[Image above] Credit: Matthew Bodaly; Flickr CC BY-NC-ND 2.0
Fossil fuels still largely power our world—but their combustion creates a host of harmful waste gases.
While continuing increases in the use of renewable energy sources are helping decrease generation of these waste products, making fossil fuel utilization a cleaner process would also be a big win towards a multi-approach sustainable future.
And ceramics can do it.
Ceramic hydrogen separation membranes offer the possibility of not only helping to cut greenhouse gases from waste gas streams, but also to convert some of that waste into fuel through isolation of pure hydrogen gas—which can then be used as an energy source to power fuel cells, for example.
Plus, hydrogen separation membranes can offer benefits to other energy-intensive industries beyond fossil fuels, too—including the steel, glass, and cement industries.
But current hydrogen separation membranes fall short in several areas—the membranes operate at high temperatures (i.e., the process is energy-intensive); current membranes aren’t stable enough and don’t separate gases fast enough, because they suffer from low hydrogen flow rates; and the entire separation process is expensive.
So researchers at Forschungszentrum Jülich in Germany have developed a significantly improved stable ceramic hydrogen separation membrane that can enable a hydrogen flow rate that is nearly double that of other separation membranes.
To bypass the limitations of individual materials, the researchers explored two-phase membranes based on perovskite and fluorite. Their membrane mixes together barium cerate doped with europium oxide (BCEO) and cerium doped with yttrium and europium oxide (CYO).
“The individual grains are only a thousandth of a millimeter in size and exhibit both ionic and electronic conductivity,” lead author Mariya Ivanova says a Jülich press release.
The team’s two-phase BaCe0.8Eu0.2O3-δ:Ce0.8Y0.2O2-δ membrane, just 500 µm-thick, allows hydrogen protons and electrons to separately pass through the membrane. Protons occupy crystal lattice vacancies in the ceramic membrane and are driven through the membrane by pressure differences and temperature, the researchers explain.
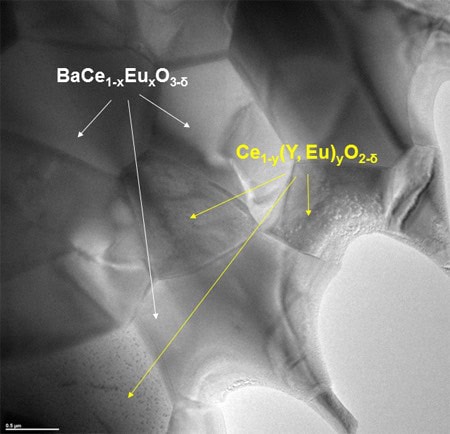
TEM image of the ceramic membrane. The two phases for proton and electron conduction are marked in colour: barium cerate doped with europium oxide (BCEO) and cerium doped with yttrium and europium oxide (CYO). Credit: Forschungszentrum Jülich
“They dock onto a hydrogen ion and jump in the direction of the lower pressure to the next hydrogen ion, from vacancy to vacancy, until they form elementary hydrogen again on the other side,” Ivanova says in the release. “The electrons are transported through the second component of the ceramic and ensure that charge equalization occurs.”
The ceramic membrane also functions at lower temperatures of 600–700°C, however, the research is preliminary. So far, the team has only fabricated and tested a small membrane, measuring about the size of a 10-cent coin—so there’s much more work to be done.
“It is still too early to be thinking about an industrial application,” Ivanova says. “We will continue to conduct research, searching for a suitable material with a high flow rate and stability as well as low costs. The next step will be to increase component size to make it fit for industrial application.”
Read more in the open-access paper, published in Scientific Reports: “Hydrogen separation through tailored dual phase membranes with nominal composition BaCe0.8Eu0.2O3-δ:Ce0.8Y0.2O2-δ at intermediate temperatures”(DOI: 10.1038/srep34773).
Author
April Gocha
CTT Categories
- Energy
- Environment
- Material Innovations