[Image above] Schematic of a proposed compact gas-to-gas heat exchanger with engineered ceramic cellular architectures between consecutive border plates. Credit: Pelanconi et al., Materials (CC BY 4.0)
When designing high-temperature systems, a lot of focus is given to developing materials that can withstand the extreme environment, such as ceramic matrix composites in jet engines. But it is equally important to design mechanisms and devices for managing the thermal energy.
Heat exchangers are devices used frequently for thermal management in anything from food processing to power generation to oil refining. These devices transfer thermal energy between two or more fluids—i.e., liquids, vapors, or gases—either directly (the fluids touch each other) or indirectly (the fluids are separated by a solid, thermally conductive boundary layer).
In recent years, researchers of indirect heat exchangers showed significant interest in using complex porous architectures as the boundary layer due to their tunable multifunctional properties. In particular, lattices consisting of a periodic arrangement of unit cells provide great control over the design and final function of the component.
Ceramic lattices—mainly alumina (Al2O3), zirconia (ZrO2), and silicon carbide (SiC)—are widely used in high-temperature applications as they withstand both high temperature and oxidation. And thanks to the advent of additive manufacturing technologies, designing unit cells from such materials is a more precise process than ever before.
In a recent open-access paper, researchers from the University of Applied Sciences and Arts of Southern Switzerland (SUPSI), EngiCer SA in Switzerland, and the University of Padova in Italy used additive manufacturing to develop ceramic lattices for high-temperature heat exchangers that could be coupled with the solar process of the HYDROSOL-beyond project.
The HYDROSOL-beyond project explores using concentrated solar power to produce hydrogen from the dissociation of water. The project is a continuation of HYDROSOL-Plant, which implemented and tested operation of a 750-kWth solar plant for hydrogen production.
The HYDROSOL-beyond project required development of two compact gas-to-gas heat exchangers, one involving the inert gas nitrogen and the other involving steam generation. To determine which material to use for the heat exchangers, the researchers compared several ceramics and stainless steels using the Ashby approach to material selection, which uses charts that plot material properties to compare the performance of materials in different conditions.
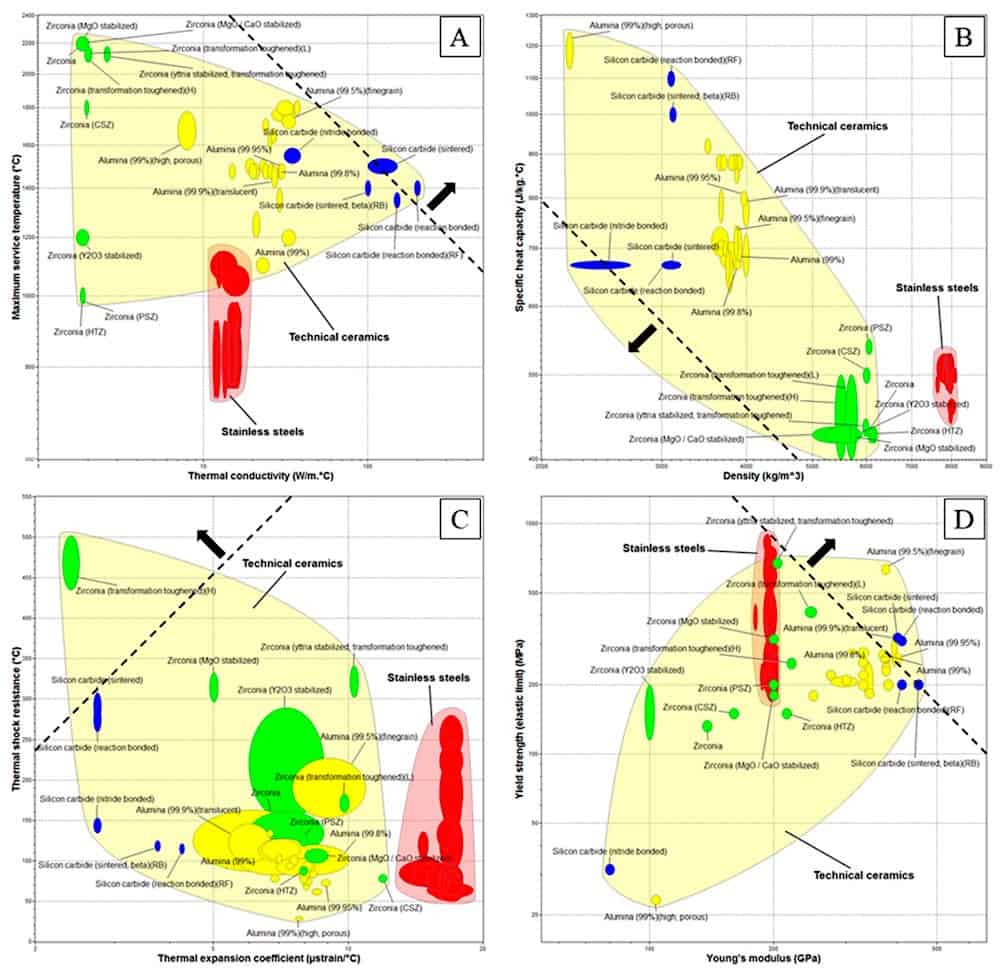
Ashby materials property chart for technical ceramics and stainless steels at 25°C: (A) thermal conductivity against maximum service temperature; (B) density against specific heat capacity; (C) thermal expansion coefficient against thermal shock resistance; (D) Young’s modulus against yield strength. Area legend: silicon carbide—blue; zirconia—green; alumina—yellow; stainless steel—red. Materials properties were obtained from Ansys GRANTA EduPack software, ANSYS, Inc., Cambridge, UK, 2021 (www.ansys.com/materials). Credit: Pelanconi et al., Materials (CC BY 4.0)
Based on the Ashby charts, the researchers chose the silicon carbide family of ceramics for both heat exchangers due to the ceramic’s very good thermal and mechanical properties with respect to zirconia and alumina in the expected operating environment. They specifically chose reaction bonded silicon carbide because it demonstrates higher thermal conductivity and thermal shock resistance and lower thermal expansion and heat capacity, and it is simpler to manufacture than pure-sintered silicon carbide.
To fabricate the ceramic lattice, the researchers first designed, dimensioned, and 3D-printed the structure using a polymeric material. These polymeric structures were then impregnated with a silicon carbide-based ceramic slurry before being dried, pyrolyzed, and infiltrated with liquid silicon to deliver the final reaction bonded silicon carbide lattice.
The lattice consisted of tetradecahedron unit cells, i.e., a polyhedron consisting of 14 faces (6 squares and 8 hexagons). These cells are known as Kelvin cells because the structure was first proposed by Scotch-Irish mathematical physicist and engineer William Thomson, Baron Kelvin of Largs.
The researchers created three lattice configurations using the Kelvin cells, distinguished by the number of cell layers arranged along the height of the channel (either one, two, or three layers). Then, using computational fluid dynamics simulations, they derived a collection of correlations that can be used to estimate the convective heat transfer coefficient and the pressure drops in the Kelvin cell-based lattices. For example, some of their observations include
- Heat transfer efficiency is lower for lattices with more layers as the average distances from the channel walls increases.
- Radiative heat transfer makes the lattice temperature distribution more uniform, which in turn increases the heat exchanged by convection with the fluid. This effect was most pronounced for the structure with three layers, as it is characterized by more pronounced temperature distribution inhomogeneity.
The researchers write that ideally this research will help “boost the performance of the current [heat exchange] technology through innovative solutions that will increase the potential of the [concentrated solar power] technology’s future commercialisation.”
The open-access paper, published in Materials, is “Application of ceramic lattice structures to design compact, high temperature heat exchangers: Material and architecture selection” (DOI: 10.3390/ma14123225).
Author
Lisa McDonald
CTT Categories
- Basic Science
- Energy
- Thermal management