[Image above] Credit: David Wilson; Flickr CC BY-NC-ND 2.0
We’re well into throes of warm spring-like temps and fast approaching the balmy days of summer here in the Midwest, so the need for ice removal seems like a distant memory—a concern to pack away for next winter, along with our down parkas, wool sweaters, and thick-soled boots.
Lucky for our future selves next winter, scientists don’t conduct research depending on the season. The work to develop new and innovative solutions for surface ice removal continues despite the rising mercury.
This spring, we covered research from the University of Michigan (Ann Arbor, Mich.), where researchers are working on a new durable and inexpensive spray-on ice-repellent coating that is thin, clear, and slightly rubbery to the touch and could make ice slide off equipment, airplanes, and car windshields with only the force of gravity or a gentle breeze.
Meanwhile, researchers at the University of Nebraska-Lincoln are keeping their focus more down-to-earth and hitting the pavement to develop an electrically conductive concrete that uses gentle heat to shed ice, while still being safe to the touch.
And earlier this year, we reported on work from from Rice University chemists who are using graphene to help heat surfaces and simplify ice removal. The team developed a thin coating of graphene nanoribbons in epoxy that is effective at melting ice on a helicopter blade—and that means it may be an effective real-time de-icer for aircraft, wind turbines, transmission lines, and other surfaces exposed to winter weather.
This week, the Rice University team published the latest advancement on their graphene-based de-icer.
The new material still melts ice from airplane wings and electrical wires when conditions get too cold. But now the team says if the air is above 7ºF, their de-icer prevents any ice formation at all.
James Tour, chemist at Rice, and his team gave the de-icer superhydrophobic capabilities that passively prevent water from freezing above 7ºF, explains a university news release. When the de-icer is sprayed on a surface—such as an airplane wing—it forms a tough film of atom-thin graphene nanoribbons that conduct heat when an electric current is applied, melting ice and snow accumulations.
“We’ve learned to make an ice-resistant material for milder conditions in which heating isn’t even necessary, but having the option is useful,” Tour says in the release. “What we now have is a very thin, robust coating that can keep large areas free of ice and snow in a wide range of conditions.”
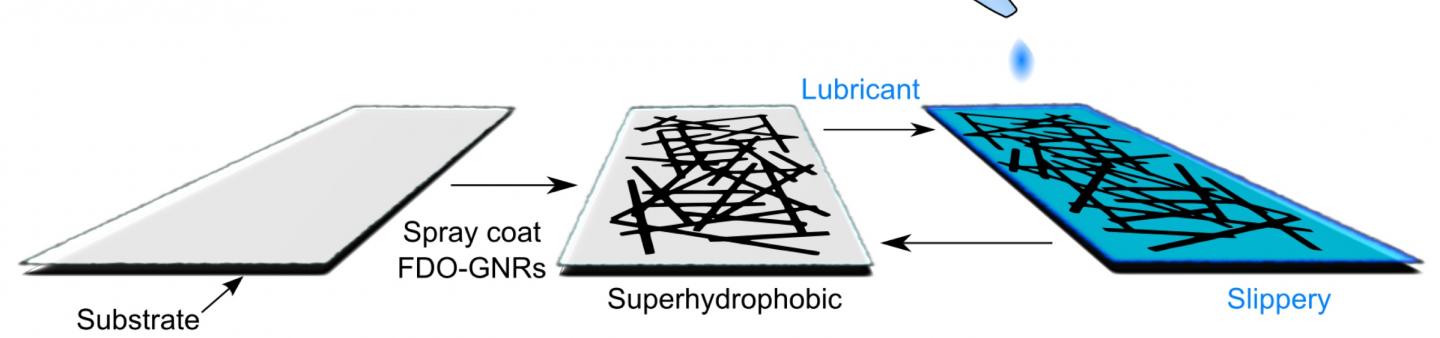
Rice University scientists have modified their graphene-based de-icer to resist the formation of ice well below the freezing point and added superhydrophobic capabilities. The robust film is intended for use in extreme environments as well as on aircraft, power lines, and ships. Credit: Tour Group; Rice University
But for a material to be superhydrophobic, it has to have a water-contact angle that exceeds 150º.
So the team modified the graphene nanoribbons with a fluorine compound to enhance hydrophobicity. According to Tour, nanoribbons modified with longer perfluorinated chains produced films with a higher contact angle—a finding that suggests the graphene film can be tuned to suit different weather conditions.
When the team warmed test surfaces to room temperature and cooled them down again, Tour says the change in temperature didn’t alter the film’s properties. But the team discovered that when the ambient temperature dipped below 7ºF, water would condense within the film’s pores and rob the surface of its superhydrophobic and ice-phobic properties.
Then the team applied at least 12 volts of electricity to the film, which warmed it enough to retain its repellant properties. Applying 40 volts to the film, they found, brought it back to room temperature, even if the ambient temperature was –25ºF. Any ice that formed melted after 90 seconds of resistive heating, the release explains.
Although the de-icing capability worked efficiently to remove ice and snow, the team still faced a challenge—they found that it didn’t rid the film completely of water. Some still became trapped in the pores between linked nanoribbon bundles.
So they employed a slippery solution, according the release. They added a lubricant with a low melting point (–61ºF) to the film, which sped up de-icing and saved energy in the process.
The research, published in ACS Applied Materials and Interfaces, is “Passive anti-icing and active deicing films” (DOI: 10.1021/acsami.6b03060).
Author
Stephanie Liverani
CTT Categories
- Material Innovations
- Nanomaterials