[Image above] United States’ infrastructure is in dire need of repair. Hydrodemolition is an ideal method for concrete reconstruction. Credit: NCDOTcommunications, Flickr (CC BY 2.0)
No matter where I go in the United States, I hear the same refrain: “Our town/county/state has the worst potholes.”
Though many of these statements are steeped in anecdotal hyperbole, the truth is that U.S. infrastructure is crumbling across the nation—and crumbling severely.
The American Society of Civil Engineers’ 2017 Report Card for America’s Infrastructure gave U.S. infrastructure a D+, the same score it received in 2013. An analysis from the American Road & Transportation Builders Association states there are over 47,000 structurally deficient bridges across the nation, including 1 in 3 bridges on the Interstate Highway System.
If Infrastructure Week ever becomes a reality instead of a long-running joke, we will need efficient and safe methods to repair this failing infrastructure. When it comes to repairing concrete, one technique in particular stands out as ideal—hydrodemolition.
Hydrodemolition is a concrete removal technique that uses high-pressure water jets to remove layers of deteriorated and damaged concrete. It was first developed in the early 1980s by a joint venture led by the Swedish National Road Administration looking to develop safer and more efficient alternatives to conventional concrete removal methods.
Compared to conventional methods, hydrodemolition has several advantages. For example, unlike jackhammers, which forcefully batter through concrete and create microfractures that can significantly damage structure integrity, the high-pressure water used in hydrodemolition widens existing pores and microcracks, breaking the concrete apart in a controlled manner.
Hydrodemolition also leaves behind a rough surface that is ideal for bonding with new concrete, it presents minimal risk for damaging the steel rebar, and it reduces dust pollution while aiding collection of the concrete that is removed.
All these immediate advantages of hydrodemolition lead to greater advantages in the long term. “The Swedish Cement and Concrete Research Institute reports a bridge repair life expectancy of 21 years to 35 years with hydrodemolition compared to 7 years to 12 years with mechanical chiseling,” according to a Concrete Construction article.
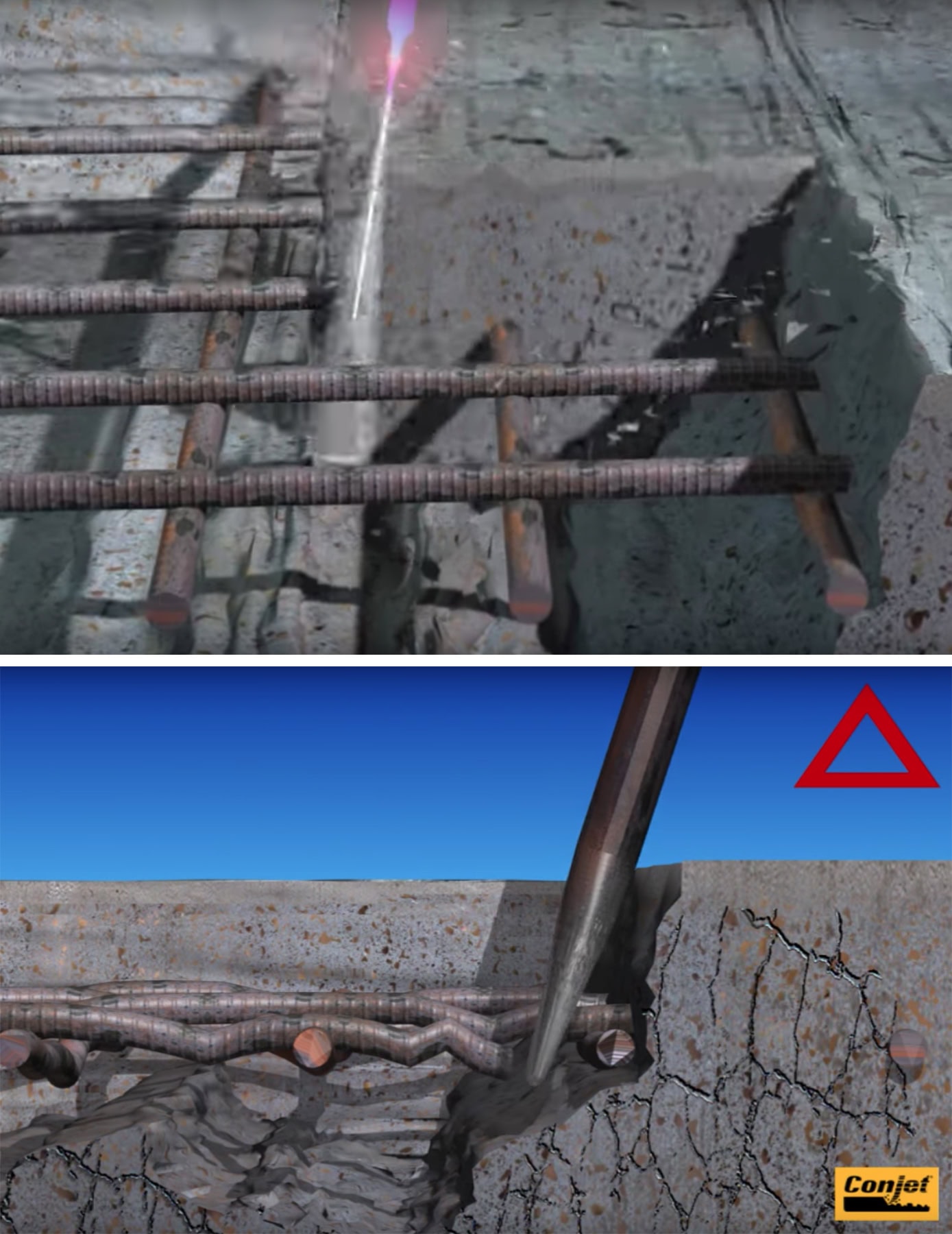
Hydrodemolition equipment manufacturer Conjet AB illustrates the difference between hydrodemolition (top) and conventional methods (bottom) of concrete removal. In contrast to jackhammers, hydrodemolition does not create microfractures and does not damage the steel rebar. Credit: Conjet AB, YouTube
In 2008, when the European EN 1504 standards for protecting and repairing concrete were released, hydrodemolition manufacturers celebrated. “The new EU safety and environment regulations … is literally promoting hydrodemolition robots to comply with the new environmental and safety standards,” Roger Simonsson, chief executive of Swedish hydrodemolition equipment manufacturer Aquajet, says in a Professional Demolition International article.
In the past few months, hydrodemolition has shown up repeatedly in news articles across the U.S. For example, officials in Jackson County, Alabama, plan to use hydrodemolition to repair their longest and tallest bridge; the Rhode Island Turnpike and Bridge Authority administration include hydrodemolition in their multiphase project to repair the 50-year-old Newport Bridge; and Utah Department of Transportation (UDOT) officials are using hydrodemolition to quickly repair concrete on 14 different bridges.
The hydrodemolition project in Utah particularly highlights the advantages to hydrodemolition. A For Construction Pros article explains that when UDOT officials conducted a study to determine best repair method, “The study found that using [hydrodemolition] would cost an estimated $14.4 million compared to $29.7 million to reconstruct the bridge decks and $300 million to replace the bridges entirely.”
Want to see a hydrodemolition system in action? Check out this video demonstrating the technique!
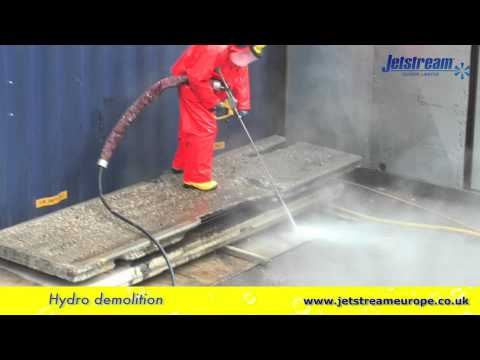
Credit: Jetstreameurope, YouTube
Environmental issues
Hydrodemolition can use a lot of water. For example, though handheld guns may use as little as 6 gallons per minute (gpm), larger machines can use up to 100 gpm. This water requirement could increase costs if water needs to be trucked in to a remote location.
However, with proper measures, substantial amounts of water can be reclaimed and reused. For example, though the UDOT project uses up to 40,000 gallons of water per day, they recover and reuse about 95% of that water onsite. The remainder is sent to settling ponds for further processing. They also haul the concrete debris to concrete plants for recycling.
Considering hydrodemolition systems for your construction business?
Hydrodemolition systems can range in price from $2,000 “shotgun” systems to $300,000 fully robotic devices. Consider the requirements of your project when selecting a system.
Author
Lisa McDonald
CTT Categories
- Cement
- Construction