson, leader of cyberpunk fiction movement
When you want to know how things really work, study them when they are coming apart.
What holds things together, especially when they are mismatched like metals and ceramics? How do they come apart? How can we improve the bonding? These are critical questions for applied ceramists and ceramic engineers, particularly with the continuous growth of functional ceramics for electronics and optical applications.
In practical terms, wetting, welding, joining, and coating are all forms of bonding. In technical terms, bonding occurs when different atoms share electrons. Bonds between dissimilar materials come from some form of matching, which can be seen in electron microscope images. Either the atoms line up, as with epitaxial growth, or they become intertwined or entangled, much like a batch of cooked long noodles can come out of the pot in one big mass.
Two articles from the November/December issue of the International Journal of Applied Ceramic Technology report on the issues of bonding while solving problems for different applications of ceramics and glass.
Increase bonding strength by 15-fold
In “Enhancement of bonding strength between lead wires and ceramic matrix of metal ceramic heater,” researchers from Wuhan University of Technology, China Tobacco Hubei Industrial LLC, and University of Science and Technology Beijing explored how heaters failed when the electrical connection (lead) wires were stressed. They found the bond between the tungsten/manganese heater and the alumina support was weak and explored adding alumina/magnesia/silica bonding aids to the metal heater screen-printing ink.
Their experiments resulted in a 15-fold increase in bonding strength, as measured by stress on the lead wires, with only a 10% increase in cold resistance. And while this result is impressive by itself, the researchers also explored the microstructure to determine the mechanisms for the increase.
They found manganese-aluminum spinel formed at the interface of the substrate with the metal. In the strongest sample with alumina/magnesia bonding aid (no silica), it showed the spinel intertwined with the metal to enhance the bonding. It also turns out that the silica complicates the bonding, though you will have to read the article to discover the mechanism for this phenomenon.
The paper, published in International Journal of Applied Ceramic Technology, is “Enhancement of bonding strength between lead wires and ceramic matrix of metal ceramic heater” (DOI: 10.1111/ijac.13319).
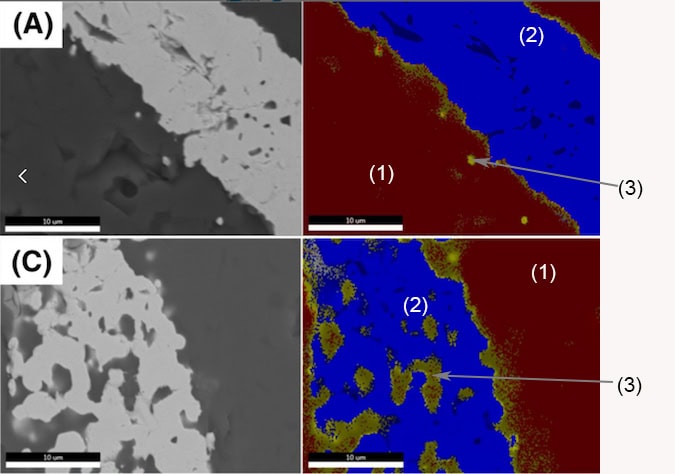
Edge-view backscatter images and element mapping for alumina substrate and metal heater (A) without additives and (C) with alumina/magnesia additive. The images show three phases: the alumina substrate (1, red), the heater metal (2, blue) and the spinel (3, green). Credit: Zhu et al., International Journal of Applied Ceramic Technology
Improve bonding, reduce temperatures
In the next article, “Evolution of interfacial structures and mechanical performance of sapphire and Sn-9Zn-2Al joints by ultrasound,” researchers from Harbin Institute of Technology in China explored ways to improve the wetting of alumina (sapphire) by metal solders while also reducing the soldering temperature. Sapphire is used with many optical devices that can be temperature sensitive. While previous studies used rare earth and precious metal additives to improve bonding and reduce processing temperatures, the researchers used sonication at 20,000 Hz to impart the additional energy needed to form the bonds.
As with the previous article, the researchers explored the strengthening mechanism. In this system the aluminum in the solder formed aluminum oxide (alumina) at the surface of the sapphire. Subsequently, a zinc-aluminum phase (97% zinc) layer formed on top of the aluminum oxide, which acted as a transition from the aluminum oxide to the Sn-9Zn-2Al solder. The researchers found that these processes took a relatively long time, indicating the motion of atoms is required, making these processes diffusion limited.
The paper, published in International Journal of Applied Ceramic Technology, is “Evolution of interfacial structures and mechanical performance of sapphire and Sn–9Zn–2Al joints by ultrasound” (DOI: 10.1111/ijac.13324).
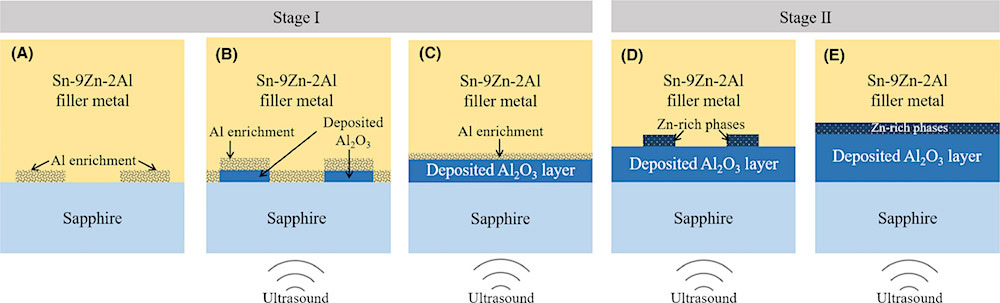
Schematic model of the evolution of the interface microstructure under ultrasound. Credit: Xu, Ma, and Yan; International Journal of Applied Ceramic Technology
I find it fascinating that both studies developed very strong bonding so that the final incidences of failure occurred within the metal. In other words, the ceramic-metal interfacial bond was stronger than the internal strength of the metals.
Thus, the ceramics are no longer the materials that limit the mechanical integrity for these heaters or sapphire-based components. Makes me proud to know we have some awesome engineers.
James Dyson, CEO of Dyson Ltd
Manufacturing is more than just putting parts together. It’s coming up with ideas, testing principles, and perfecting the engineering as well as the final assembly.
Author
Jonathon Foreman
CTT Categories
- Basic Science
- Manufacturing