[Image above] Example of bullet-resistant glass after testing on the shooting range. Credit: timeless art, Shutterstock
Public appearances are a crucial activity for high-profile figures, yet they come with potentially big risks. Consider, for example, the attempted assassination of Pope John Paul II in 1981. While he survived the attack, it made the Vatican realize the need for stronger measures to protect the Pope during future events.
Fortunately, an existing technology offered an immediate solution to improve protection: ballistic windows. Popemobiles were soon fitted with either bullet-resistant acrylic or glass windows, following a trend adopted by other dignitaries earlier in the 20th century.
Besides transportation, bullet-resistant glass, known colloquially as “bulletproof” glass (even though all ballistic materials have a failure point), can be found installed wherever high levels of security are required, including military sites, government offices, law enforcement buildings, financial institutions, educational facilities, retail stores, and even some residential houses. Various materials and designs fall under this umbrella term, but all serve to help protect people now and in the future.
A long history of strengthened and toughened glasses
There are myths dating back centuries of artisans creating strong, supposedly unbreakable glasses. But one of the earliest concrete examples of a toughened glass are Prince Rupert’s drops, a form of thermally tempered glass attributed to Prince Rupert of the Rhine in 1661. These drops are created by placing molten glass into cool water, which rapidly cools the glass. The round ends of the drops can withstand being hit with a hammer, but the drops will explode if hit on the fragile tail.
About 200 years later, François Barthélémy Alfred Royer de la Bastie developed and patented a rudimentary method for thermally tempering glass. But it was nearly another 100 years after that, in 1935, when Rudolph A. Seiden secured the first comprehensive patent for a whole process to make thermally tempered glass.
Thermally tempered glass experiences compression forces on the outer surface and tensile stresses within the bulk. Instead of breaking into sharp, jagged pieces, the glass shatters into blunt, granular fragments, earning it the moniker “safety glass.”
Laminated glass came into being after a laboratory accident in the early 20th century. When French chemist Edouard Benedictus dropped a beaker coated in the thermoplastic cellulose nitrate from previous experiments, the cracked pieces held together rather than exploding apart. In 1909, the chemist filed one of the first safety glass patents, in which plastic cellulose was bonded between two sheets of glass.
Benedictus’s invention found major use in World War I military applications, such as airplane and automobile windshields and lenses for gas masks and aviator goggles. However, after the thermoplastic polyvinyl butyral (PVB) was formulated in 1927, this adhesive became the standard one used in laminated glasses, making an appearance in ballistic windows to protect bunkers and vehicles during World War II. Another thermoplastic material, polycarbonate, came on the scene around 1953, and it started being used as an additional layer in laminated glass—or as a wholesale replacement—due to its ballistic-resistant properties.
About three decades later, the first official “bulletproof” glass patent was awarded in 1982, titled Composite Pane Having a High Resistance to Impacts (US-4321777-A). This technology featured a thick layer of polycarbonate sandwiched between laminated glass panes, using layers of PVB or similar films as adhesives. This design allowed the kinetic energy of a bullet to be dispersed throughout the polycarbonate, with the laminated glass preventing sharp pieces of glass forming after impact.
Current materials and processes for bullet-resistant glass
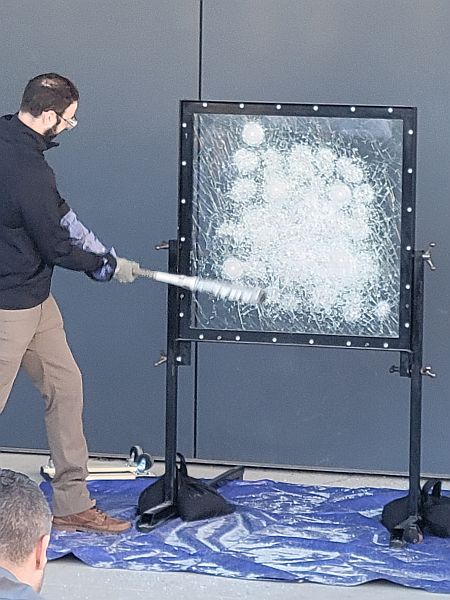
A demonstration of bullet-resistant glass at DesignColumbus 2025. Credit: Laurel Sheppard
Modern bullet-resistant glass typically consists of several layers of different materials. The outer layer, which the bullet strikes first, is a tempered glass pane laminated together with layers of PVB or ethylene-vinyl acetate. After the bullet strikes, the glass cracks but flattens the bullet by absorbing its initial impact.
The bullet then encounters the plastic layers, which may include acrylic and/or polycarbonate. These layers help disperse the energy of the projectile over a large area, so the bullet becomes embedded in the material instead of completely passing through.
Several steps are involved in the manufacturing process. A standard float glass process is used to make glass panels, which then undergo thermal or chemical tempering to strengthen the glass. After the various layers are cut to the desired size using laser and waterjet technologies, any contaminants are removed from the surface.
The layers are stacked together in a clean room environment often using advanced robotic systems, and then they are bonded together at high temperatures and pressures in an autoclave. An edge sealing and protective coating is added to the finished product to avoid moisture penetration. For more details on the materials and processes, watch the video below.

Credit: Complex Made Simple, YouTube
The finished product undergoes a variety of tests, including stress, optical clarity, and light transmission. For ballistic testing, the bullet-resistant glass is assessed according to the UL 752 standard, with levels of defense ranging from 1 (lowest) to 10 (highest). The level of defense is dependent on the composition of the layers, overall thickness, type of bullet, and number of shots. The video below shows the performance of three different types of Level 3 bullet-resistant glasses.
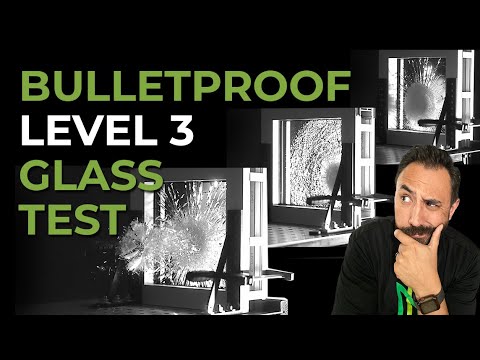
Credit: LearnGlazing, YouTube
Today’s bullet-resistant glass comes in various tints and transparency to match existing windows. It also can be frosted, thermally insulated, and manufactured to meet certain green building standards.
Innovative technologies improve performance
More recent advancements are making glass stronger, tougher, and more resistant to ballistics.
- Lightweight and transparent ceramics. Transparent aluminum oxynitride and magnesium aluminate spinel are providing a new generation of armor-like windows for both military and commercial applications.
- Nanotechnology improves strength without increasing weight. Researchers at Columbia Engineering and the National Institute of Standards and Technology produced films composed of silica nanoparticles coated with polymethacrylate strands, which can rapidly dissipate energy from impacts.
Smart glass features are also being integrated into bullet-resistant glass. Electrochromic and photochromic materials allow the glass to adapt to changing light conditions. In addition, companies are investigating integrating sensors for detecting impacts, temperature changes, and potential delamination in real time.
Ultimately, bullet-resistant glass is poised to remain a strong and growing market, helping save lives in these times of increasing conflicts and natural disasters.
Author
Laurel Sheppard
CTT Categories
- Education
- Glass
Related Posts
Fresnel lenses: A beacon of hope in the maritime industry
August 7, 2025