[Image above]: Sampling of commercially available LED lightbulb replacements for standard incandescent bulbs. Credit: Geoffrey A. Landis; Wikimedia.
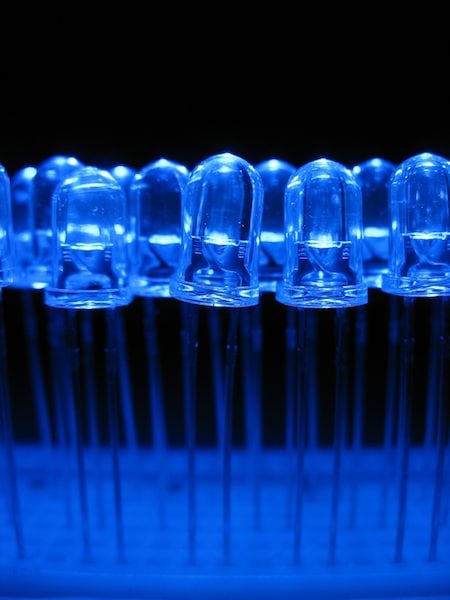
Yellow-emitting phosphors convert some blue LED light and combine with the remaining blue light to make desirable and useful “white light” LED lightbulbs. Credit: Gussisaurio, Wikimedia.
When then-president George W. Bush signed into law the Energy Independence and Security Act of 2007, the death knell began tolling for incandescent lighting. While the legislation did not require an end to incandescent lighting, it made this lighting source incapable of meeting the higher efficiency required by the law. The compact fluorescent light bulb is one replacement technology that gained early traction, but light sources based on light-emitting diodes—LEDs—are gaining ground quickly.
Analysts and market-watchers expect LED technology to emerge as the dominant lighting technology. Strategies United will issue a report this month showing that the global LED market reached a value of $14 billion in 2013, and the Freedonia Group forecasts that demand for lighting fixtures will reach $23.3 billion by 2016, with expected strong demand for LED fixtures in all lighting market segments.
The reason for the lightbulb switch is energy savings. The Department of Energy estimates that LED lighting could save 190 terrawatt hours of electricity per year by the year 2030. According to GE Lighting’s website, that translates into the equivalent output of 24 large (1,000 MW) power plants or power for 95 million homes. The estimated cost savings in today’s currency is in the neighborhood of $15 billion. (The GE Lighting website also has a nice short overview of how LEDs work.)
One technical obstacle facing LED light sources is the development of high-quality white light (pdf). A light-emitting diode, governed by the laws of physics, is essentially a monochromatic light source with a narrow wavelength spectrum. There are two ways to engineer a “white light” LED—combine red, green, and blue light in the right proportions, or convert the light using a phosphor. Conversion is achieved by shining blue or near-ultraviolet LED light on a yellow-emitting phosphor, such as cerium-doped yttrium aluminum garnet (Ce3+:YAG). Combining the blue and yellow gives white light, and commercial products exist using this approach.
However, a new Rapid Communications article in the Journal of the American Ceramic Society (login required) outlines some of the problems with current conversion technology, including degradation of epoxy resins that decrease transmittance and efficacy, refractive index of the epoxy leading to total internal reflection of white light and efficiency reduction, and that the “color temperature” of commercial white light LEDs is not warm (red) enough.
To address these problems, a Korea-based group of researchers from Pohang University of Science and Technology and Kongju National University embedded phosphors in glass frit instead of epoxy. The group mixed high refractive index, commercially available glass powders with Ce3+:YAG phosphors and cosintered the composites. They used a high lead content borosilicate composition: 50PbO–35B2O3–15SiO2 (mol %). The composition had the advantage of an index of refraction very close to that of the phosphor—1.8 and 1.83, respectively—which eliminated total internal reflection losses at the phosphor–matrix interface. Also, the composition had a low softening point. Researchers were interested in keeping processing temperatures low to prevent phosphor degradation, although the sintering temperature had to be higher than epoxy working temperatures.
The reported results are promising. The researchers noticed no chemical reaction between the phosphors and the glass matrix, and the phosphors did not degrade during sintering. The luminescent properties were as good or better than commercial, epoxy-based wavelength converters.
The group also experimented with improving the “color” of the white light, that is, making it more red or warmer. To do so, they added Eu3+ and Mn2+ to the glass frit in the forms of Eu2O3 and MnO, hoping to increase light emission in the 620–710 nm wavelength region. This approach proved successful, too, and they were able to reduce the white light “color temperature” from 7,000 K to about 4,000 K.
The authors immediately identified the inevitable technical challenge facing this proof-of-concept: “PbO [in the glass matrix] needs to be replaced by an environmentally safe component in the future.”
The paper is “Stable and color-tailorable white light from blue LEDs using color-converting phosphor–color composites,” by S. Yi, W.J. Chung, and J. Heo (DOI: 10.111/jace.12739).
Author
Eileen De Guire
CTT Categories
- Basic Science
- Energy
- Glass
- Optics