[Image above] Credit: Michael; Flickr CC BY-NC-ND 2.0
It sounds like an academic research fairy tale—a collaboration born from a conference that crosses institutional and international borders, develops a novel method of experimentation, sees something important that’s never been seen before, and bears a publication in Nature Communications.
But this isn’t a fairy tale—this is real life for University of Central Florida engineering professor Seetha Raghavan.
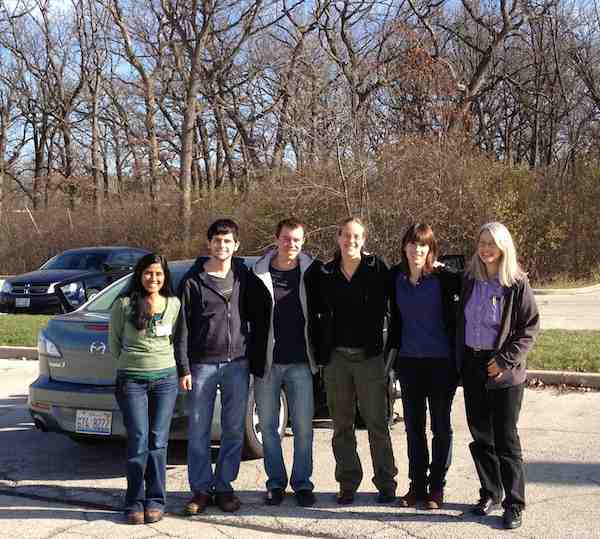
Researchers from UCF and DLR (L to R): Seetha Raghavan, Albert Manero, Kevin Knipe, Janine Wischek, Carla Meid, and Marion Bartsch. Credit: DLR; UCF
Raghavan and a team of researchers from the Institute of Materials Research at the German Aerospace Center (DLR), Argonne National Laboratory, and Cleveland State University have succeeded in capturing a glimpse into the ceramic coating that protects aircraft engines from the extreme thermal cycling and mechanical strain they encounter with every flight.
Turbine engines work most efficiently when the combustion gases that enter the turbine are hot—really hot. So hot that that the superalloy turbine blades would melt if it weren’t for the protection of an oxide ceramic thermal barrier coating (TBC).
And, in addition to the thermal onslaught, the turbines experience centrifugal forces and intense mechanical loads with each flight—all in all, those TBCs and the turbines they protect take one heck of a beating.
Raghavan is studying how to improve those coatings, a goal that requires a better understanding of how they fail in the first place. So the international dream team devised a plan to see how the coatings respond, in real time, to the extreme temperatures and stresses they undergo with each flight—not an easy task.
But they dreamed big. To get the glimpse into precisely what happens in the coatings, the team devised a plan—utilizing the expertise of all team members—to use X-rays from Argonne’s synchrotron to study the thermal barrier coating on a nickel-based superalloy substrate under simulated service conditions inside a custom-built compact furnace.
“While the idea sounded impossible, we had a team of willing collaborators with complementary skills, as well as excellent students who were motivated to take on the challenge,” Raghavan says in a UCF press release.
Ragahavan and her students traveled to DLR to work with their German colleagues to build the furnace, which was then brought back across the Atlantic to use with X-ray beams at Argonne.
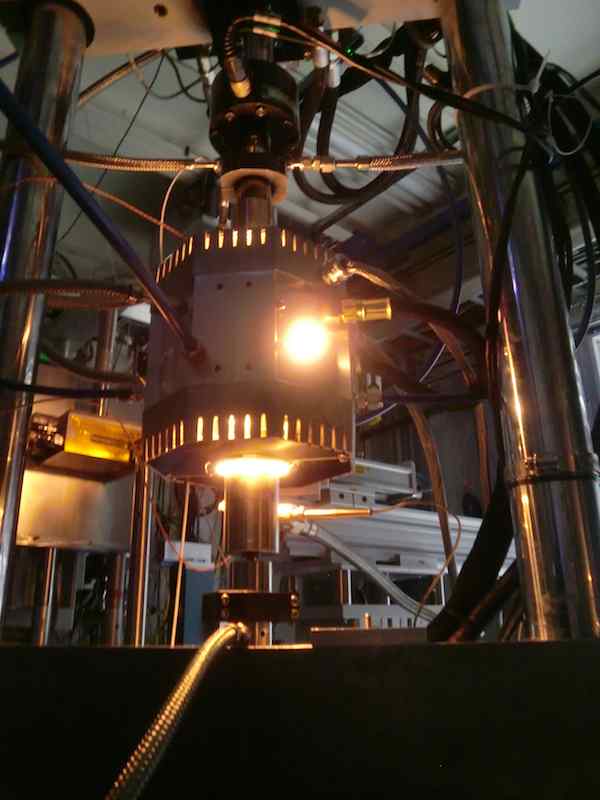
The testing setup at Argonne National Laboratory, at Jonathan Almer’s beam line 1-ID. Credit: DLR; UCF
And the outcome? The team has “succeeded in efforts to replicate complex operating conditions of turbine coatings under extreme temperatures of 1,000°C, while simultaneously capturing the in-cycle mechanics of material response,” Raghavan says in an email. “This paper presents the first quantitative high-resolution strains obtained from this study.”
Their unique approach allowed them to gather data on the diffraction peaks within their material, “overcoming challenges associated with the curvature and dynamic expansion conditions,” Raghavan says, so that they could determine the strains that develop in the material during service.
“Two factors set our work apart: the creation of a realistic extreme environment coupled with high-resolution data collection; and unique results that capture the evolving strains as they are subjected to varying levels of each or both,” she says.
Together, the team quantitatively measured strain at various depths in the coating, and that data validated current views of high-temperature relaxation. Their real-time measurements also validated previous microscopy studies of failure locations at the interface between the superalloy and TBC. “This capability allows for future experiments to provide an insight into the long-term effects of thermal gradient mechanical cycling of coatings applied to jet engine turbine blades,” Raghavan says.
“The techniques pave the way for a unique insight into understanding the mechanics leading to failure of the oxide layer in thermal barrier coating systems, with goals of improved durability and higher turbine inlet temperatures. The pioneering efforts present a game-changing approach to the study of materials under extreme environments—it takes high temperature materials testing to the next level.”
The paper is “Strain response of thermal barrier coatings captured under extreme engine environments through synchrotron X-ray diffraction” (DOI: 10.1038/ncomms5559).
Author
April Gocha
CTT Categories
- Aeronautics & Space
- Material Innovations
- Transportation