[Image above] Glass containers could see a comeback in the face of backlash against single-use plastics. Credit: Andrew Seaman, Unsplash
If the COVID-19 pandemic has taught me anything, it is that things in the world can change much more quickly than I ever thought.
Of course, highly infectious and reasonably deadly disease has a way of spurring swift action. The coronavirus crisis, despite arguments about whether we are doing too much or too little, demonstrates that concerted and drastic action is most definitely possible. Which leaves me wondering—can we apply such prompt action to other looming challenges currently facing humanity?
Ever since I wrote the CTT article a year ago about massive challenges, falsehoods, and shifts in how materials are recycled, I’ve had our materials waste stream on my mind.
Despite the prevalence of public recycling bins and curbside recycling pickup in many communities, modern recycling in its present state is a materials dead end. The truth is that those empty vessels, whether we toss them in a recycling bin or not, generally do not find new life as other materials, products, or goods—they are finding their way to landfills, piling up, polluting the earth, and wasting resources.
A recent study by Greenpeace “found that out of 367 recycling recovery facilities surveyed none could process coffee pods, fewer than 15% accepted plastic clamshells—such as those used to package fruit, salad or baked goods—and only a tiny percentage took plates, cups, bags and trays,” according to an article on The Guardian.
Part of the problem is that some plastics labeled as recyclable really are so in theory more than in practice. Many of these materials are mixed plastics (numbers 3–7), which makes them difficult to process and repurpose into new materials and goods.
The Guardian article continues, “The report noted that recyclers often report ‘mixed plastics’ as having negative value—in other words, they cost money to get rid of. Additionally, it cited federal studies that have estimated that fewer than 5% of these products get reprocessed into new products.”
Although this situation is a problem for those tasked with getting rid of waste, there are signs manufacturers—those who produce the products and thus choose which packaging to sell those products in—are starting to take responsibility as well.
Major manufacturers are grappling with how to reduce plastic use to the avail of consumers and the planet alike. “Unilever plans to halve its use of virgin plastic by 2025, while Procter & Gamble Co. has pledged to do the same by 2030. Mars Inc. and PepsiCo. Inc. have similar plans,” according to a Wall Street Journal article.
Others are developing innovative solutions when it comes to recycling, creating new ways to repurpose discarded plastics into new uses, including recycling soft plastics and toner waste into asphalt additives and extracting polyester from mixed plastic recycling waste.
But perhaps a more effective strategy to curb the buildup of recyclable products going to waste is to move further away from the concept of disposable packaging altogether—instead opting for containers that can be reused and refilled instead of discarded.
One such solution I mentioned in that CTT article last year was an initiative called Loop, which seeks to return to a milkman-based model in which consumer goods are supplied in reusable packaging that is returned to the manufacturer for cleaning, refilling, and reuse.

A bag in which Loop containers are shipped to consumers. Credit: NowThis Future, YouTube
Loop uses container deposits that consumers pay when they purchase a product but then recoup when they return once empty, allowing the container to be reused again and again.
Loop’s first pilot program began in May 2019 in Paris and New York City and has since expanded to Massachusetts, Connecticut, Delaware, Vermont, and Rhode Island. California, the United Kingdom, Canada, Germany, and Japan are slated to soon get Loop service as well, in addition to Australia next year.
And, according to a Fast Company article, the program seems to be doing relatively well so far, although specific data are not available. “The tests have been successful enough that the system is now rapidly expanding and will soon launch in retail stores,” the article states. That includes partnerships with Walgreens and Kroger, among others.
“The response to Loop is a simple one: Let’s shift ownership of the package in the end back to the manufacturer. And as such, they treat it as an asset and they can start investing in the pack again,” Tom Szaky, CEO of Loop, says in the article.
Because the packaging is designed to be reused again and again, Loop’s products come in more durable, more aesthetically pleasing packaging. Most eschew plastic altogether, instead opting for metal or glass. Loop’s growing product list now includes hundreds of products, including spices, granola, nut butter, juice, and mouthwash supplied in refillable glass containers, and ice cream and dry goods packaged in stainless steel canisters.
It remains to be seen if Loop proves sustainable as a business model (currently, limited utilization and integration means prices are still high), but it seems that the issues with recycling plastic as well as plastic’s public status as an environmental enemy are translating into a growing opportunity for other materials in the packaging and container world.
One prime candidate, of course, is glass. Materially speaking, glass is quite favorable from a sustainability perspective—not only can glass containers be effectively sterilized for reuse, but the material itself can be recycled continuously to be formed and re-formed into new glass containers.
Which brings me to my second point—another effective strategy to curb the buildup of recyclable products going to waste is to improve recycling chains. As I mentioned, for some plastics that is difficult, but it might be less so for glass.
Glass once commanded a majority of the container market for various consumer products, such as soda, but has been supplanted by plastic in the past several decades because plastic is cheaper, lighter, and less likely to break.
“Today, just 1% of U.S. soda comes in glass bottles, down from nearly 58% in 1975, according to Beverage Marketing Corp., a consulting firm. Over the same period, plastic jumped to 32.5% from nothing,” according to an article from the Wall Street Journal.
That drop in demand has contributed to a decline in glass container manufacturing plants, with 65% less glass container plants in the U.S. today than there were in 1983, the article cites. However, there are some signs that glass containers are finding footing in the spaces where plastic once stood.
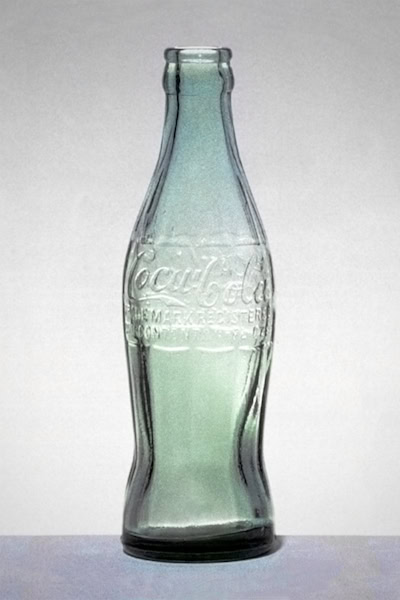
Coca-Cola debuted their iconic contoured glass bottle to the public in 1916. Now, most Coca-Cola products are sold in plastic bottles. Credit: nagualdesign, Wikimedia (CC0 1.0)
“The U.S.’s first new glass container plant in 12 years, a $123 million facility, is being built by Arglass Yamamura LLC in Georgia. Perrysburg, Ohio-based O-I, the world’s biggest maker of glass containers, is investing more than $60 million to build a new furnace at its French plant, its first such expansion in the region in two decades,” the Wall Street Journal article continues. “Glassmakers also are investing in new technology to quickly swap colors and molds in a bid to woo craft brewers and small brands, in a break from the long production runs that have dominated the industry to date.”
One remaining negative mark of glass containers is that, despite glass’s robust ability to be recycled, current recycling rates are low in some parts of the world. Glass recycling rate is 75% in the European Union and 95% in Sweden, but China and the U.S. lag way behind at closer to 33%, according to article published in the December 2019 issue of Food Technology.
As I wrote in the CTT article about recycling from last year, that is partially due to popularity and prevalence of single-stream recycling in the U.S., which makes it difficult to separate out a high-quality waste stream of glass for recycling.
So, that is one area the glass container industry is currently targeting, with glassmakers and even some municipalities even funding separate programs for consumers to recycle glass.
In some areas of Virginia, for example, glass is no longer accepted in single-stream curbside bins; residents instead are encouraged to collect and drop-off glass waste at specially designated drop-off sites.
“The glass is collected from a network of more than two dozen purple dumpsters and then taken to Fairfax County’s I-66 transfer station, where it is crushed by a gigantic glass crushing machine,” according to an article from public radio station WAMU. “Forbes says the crushed material is high quality—98% glass—and a completely different product than the mixed trash resulting from glass processed through single stream recycling systems.”
Once processed, the collected glass is then sold to companies to make new glass products. And while one might suspect that people are unlikely to go out of their way to separately collect and responsibly dispose of glass, the results of some of these programs show otherwise.
“In Virginia, officials say they were surprised by how quickly residents started using the glass drop off sites,” the WAMU article continues. “Since launching last year, the program has collected nearly 5 million pounds of glass, roughly 200,000 pounds per week.”
Of course, much more expansion and use of such efforts are required to reach those 75% glass recycling rates of the European Union, but the success of such efforts may point to potential solutions to help address this challenge. And, combined with efforts to reduce disposable packaging and increase container reuse, effective solutions are poised to make a difference—if they can just do so fast enough.
“There is an opportunity to capitalize on the backlash against single-use plastics, but it is very hard,” Nipesh Shah, CEO of Tampa-based Anchor Glass Container Corp., says in the Wall Street Journal article.
Author
April Gocha
CTT Categories
- Environment
- Glass
- Manufacturing