[Image above] Carbon nanofiber before and after undergoing pulsed laser annealing. NC State researchers used this technique to create diamonds at room temperature and pressure. Credit: Jay Narayan, North Carolina State University
Unless you are extremely lucky to witness a kimberlite eruption (or a cargo plane malfunction), chances are you will not randomly stumble upon diamonds lying strewn across the ground. That is because diamonds take very high temperatures and pressures to form, and thus form naturally at about 150 kilometers (90 miles) below Earth’s surface, in temperatures around 1,050°C (2,000°F).
The extreme temperature and pressure barrier to creating diamonds on Earth’s surface was broken in 1955 when General Electric announced their researcher Howard Tracy Hall created the first man-made diamond.
Though current machines used for creating lab diamonds are more refined than ones used in the 1950s, the two main methods for creating diamonds still require temperatures well above room temperature. The first method, high pressure, high temperature (HPHT), requires temperatures of 1,300-1,600°C (2,372-2,912°F) and pressures between 50 to 60 kbar. The other, newer method for diamond creation, chemical vapor deposition (CVD), requires significantly lower temperatures and pressures—700-1,000°C (1,292-1,832°F) and 30-300 torr (<0.0004 kbar)—but this environment is still well above average room temperature.
In 2015, North Carolina State University researchers successfully tackled the high-temperature requirement by using high-power nanosecond laser pulses to convert carbon into diamond at ambient temperature and pressure (we reported on this discovery in CTT). Key to their success was undercooling. They placed carbon thin films on a substrate of sapphire, glass, or plastic and then melted the films using nanosecond laser pulses, at which point they undercooled the liquid carbon and directed its solidification into diamond structures.
At the time, NC State University filed a provisional patent for the diamond creation technique, but the researchers were not done just yet. In January of this year, they published a new paper extending their research.
“Our earlier work was on conversion [of] carbon thin films into diamond or Q-carbon,” says Jagdish (Jay) Narayan, chair professor in the materials science and engineering department at NC State and corresponding author of the paper, in an email. “This breakthrough is focusing on conversion of carbon fibers and nanotubes into diamond fibers, which opens many more applications ranging from field emission frictionless motors to quantum sensing and computing.”
Unlike with carbon thin films, Narayan and his colleagues did not need substrates to ensure proper undercooling in carbon nanofibers and carbon nanotubes. “The sapphire, plastic, and glass substrates provide sufficient undercooling in the case of amorphous thin films of carbon,” say the researchers in the paper. “In the present case, the restriction of heat flow (1D) in [carbon nanotubes/carbon nanofibers] provides enough undercooling to cause the conversion.”
As such, “[t]hese nanofibers and nanotubes could be [placed] on any substrate for conversion into diamond,” Narayan adds.
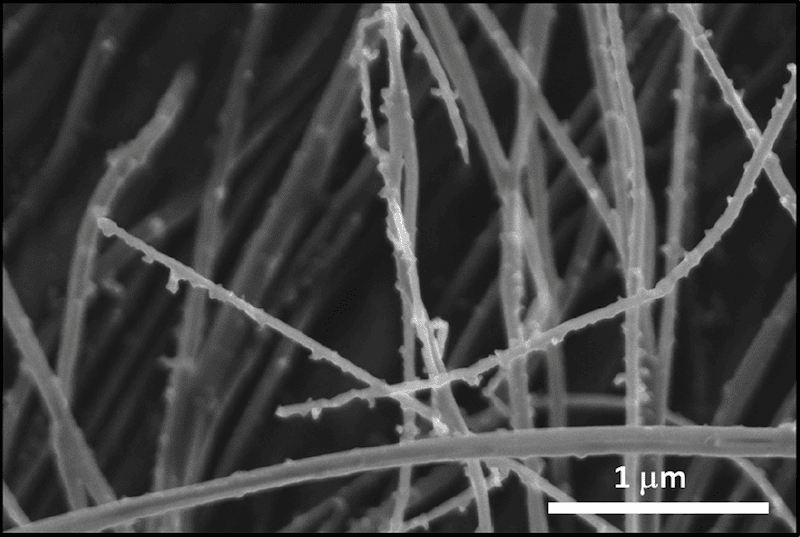
Depending on carbon nanofiber diameter, fibers either completely turned into diamond or only the surface became diamond. Credit: Jay Narayan, Nanoscale
After applying the laser pulse/undercool process to their carbon nanofibers and nanotubes, the researchers found each object responded similarly to the process. In both cases, the carbon-to-diamond conversion process started from the objects’ tips and then bent. The difference, though, between diamonds created from nanofibers and diamonds created from nanotubes was the diamond tips were considerably sharper for nanotube-created diamonds due to a smaller amount of available carbon. “Certain applications needing sharper ends will go [for] nanotubes,” Narayan explains.
Looking just at carbon nanofibers, the researchers discovered that below a critical diameter, the entire carbon fiber turned into diamond. Above that critical size, diamond nanocrystallites formed on the surface, some of which grew rapidly to form diamond nanorods. Compared to untreated carbon fibers, the laser-annealed fibers considerably enhanced diamond nucleation and growth. The researchers attributed this enhanced growth to nanodiamond nuclei formed during laser annealing, which provided effective nucleation sites.
While their method provides various advantages over current diamond-creation techniques, the researchers highlighted a more subtle advantage beyond just forgoing extreme temperature and pressure. “By controlling the nucleation and growth processes from the liquid, we can control the formation of defects and create diamond structures with fewer undesirable defects,” say the researchers in the paper. “This is a very important consideration in diamond as the defect annealing temperatures exceed 1700°C [3,092°F], above which high pressure is needed to stabilize the diamond and anneal out defects.”
What comes now? Currently, Narayan says they are conducting field emission studies to create more efficient frictionless motors and display devices. Additionally, NC State has filed a patent for this new method of processing diamond fibers.
The paper, published in Nanoscale, is “Direct conversion of carbon nanofibers and nanotubes into diamond nanofibers and the subsequent growth of large-sized diamonds” (DOI: 10.1039/C8NR08823C).
Author
Lisa McDonald
CTT Categories
- Material Innovations
- Nanomaterials