[Image above] Artist’s rendering of the USS Zumwalt in action. First in a new class of Navy destroyers, the Zumwalt will use transparent MgAl2O4 deckhouse windows. Credit: US Navy.
Two manufacturers are in a bit of an “arms race” to commercialize aluminum oxynitride and magnesium aluminate transparent polycrystalline cubic spinel for defense and other applications.
We did a full-scale report on the state of the technology in this article (pdf) in the March 2013 ACerS Bulletin. Since then, both Surmet Corp., (Burlington, Mass.), the supplier of that original report, and ArmorLine (Indian Land, S.C.) have been hard at work to make larger pieces at higher volumes, higher quality and, especially, lower cost.
On May 28, Surmet announced delivery of 18×35 inch monolithic aluminum oxynitride windows (the company’s ALON product line), which it says are the world’s largest transparent ceramic armor windows. “Producing the windows in this size and transitioning them into the defense system represents both technical and programmatic success for Surmet and its DoD funding partners,” the company said in a news release. The program’s ultimate goal is production of 36×36 inch ALON windows by mid-2014, according to the release.
ArmorLine works only with magnesium aluminate material for optical and armor applications. Plant engineering manager John Voyles said in a June 13 webcast that the company opted for an “all-in” approach to scale-up and commercialization of optical grade transparent MgAl2O4 spinel, using a $20 million private investment from parent company Defense Venture Group Ltd. (Indian Land) to purchase and install the equipment needed for development of robust production processes. The ultimate goal is volume production of optical quality components as large as 50×30 inches.
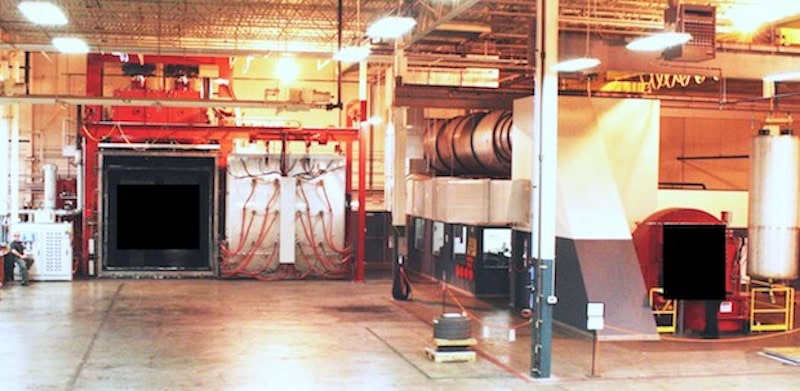
Hot pressing and HIP equipment at ArmorLine’s Indian Land, S.C., facility is said to be the largest in the world. For scale, note the operator seated at far left. Also note the company has blacked out a couple of strategic features in this photo. Credit: ArmorLine.
The company now operates out of a 257,000 ft2 facility that houses what it says are the world’s two largest vacuum hot presses and the world’s largest hot isostatic press. Voyles said the company began its scale-up efforts in April 2012, producing 16×16 inch plates used by the Army as ballistic test coupons. By January of this year ArmorLine was hot pressing multiple 19×19 inch plates per die—a total of more than 250 plates that required 20 HIP runs—and had produced other components as well. One was a 36-inch diameter disk Voyles said was the largest-diameter optical quality spinel piece ever attempted.
For components intended for optical applications in the visible to mid-infrared range, ArmorLine has worked to achieve and maintain refractive index homogeneity both within lots and from lot to lot. Voyles said testing of optical properties of more than 50 pieces has shown consistent refractive index on round test parts from 4 to 13 inches in diameter and plates up to 16×23 inches. Thicknesses generally range from 0.3 to 0.8 inches, although the company has produced parts as thick as 1.5 inches, he added.
ArmorLine’s focus hasn’t been entirely on process validation and testing, though. According to Voyles, the company has produced curved plates for a specific land vehicle application and is close to manufacturing optical quality 19×29 inch plates. “The goal is to have that size by fall,” he said.
Those plates would be destined for use as electro-optical/infrared deckhouse windows in the USS Elmo Zumwalt, the first of a new class of US Navy destroyers that feature a low radar signature compared with current vessels. Currently under construction at Bath Iron Works (Bath, Me.), the ship is expected to be delivered in 2014. A brief time-lapse video of the deckhouse being integrated with the ship’s hull is available here.
Author
Jim Destfani
CTT Categories
- Optics