[Image above] Piezoceramic patch-based smart aggregates (SA) are used for structural health monitoring of concrete structures. Could a tubular SA design monitor these structures even better? Credit: synx508; Flickr CC BY-NC 2.0
When I was a kid growing up in Iowa, my parents took me to all the typical tourist attractions that make Iowans proud—the Iowa State Fair, National Balloon Classic, riverboat ride down the Mississippi. But they also made sure I saw some of the more hidden gems of Iowa tourism, such as the covered bridges of Madison County.
The six bridges included on the covered bridges tour are beautiful because they lack something many bridges today rely on—concrete. The Madison County bridges are instead made mostly from wood, which gives them a unique charm.
But though wood bridges have charm, I understand why concrete is often used instead—concrete has higher compressive strength and is resistant to wind, water, and fire, making concrete bridges generally safer (and upkeep cheaper) than wood bridges in the long run.
In addition to its inherent materials properties, another reason concrete is such a safe building material is that we have developed effective ways to monitor its health. In particular, piezoelectric-based transducers are commonly used to monitor structural health of concrete structures because they can serve as both a sensor (receive signals) and an actuator (transmit signals).
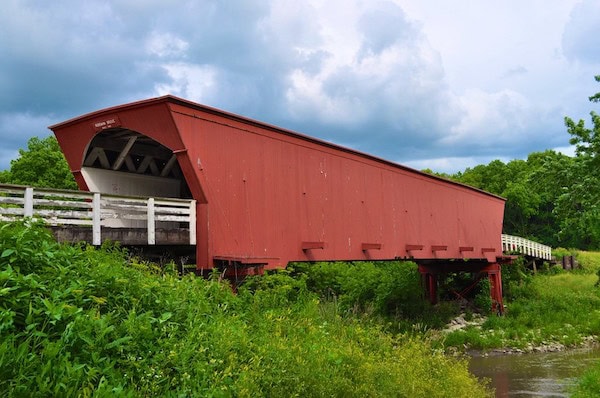
Though wood bridges have their charm, concrete bridges are generally more resistant to the environment and require less upkeep. Credit: Scott McLeod (of Roseman Bridge in Madison County; Flickr CC BY 2.0
However, piezoelectric patches are quite vulnerable to external loads (a hard impact may destroy them), and they can short out if water seeps into the concrete.
That is why Song et al. proposed smart aggregates (SAs) in 2007. In SAs, the piezoelectric patch is protected by both an inner metal shell and an external layer of a high-strength protective material (such as marble or cement). Over the past decade, numerous experiments have shown the efficacy of this design—despite the extra protective casing, SAs retain their conventional piezoelectric abilities.
Yet SAs have a noticeable limitation. Due to the plate-like geometry of piezoelectric patches, the detection range of conventional SAs are limited to patch orientation—they are unidimensional. That means a large number of SAs are needed to monitor a concrete structure, because each SA can only measure stress from one direction.
Kong et al. proposed a spherical SA that could offer omnidirectional measurements in a 2017 two–part paper. However, according to Weihang Gao and Hongnan Li (SLCOE, Dalian University of Technology) and Siu Chun Michael Ho (University of Houston), this design may not be practical for many concrete structures.
“[M]any concrete structures can be considered as two-dimensional structures (e.g., precast shear wall, concrete pavements and floors),” they explain in a recent paper. “If the SSA [spherical SA] is employed to generate and measure stress waves in two-dimensional (2D) structures, reflected waves from the two surfaces along the direction of the thickness will complicate the detection result.”
In their paper, published in Sensors, they propose a new SA design to measure stress in 2D concrete structures—a tubular SA (TSA).
“The actuating and sensing core in the TSA is a piezoceramic tube, which can generate a radially expanding stress wave along the plane of slab-like concrete structures while minimizing reflections at the two surfaces,” the researchers explain in the paper.
They fabricated the TSA by coating a piezoceramic tube with a thin layer of epoxy resin to enhance the tube’s strength and provide waterproofing protection. They then coated the entire assembly with liquid electrical tape to provide electrical insulation and further waterproofing. Lastly, the transducer was encased within ultra-high-performance concrete (UHPC).
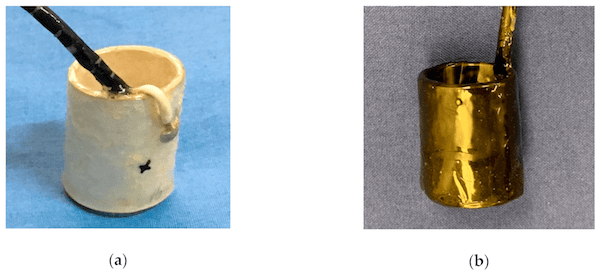
The researchers coated their piezoelectric tube with (a) epoxy resin and (b) liquid electrical tape to provide electrical insulation and waterproofing protection. Credit: Gao, Li, and Ho, Sensors (CC BY 4.0)
The researchers embedded the completed TSA into the center of a hexahedral concrete block and bonded four conventional (unidimensional) SAs onto the surface. They then conducted three experiments to test the TSA.
First, the researchers used an impedance analyzer to measure natural frequencies of the TSA, to determine suitable operating frequencies (they found the TSA operated well in 35–45 kHz and 60–85 kHz frequency ranges). Then, they tested sending and receiving stress waves to show advantages of TSAs over conventional SAs.
“When the TSA serves as the actuator [signal transmitter], a radially uniform stress wave in the 2D plane of the structure can be generated,” the researchers explain. “Likewise, the proposed TSA can easily recognize the first arrival of the stress wave when serving as a sensor.”
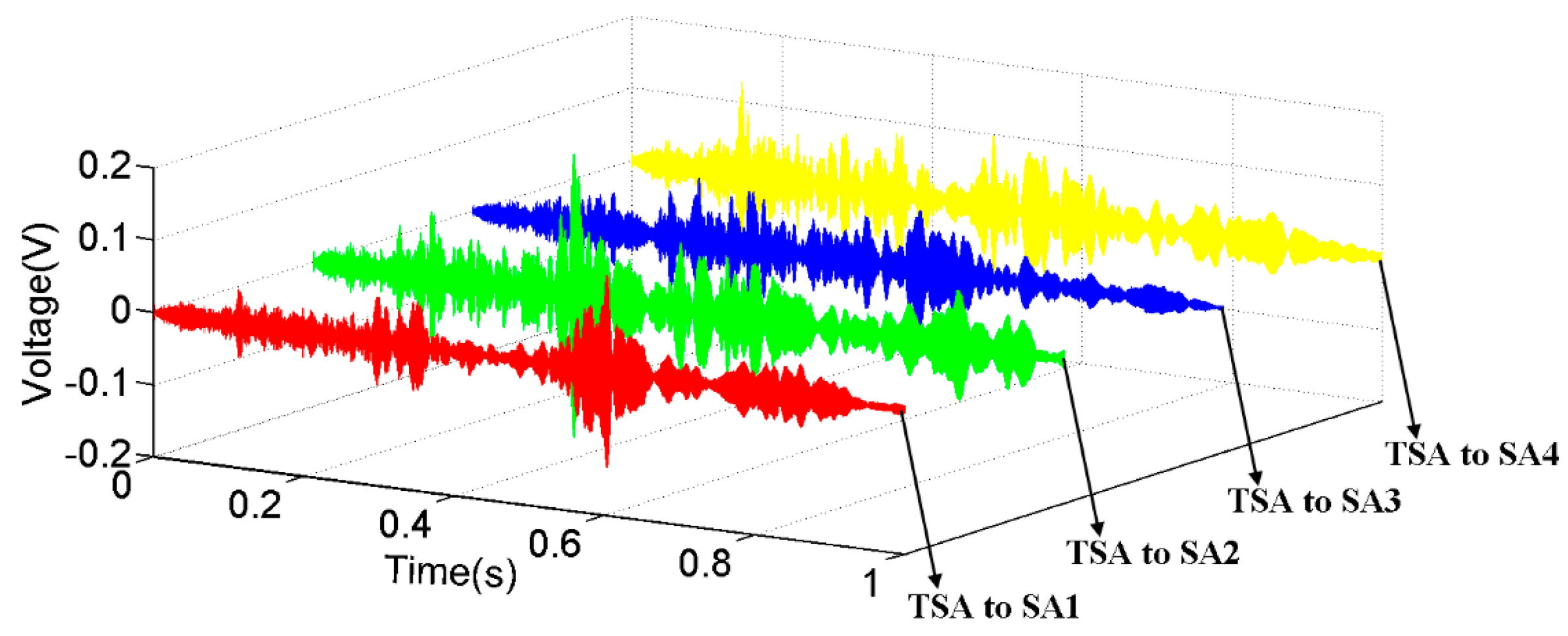
Signals received by the surface-bonded SAs confirmed that the stress wave induced by the TSA was radially uniform in the plane of actuation. Credit: Gao, Li, and Ho, Sensors (CC BY 4.0)
In the last experiment, the researchers transmitted and received swept sine stress waves to test if TSAs can implement active sensing, which their experiment confirmed.
From these experiments, the researchers highlighted two important conclusions about the TSA transducer design.
- TSAs have a larger monitoring area than patch-based SAs, meaning fewer are needed to perform the same function.
- Unlike spherical SAs, TSAs can minimize the influence of reflected stress waves.
Ultimately, “the experimental results indicate the feasibility of the proposed TSA in the damage detection of two-dimensional concrete structures,” the authors conclude.
After reading this article, I was curious if any similar devices exist that could monitor structural health of wood structures. And what do you know—wood itself has piezoelectric properties! Who knows, maybe in the future, the Madison county bridges will be monitoring themselves.
The open-access paper, published in Sensors, is “A novel embeddable tubular piezoceramics-based smart aggregate for damage detection in two-dimensional concrete structures” (DOI: 10.3390/s19071501).
Author
Lisa McDonald
CTT Categories
- Cement
- Construction
- Material Innovations