[Image above] A single octet truss unit cell developed by researchers at MIT and LLNL comprises materials with uncharacteristically high strength at low density. Credit: MIT
Almost a decade ago, a team of researchers led by Nicholas Fang unlocked a small—but important—part of science.
Their 2005 Science paper showed that the diffraction limit was actually not a limit at all—their work achieved subdiffraction limit imaging with the help of a special optical silver “superlens.”
Now at MIT, Fang’s team, collaborating with another team of scientists from Lawrence Livermore National Lab led by Christopher Spadaccini, most recently incorporated those subdiffraction limit principles to develop and fabricate new ultrastiff, ultralight, structures of metamaterials made by a high-precision additive manufacturing technique known as projection microstereolithography.
And just as wealth begets wealth, apparently one Science publication leads to another.
The former diffraction limit dictated that the ability to print small features was determined by the wavelength of light. But because the researchers banished the limit, they could achieve structures 1/100th the width of a human hair.
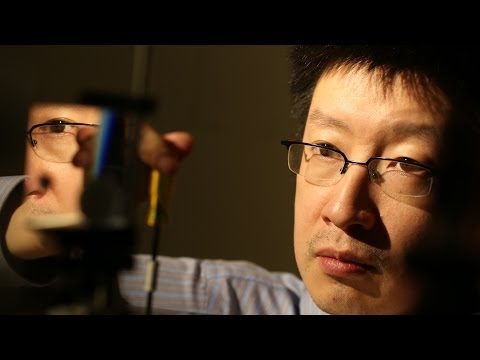
Nicholas Fang discusses how his team broke the diffraction limit to ultimately develop strong-but-light metamaterials. Credit: MIT Mechanical Engineering; Youtube
The interim time between the first limit-busting development and the latest publication was necessary to develop “something we can print, using a digital projection—to convert this solid model on paper to something we can hold in our hand,” Fang says in an MIT press release.
These new materials are unique in their ability to maintain stiffness and strength at low density. Fang explains in the release, “Normally, stiffness and strength declines with the density of any material; that’s why when bone density decreases, fractures become more likely. But using the right mathematically determined structures to distribute and direct the loads—the way the arrangement of vertical, horizontal, and diagonal beams do in a structure like the Eiffel Tower—the lighter structure can maintain its strength.”
The authors write in the paper that the new materials “maintain a nearly linear scaling between stiffness and density spanning three orders of magnitude in density, over a variety of constituent materials”—polymers, metals, and (our personal fave) ceramics.
Projection microstereolithography, which allows precision and complexity at smaller scales than other additive manufacturing techniques can provide, enabled researchers to generate microtruss-supported structures, while maintaining strength and reducing density.
Their structures feature octet-truss unit cells ranging (for all materials) from ~20 um to ~40 nm, with densities from 0.87 kg/m3 to 468 kg/m3 or relative densities from 0.025% to 20%, the authors report.
For the ceramic structures, the researchers fabricated the structures from photopolymer templates that were coated with aluminum oxide by atomic layer deposition. Thermal decomposition removed the polymer template, leaving hollow ceramic microlattices of alumina layers ~40 to 210 nm thick.
We’ve reported on similarly beautiful and complex microstructures on CTT before, but Fang and colleagues report that their new structures maintain strength over a wider density range than those previous developments.
“This material is among the lightest in the world,” Spadaccini says. “However, because of its microarchitected layout, it performs with four orders of magnitude higher stiffness than unstructured materials, like aerogels, at a comparable density.”
The paper is “Ultralight, ultrastiff mechanical metamaterials” (DOI: 10.1126/science.1252291).
Author
April Gocha
CTT Categories
- Manufacturing
- Material Innovations
- Nanomaterials