[Image above] Micrograph of the fracture surface of a carbon nanotube–aluminum oxide composite with nanotubes bonded to ceramic grains. Credit: Bechteler et al., International Journal of Ceramic Engineering & Science (CC BY 4.0)
From a chemistry standpoint, adding carbon to oxide ceramics would seem to make little sense. Carbon mainly forms covalent bonds, and in graphite form, carbon will oxidize (burn) at temperatures over 400°C. Oxide ceramics, on the other hand, feature mostly ionic bonds, and they are processed (and often used) at temperatures well above 400°C.
However, researchers have found that carbon-containing oxide ceramic matrix composites can offer enhanced physical and chemical properties, driving much research in this area. Two particular forms of carbon are stimulating the most interest: graphene and carbon nanotubes (CNTs).
Graphene and carbon nanotubes both consist of a single to few sheets of networked carbon atoms. However, while graphene has a planar network structure, carbon nanotubes have a “rolled” tubular structure.
Recent articles on carbon nanotube-containing ceramic composites showed improved properties compared to the original ceramic composite, including solar energy harvesting, electrochemical response in sensors, green bonding and firing in castable refractories, and mechanical properties. The improvements to properties are so beneficial that production methods are being explored to scale up manufacturing with reproducible and cost-effective fabrication processes.
In the article “Improvement in mechanical properties of enamel via carbon nanotube addition,” researchers from Yantai University in China prepared and tested steel samples that were spray coated with enamel containing multiwall carbon nanotubes.
To create the enamel/nanotube slurry, the multiwall carbon nanotubes were first milled and then washed in concentrated acids to remove impurities and to increase surface roughness before being added to the enamel. The water-alcohol based slurry was then sprayed onto steel substrates and fired at 940°C.
Analysis of the coating revealed that the van der Waals forces of the carbon nanotubes led to good dispersion, while the surface roughness provided physical connection to the enamel matrix after firing.
Mechanical testing found that fracture toughness and bending strength improved with the addition of 0.4–0.5 weight% of carbon nanotubes. The authors attribute these improvements to crack deflection at the enamel–nanotube interface along with the higher strength of the carbon nanotubes preventing cracks from opening wider. Higher loading led to reductions in visual quality of the enamel and mechanical properties.
The paper, published in International Journal of Applied Ceramic Technology, is “Improvement in mechanical properties of enamel via carbon nanotube addition” (DOI: 10.1111/ijac.13659).
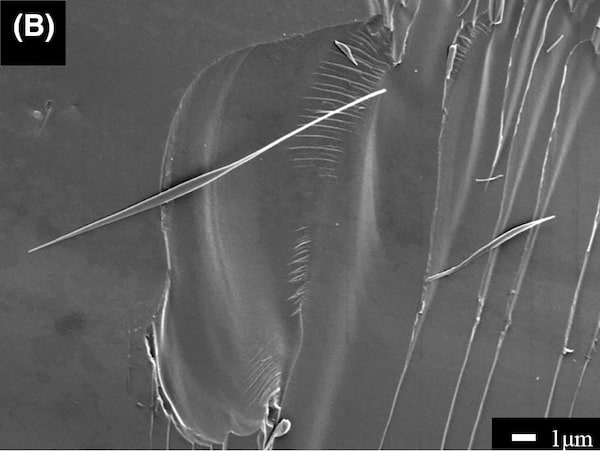
Note the preferred directions and fiber-pullouts on the fracture surface of the carbon nanotube-reinforced enamel. Credit: Wang et al., International Journal of Applied Ceramic Technology
In the open-access article “Development of pressureless sintered and hot-pressed CNT/alumina composites including mechanical characterization,” researchers from Nuremberg Tech (Germany) and Rauschert Heinersdorf-Pressig GmbH similarly found that 0.5 weight% additions of carbon nanotubes into alumina powder could be sintered to adequate density through pressureless sintering at 1,550°C. They also found improvements in hardness for hot-pressed samples peaked at approximately 0.5% carbon nanotube content. Different from the previous paper, these authors found toughness initially dropped but then increased with increased carbon nanotube content.
The authors made many additional observations surrounding the sintering of carbon nanotube–alumina and property measurements. First, they sought to employ safer and less expensive production methods. To that end, they did not acid-wash the as-received aqueous suspensions of carbon nanotubes, and they suspended the alumina powder in water with only a small amount (1%) of organic dispersant. Freeze-drying of the suspensions, which is common and cost-effective, removed the water without significant agglomeration.
The authors employed an in-situ dilatometer in conjunction with their hot-press to attain real-time densification information. Their results showed significant densification during the pressure ramp at 1,200°C. They then determined that the optimal mix of conditions for hot-pressing was a pressure of 80 MPa, sintering temperature of 1,550°C, and finer grained alumina starting material. Under these conditions, they sintered composites with up to 3% carbon nanotube content to more than 95% dense. Greater pressures did not substantially improve densification, and higher temperatures would lead to degradation of the nanotubes.
Their measurements of mechanical properties via indentation were performed on the top face of the disk (i.e., the plane perpendicular to the direction of applied pressure), as is typical in these studies. Innovatively, they also experimented on the “side” of the samples (the plane parallel to the direction of the applied pressure). Furthermore, they differentiated their results in different directions to explore anisotropy.
Toughness along the top was independent of direction, indicating no preferred orientation of the carbon nanotubes in-plane. For toughness measured on the side of the sample, the toughness measured for cracks travelling along the disk’s planes was much higher than toughness measured through the sample layers (parallel to the force direction).
Finally, the authors compared toughness calculated by three different models. While there were some broad qualitative agreements in the calculated values (e.g., compositions displaying greater or lesser toughness) and some correlation of amount of change for each model, there was no numerical agreement in reported values. Thus, the authors caution against comparing raw toughness values among different articles without making certain the calculations were performed using the same models.
The open-access paper, published in International Journal of Ceramic Engineering & Science, is “Development of pressureless sintered and hot-pressed CNT/alumina composites including mechanical characterization” (DOI: 10.1002/ces2.10103).
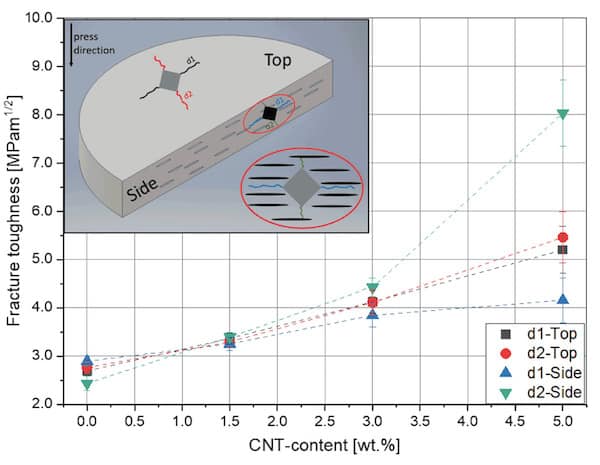
Fracture toughness of a carbon nanotube–alumina oxide composite separated in two crack orientations (d1/d2) of the measured indentations. Credit: Bechteler et al., International Journal of Ceramic Engineering & Science (CC BY 4.0)
These articles show that the future of innovative ceramics requires us to raise questions about assumptions while pushing forward with developing and refining fabrication methods and testing protocols.
Author
Jonathon Foreman
CTT Categories
- Material Innovations
- Nanomaterials