[Image above] A new butter-like ceramic interlayer makes solid-state battery cells much more stable and thus able to withstand much higher current density. Credit: Yen Strandqvist; Chalmers University of Technology
We have certainly sung the praises of solid-state batteries on Ceramic Tech Today and in the ACerS Bulletin. (Recently, the September 2019 issue focused on unlocking solid-state batteries’ potential.)
After all, these energy storage powerhouses offer the potential for higher performance, longer lifecycles, wide operating ranges, and improved safety compared to our current go-to of lithium-ion batteries.
Although we do not yet have solid-state batteries providing power in mainstream commercial energy applications, all signs seem to indicate that we will not be saying that much longer. Years of research investment and serious innovation seem poised to finally pay off.
As we detailed in an April post on Ceramic Tech Today, a handful of challenges remain to be solved before solid-state batteries finally achieve their full commercial potential. Specifically, we need to
1. Create stable interfaces with solid electrolytes,
2. Establish new tools to characterize solid-state batteries,
3. Develop scalable and cost-effective manufacturing, and
4. Design batteries for recyclability.
That first point is a significant challenge—the interface between the solid electrolyte and electrodes is a vulnerable point for solid-state batteries because it is chemically unstable.
So devising strategies to stabilize that interface is key to unlocking the potential of solid-state batteries. Not surprisingly, much recent research has investigated diverse materials for a stable interlayer, including glass. Yet existing interlayers still cannot sufficiently reduce resistance and cannot provide an adequate barrier between electrode and electrolyte to make solid-state batteries viable.
But a new high-performance ceramic interlayer that goes on as smooth as butter shows significant promise to finally be just the material that solid-state batteries have been searching for.
Developed by scientists at Chalmers University of Technology in Sweden and Xi’an Jiaotong University in China, the interlayer is a paste-like mixture of glass-ceramic nanoparticles [Li1.5Al0.5Ge1.5(PO4)3, otherwise known as LAGP] within an ionic liquid. Despite its butter-like consistency, the material provides a battery interlayer with adequately high ionic conductivity, high thermal stability, and low interfacial resistance to potentially make solid-state batteries a commercial reality.
“This is an important step on the road to being able to manufacture large-scale, cost-effective, safe and environmentally friendly batteries that deliver high capacity and can be charged and discharged at a high rate,” Aleksandar Matic, Chalmers professor of physics and senior author, says in a Chalmers press release.
In the lab, the team showed that adding the interlayer to solid-state coin cell test batteries composed of a ceramic LAGP electrolyte and lithium metal anode enhanced the batteries’ performance and durability by acting as a sufficient barrier between electrode and electrolyte.
When tested under heating, the interlayer protected batteries even after intense heating for 40 minutes—during which time, similar batteries sans the protective interlayer spectacularly caught fire and burned to a pile of ash.
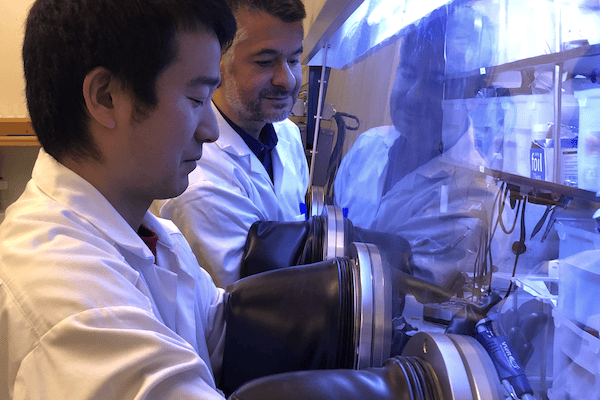
Researchers work in the battery lab at the Department of Physics at Chalmers to develop a multifunctional spreadable interlayer for the solid-state batteries of the future. Credit: Mia Halleröd Palmgren; Chalmers
In the open-access paper describing their work, the authors indicate that reaction between the interlayer ingredients contributes to the layer’s thermal stability, as the ionic liquid breaks down to deposit an “in‐situ coating of amorphous carbon on the LAGP nanoparticles.”
In addition to offering thermal stability, the scientists also show that the interlayer suppressed formation of dendrites, those spiky disruptions that grow between battery layers and can lead to catastrophic battery demise.
“This interlayer makes the battery cell significantly more stable, and therefore able to withstand much higher current density. What is also important is that it is very easy to apply the soft mass onto the lithium metal anode in the battery—like spreading butter on a sandwich,” Shizhao Xiong, Chalmers physics researcher and lead author of the new study, says in the press release.
That spreadability means it should be feasible to translate the interlayer material out of the lab and into manufacturing processes for commercial scale-up, according to Matic. “The interlayer with a butter-like (or paste-like) [consistency] should be quite suitable for large scale processing,” he writes in an email. Although large-scale processes for manufacturing solid-state batteries have not yet been developed, Matic says the interlayer’s spreadability means it can be easily incorporated with coating processes.
That is one of the challenges remaining to ensure commercial translation of the interlayer material, Matic adds. “Since there is no standard large-scale production for solid state batteries yet, the optimal properties from a processing perspective for the material in the interlayer cannot be defined,” he explains in the email. “Once one knows what properties are needed (e.g., the rheological properties) then we can fine-tune the composition.”
Matic says another challenge to address is exploring how thin they can make the interlayer—perhaps less than 10 micrometers—yet maintain good performance and reproducibility, which is an important consideration for commercialization. “This will be important for the final energy density of solid-state battery cells.”
The open-access paper, published in Advanced Functional Materials, is “Design of a multifunctional interlayer for NASCION‐based solid‐state Li metal batteries” (DOI: 10.1002/adfm.202001444).
Author
April Gocha
CTT Categories
- Energy
- Material Innovations
- Nanomaterials