[Image above] An MIT team 3-D printed composite materials with precisely controlled structures and conducted tests in a drop tower that enabled them to observe exactly how cracks appeared and spread—or didn’t spread—in the first instants after impact. Credit: MIT
The ocean is a rich, vast resource—not just of water, diversity, and life, but of materials science inspiration, too.
For instance, Columbia University researchers recently took inspiration from oyster shells to develop a polymer nanocomposite with controllable self-assembly that makes the material stiff, deformable, and lightweight.
And New York University researchers turned to sea urchins, studying their sturdy spicule structure to learn how to build tunable fracture-resistant materials, such as dental composites and lightweight armor.
Plus, scientists are still discovering new creatures that may be future sources of materials science inspiration—such as this this carnivorous sponge species discovered off Canada’s North Atlantic coast that uses glass spikes to snag its dinner. Ouch.
If you’re familiar with Ceramic Tech Today, the plethora of oceanic inspiration will come as no surprise. I’ve written before about materials science research, discoveries, inventions, and technology inspired by sea sponges, fish scales, diatoms, chitons, limpets, oysters, and even penguin feathers.
It seems like I’m on an oceanic roll—so, let’s add another creature to that list, shall we?
Researchers at Massachusetts Institute of Technology (Cambridge, Mass.) have now taken inspiration from conch shells to develop a 3-D printing technique that can build composite materials with incredible toughness.
Conch shells are tough—10 times tougher than go-to-tough-biomaterial nacre (a.k.a. mother-of-pearl, and the subject of the oyster story linked above)—because they have a three-tiered architecture that contains layers of materials with opposing grain directions.
The opposing grain structure creates a maze-like matrix within the shell that prevents cracks from propagating by not providing them with a clear path to follow.
So to recreate that natural structure, the MIT team used additive manufacturing to develop a technology that replicates the conch’s shell structure. The 3-D printing technique deposits layers of polymer materials with opposing geometries—akin to the shell’s structure—to create a composite with layered organization.
Then, the scientists used simulations in combination with dynamic testing experiments in the lab to examine how cracks form and propagate within the material upon impact in a drop tower.
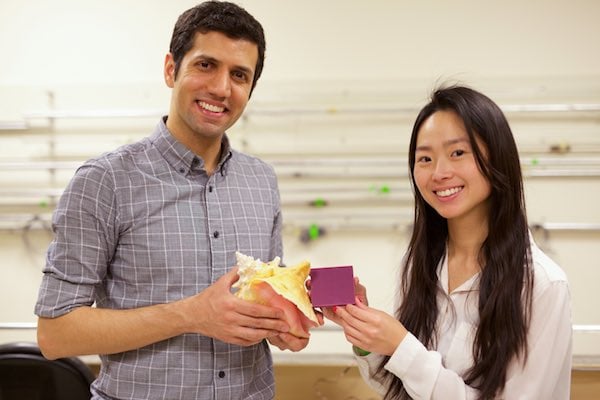
MIT graduate student Grace Gu (right) and postdoc Mahdi Takaffoli (left). Credit: Melanie Gonick; MIT
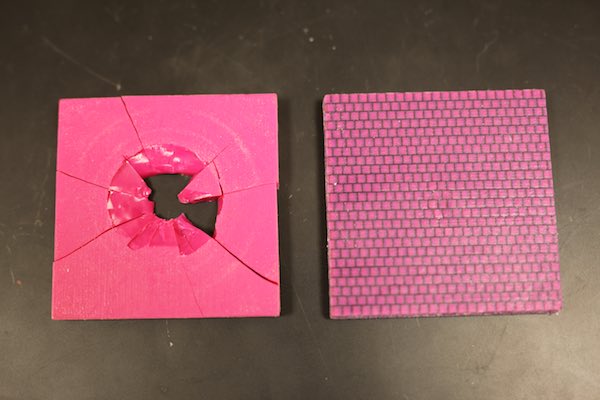
Testing proved that the geometry with the conch-like, criss-crossed features (right) was substantially better at preventing crack propagation. Credit: Melanie Gonick; MIT
“There was amazing agreement between the model and the experiments,” Markus Buehler, MIT McAfee Professor of Engineering and senior author of the new research, says in an MIT News story.
Just like in the conch’s naturally strong shell, opposing geometries were important for imparting the 3-D-printed material with strength.
“Testing proved that the geometry with the conch-like, criss-crossed features was 85% better at preventing crack propagation than the strongest base material, and 70% better than a traditional fiber composite arrangement,” Grace Gu, MIT graduate student and lead author of the research, adds in the MIT News story.
Hear more about this work in the short MIT video below.
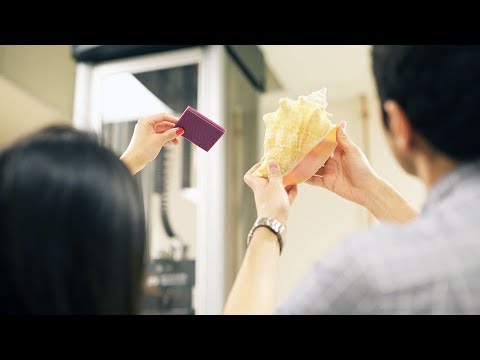
Credit: Massachusetts Institute of Technology; YouTube
For lightweight materials with such a high degree of toughness, body armor applications are a logical potential application for these additively structured polymeric materials.
“This has stiffness, like glass or ceramics,” Buehler says in the release. But integrating the layered structure makes the MIT team’s composites much less brittle than traditional glass or ceramic materials. And additively manufacturing with polymer composites comes at significantly lower costs that other types of materials.
Toughness and fracture resistance are really important criteria for body armor materials, but additional ballistic considerations include a material’s ability to resist penetration and its multi-hit capacity. Can a material stop high speed bullets before they penetrate? And how does the material stand up to an assault from multiple hits?
Polymer fibers have previously shown promise in body armor applications, but when it comes to stopping high-speed bullets, hard plates made of ceramic or metal still have offered the best protection. We’ll have to wait for more tests with these new layered composites to see how they fare in high-speed and multi-hit ballistic tests.
And although 3-D printing technologies are much more developed for polymers, we’ve seen big advancements in additive manufacturing of ceramics and glass recently—which could suggest that similar layered architectures might be able to be applied to such materials eventually as well.
The paper, published in Advanced Materials, is “Hierarchically enhanced impact resistance of bioinspired composites” (DOI: 10.1002/adma.201700060).
Interested in armor materials? Watch for the upcoming armor materials-themed August issue of the ACerS Bulletin in the next few weeks!
Author
April Gocha
CTT Categories
- Biomaterials & Medical
- Manufacturing
- Material Innovations
Spotlight Categories
- Member Highlights