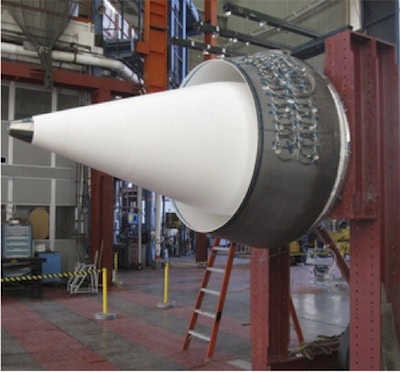
[Image above] Oxide CMC exhaust ground test demonstrator consists of a 1.60-m diameter nozzle and 1.14-m diameter × 2.34-m conical centerbody with titanium end cap inspection portal. Credit: Steyer; IJACT.
Ceramic matrix composite (CMC) materials can benefit aerospace in propulsion and exhaust, thermal protection, and hot primary structure applications, according to Todd E. Steyer of The Boeing Company (Huntington Beach, Calif.).
Reviewing aerospace-related presentations from last July’s 4th International Congress on Ceramics in a recent paper in the ACerS International Journal of Applied Ceramic Technology, Steyer outlined several emerging aerospace opportunities for CMCs, including propulsion and exhaust, thermal protection, and hot primary structure applications.
In the propulsion area, gas turbines have long been dominated by the use of nickel-based superalloys and titanium alloys. According to Steyer, engine manufacturers are now taking a closer look at CMCs for use in engine hot sections. Silicon carbide-based composites can handle temperatures to 1200°C while reducing weight and cooling requirements, resulting in reduced fuel burn and improved performance.
According to an article in MIT Technology Review, new engines being developed by CFM, a partnership between GE and France’s Snecma, feature CMC components that will reduce fuel consumption by about 15 percent—enough to save nearly $1 million per year per airplane, assuming a fuel cost of $2.50 per gallon.
CFM’s LEAP engine uses SiC-reinforced CMC parts that don’t require cooling, enabling air that would normally be diverted to keep superalloy components from melting to be used to generate thrust. It also uses parts produced using a 3-D printing process, according to the MIT article.
The company already has orders for 4,500 of the new engines. In addition to saving money, the engines will help users comply with current and anticipated emissions regulations.
In engine exhaust systems, work is underway to produce an alumina-fiber reinforced aluminosilicate matrix composite centerbody and exhaust nozzle for commercial aircraft. Currently in ground testing, the ceramic nozzle will reduce weight and engine noise and increase component lifetime, Steyer wrote.
Ceramic materials have long been used in aerospace thermal protection applications—for 30 years, ceramic tiles with glass-based coatings provided thermal protection for the US’s now-retired space shuttle fleet. Initially composed of silica fibers with a nominal density of 0.14 g/cm3 and a glaze aimed at controlling emissivity and limiting catalysis for oxygen and nitrogen recombination from the plasma on reentry, the tiles provided effective insulation but required heavy maintenance between flights. Engineers improved durability over the shuttle’s service life using new tile substrates and coatings.
For new thermal protection applications, Steyer reported on CMCs developed and tested by NASA researchers for use at temperatures to 1700°C. Toughened Uni-piece Fibrous Reinforced Oxidation-Resistant Composite (TUFROC) materials build on the success of insulating fibrous tiles with high-emissivity/low-recombination-efficiency coatings using a refractory ceramic carbon-insulated layer for dimensional stability.
Supersonic and hypersonic flight vehicles present unique challenges for primary hot structural materials, and ultrahigh-temperature ceramics (UHTCs) have been emerging as a promising class of materials for leading edges for hypersonic vehicles. The refractory nature of this class of carbides, borides, and nitrides makes them good candidates for the highest heat flux areas as well as areas with high integrated heat load as a function of time, Steyer wrote.
Particulate, whisker, and chopped or continuous fiber reinforcements are resulting in improved mechanical properties, but the materials’ relatively high density and difficulty in large-scale processing are potential drawbacks. Steyer reported one recent example in which CMCs consisting of 0.5- to 1-mm long chopped Hi-Nicalon SiC fibers in a ZrB2 matrix hot-pressed at 1700°C showed significantly improved chevron-beam fracture toughness at compositions containing up to 20 vol.% fiber.
Increased use of CMCs in aerospace will require microstructure optimization, a path to entry into service, and improved affordability. Steyer believes fundamental and applied research in damage accumulation mechanisms/models, life prediction methodologies and modeling, nondestructive inspection techniques, and robust field and depot-level repair methods will result in more CMCs in aerospace applications.
Author
Jim Destfani
CTT Categories
- Aeronautics & Space
- Material Innovations
- Refractories
- Thermal management