[Image Above] Credit: Air Force Research Laboratory
We’ve seen trends in faster flight heat up over the past few years—including both efforts to travel at supersonic (Mach 1–Mach 5) and hypersonic (>Mach 5) speeds.
For instance, NASA has been public about its plans to develop a series of X-planes that use a host of new technologies to develop and test entirely new aircraft designs.
Just recently, NASA announced that it will start building one of its concept X-planes that can travel at supersonic speed sans the supersonic boom. Engineered to redirect supersonic shockwaves coming off the plane, the aircraft design prevents the loud boom noise that has historically accompanied—and prevented—supersonic travel.
Plus there are plenty of indications that even faster hypersonic planes are now in development, or perhaps even already built. Other countries are speeding towards hypersonic travel, too—China reportedly is making significant progress towards realizing its goals to lead the world in hypersonic technologies.
The ability to travel faster is good news for reducing travel time. But aircraft that travel at such fast speeds pose an engineering challenge because of the high temperatures their materials must withstand.
Additively manufactured ceramic matrix composites are enabling new possibilities for commercial jet engines today by enabling higher operating temperatures, but when it comes to supersonic and hypersonic speeds, even ceramic matrix composites can’t take the heat.
Even more extreme materials like ultra-high temperature ceramics, such as zirconium carbide, are necessary to perform at the high temperatures generated by aircraft traveling at supersonic and hypersonic speeds.
Recently, improved characterization and analysis techniques have afforded new insights into these incredible ultra-high temperature materials, providing scientists and engineers with the data and knowledge to make further improvements.
And now, a recent collaboration seems to be poised to turn up the heat even further for ceramic materials for hypersonic travel and beyond.
The Air Force Research Laboratory’s Aerospace Systems Directorate recently announced that it is working together with HRL Laboratories (Malibu, Calif.) to additively manufacture high-temperature ceramic materials that are well-suited for hypersonic aircraft.
The two entities recently made their pairing official, together signing a technology transfer agreement (called a CRADA-MTA) that allows ARFL and HRL to share materials for testing.
Those additively manufactured silicon oxycarbide materials are being produced by HRL Labs using a printing process the company has developed to manufacture ceramics from pre-ceramic resins. Heat-treating components printed from the resins at ~3,200ºF forms silicon oxycarbide ceramics, which are tough and refractory enough to survive extreme environments—such as those encountered at hypersonic speeds.
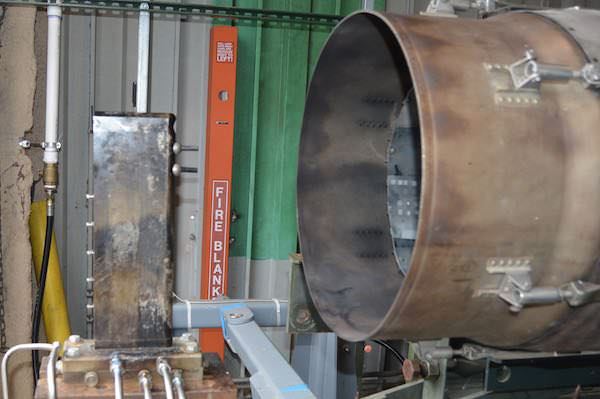
A sample of additively manufactured silicon oxycarbide being tested at Arnold Air Force Base. Credit: Air Force Research Laboratory
Despite challenges in developing such techniques, additive manufacturing and ceramics are a good match for one another—the additive manufacturing technique offers design flexibility and the capability to fabricate shapes and structures that are difficult to achieve with other ceramic manufacturing techniques. And ceramic materials offer additive manufacturing important materials capabilities, such as high resistance to heat and corrosion.
According to an Air Force press release, AFRL has tested the HRL Labs-printed SiOC components, analyzing various properties of the materials with techniques such as thermal expansion and high-enthalpy tests.
AFRL reportedly prepared a final report of its results and provided HRL with its analysis. However, that report is not public, according to Tobias Schaedler, a senior scientist at HRL Labs.
So all we do know about how the SiOC performed in AFRL’s battery of tests is limited to the press release: “During the course of their collaborative study, AFRL and HRL pushed the additively manufactured components far beyond their design envelope. The data which emerged from this extreme testing provided the partners with valuable information that is currently being utilized to guide the production of next-generation additively manufactured ceramics. These recommendations and further advances by HRL have the potential to produce materials that can meet the hypersonic requirements.”
Read: they’re further tweaking the materials, but the results so far are promising.
“The extreme temperature testing that AFRL performed revealed the limits of our new material and challenged us to improve it,” Schaedler says in the release.
Fingers crossed that we’ll be hearing more about this hot material in the near future.
Want to read more articles like this? Subscribe to the Ceramic Tech Today newsletter to continue to receive the latest news in the ceramic and glass industry right in your inbox! Visit this link to get started.
Author
April Gocha
CTT Categories
- Aeronautics & Space
- Manufacturing
- Material Innovations
- Thermal management
- Transportation