[Image above] General procedure for the preparation of polymer‐derived ceramics. Credit: Hotza et al., IJCES/Wiley (CC BY 4.0)
The processing of technical ceramics into fired parts is both an art and a science. Controlling the large number of variables for the raw materials and processing methods to match the final part specifications is difficult. More than adhering to formulations and schedules, processors must have the experience to adjust to unforeseen challenges that arise when mid-process benchmarks are not attained.
For example, wet processing methods such as slip casting, tape casting, and extrusion require precise control of the ceramic powders (e.g., composition, particle size distribution), solvents, dispersants, additives, and mixing protocols, among others, in order to attain the desired viscosity profile for the slurry. But due to the imprecision inherent in these items, the slurry may not be ideal even if the recipe was followed to the letter. Experienced operators then must adjust the slurry profile or the downstream processing in order to attain proper characteristics for the final part.
As with other industries, ceramics processors are experiencing both financial and environmental pressures to reduce their energy usage. A great deal of researchers are exploring ways to decrease firing temperatures and shorten firing cycles.
Polymer-derived ceramics (PDCs) have the potential to address these challenges and more. Whereas traditional forming begins with premanufactured ceramic powders, PDCs begin with preceramic polymers (PCPs) that are converted into ceramics by pyrolysis, which generally occurs at temperatures lower than those needed for sintering powders of the same materials. While PDCs can be formed using traditional wet processing methods, slurry processing for PCPs is often simpler than for powders.
As one might suppose, many of the traditional wet-processing steps must be adjusted to accommodate differences between traditional powder processing and processing of PDCs. A recent open-access article in the new International Journal of Ceramic Engineering and Science reviews the literature surrounding wet processing of preceramic polymers.
The literature view was conducted by researchers from two universities: Dachamir Hotza, Rafael Nishihora, and Ricardo Machado from the Federal University of Santa Catarina in Brazil; and Pierre-Marie Geffroy, Thierry Chartier, and Samuel Bernard from the University of Limoges in France. Though the researchers focus on tape casting, much of their discussion can be applied to other techniques including additive manufacturing through direct ink 3D printing.
There is much to read in their thorough treatment of the topic, including the ceramic systems investigated, the chemistry of the polymers, how fillers are used to control both processing and properties, slurry preparation and viscosity profile control, tape casting parameters, and firing parameters. While it is impossible to cover the depth and breadth of the article in this post, a number of items caught my attention.
PCPs require a shift of processing mindset
In traditional tape casting, the ceramic is formed by fusing together ceramic powder. With preceramic polymers, the ceramic is derived from polymer through chemical reactions.
The goal of traditional tape casting is uniform dispersion of fine ceramic powders within a polymeric binder system exhibiting appropriate viscosity. With preceramic polymers, the raw material is both product and binder, and the polymer/solvent systems have simpler viscosity profiles.
Firing of traditional vs preceramic tapes
Traditional tapes require removal of the binder before sintering. Because the parts are quite fragile at this stage, debinding and firing are often completed in one long heating profile. On the other hand, tapes (and other forms) made from preceramic polymers are cured by thermal crosslinking of the polymeric base into relatively stable structures. The ceramic is formed through pyrolysis, which is irreversible thermal decomposition usually performed in inert atmospheres.
Apply polymer processing techniques to PCPs
The authors describe how ceramists would do well to apply techniques from polymer processing to processing of PCPs. For example, due to the viscoelastic nature of PDCs (that builds during curing), mechanical properties are measured by dynamic shear as opposed to rotational shear viscometry.
Enhance properties with active fillers
Active fillers can be used with PDCs to enhance properties through chemical reactions during the curing and pyrolysis stages. The fillers for traditional tape casting are for the most part inert, though pore formers are removed through oxidation.
Controlling crystallinity
Upon pyrolysis, PDCs are often amorphous or have nanocrystals embedded in an amorphous matrix. Crystallinity can be controlled through post processing.
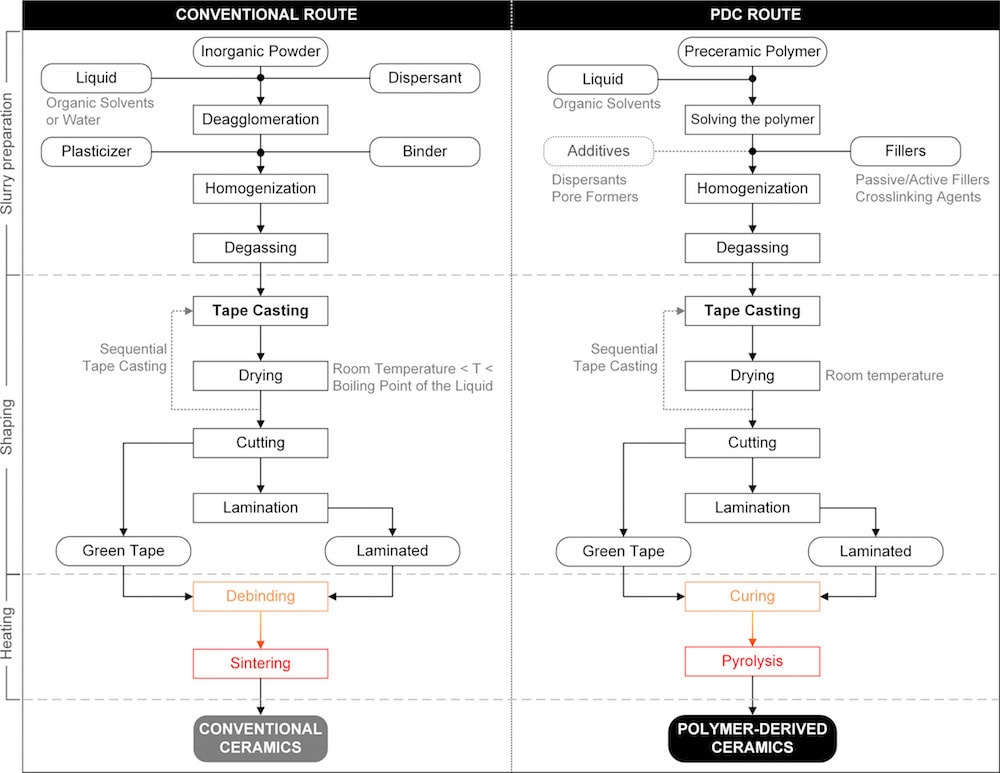
Flowchart of tape casting‐based shaping leading to either conventional or polymer‐derived ceramics. Credit: Hotza et al., IJCES/Wiley (CC BY 4.0)
The topic is rich in research possibilities to fill technological gaps for the tape casting of preceramic polymers. These include optimization of casting parameters through studies of viscoelasticity, microstructural evolution during curing and firing, and even how raw materials affect the final properties. And, because the review is published in ACerS’ new open-access journal, you can learn about these rich research possibilities for free!
The open-access paper, published in International Journal of Ceramic Engineering and Science, is “Tape casting of preceramic polymers toward advanced ceramics: A review” (DOI: 10.1002/ces2.10009).
Author
Jonathon Foreman
CTT Categories
- Manufacturing