[Image above] SEM image of glass foam with 10% borax and 5% NaOH, sintered for 15 minutes at 750°C. Credit: da Silva et al., International Journal of Applied Ceramic Technology
The ceramic and glass industry is resource intensive, using substantial amounts of energy and raw materials. Reducing resource usage would benefit both the environment and the bottom line. Thus, many research organizations are exploring various methods by which to achieve such reductions, for example, by lowering production temperatures and minimizing waste.
Many methods that research organizations are exploring are considered part of “the circular economy,” an economic system aimed at eliminating waste and promoting downstream use or recycling of resources.
At its topmost level, circular planners account for life cycles—production, use, and decommissioning of products after they cease to be useful. Decommissioning of products in particular is a substantial issue. For example, consider the cathode ray tube (CRT) industry. Have you tried recycling a CRT recently? A few years ago, I could give them to organizations that would find new users, often in developing nations. Today LCDs have firmly taken over the display market, and the amount of lead in CRTs make them difficult to recycle. Environmentally friendly disposal means paying recyclers, so many people opt for less friendly disposal means.
Producing new value-added products from waste and decommissioned materials is an advantageous method for extending the lifecycle of the raw materials of ceramics and glasses. Among the challenges for reuse are creating formulations from as-produced rather than raw materials and the instability of the supply quality (e.g., composition variations). The bottling and cement industries have reused reclaimed materials for years, and they learned to overcome these issues. Because recycling and reuse of technical ceramics and glasses is in the early stages, researchers have the luxury of focusing on formulation.
One area in which recycled ceramic and glass materials could make a large difference is in porous ceramics. Porous ceramics and glasses are a growing sector with applications in filtration, catalysis, healthcare, insulation, and more. Because porous ceramics can use ceramic and glass powders as starting materials, they hold great promise as value-added products for recycled and waste materials.
There are many methods for fabricating porous ceramics. Examples include sacrificial templating and gel casting. Glass foams, a type of porous ceramic, are often formed via sintering compacted glass powders that contain foaming agents. Two articles in the January/February 2020 issue of the International Journal of Applied Ceramic Technology (ACT, volume 17, issue 1) explore formulating waste and recycled glass into foams and the effects of parameter variations on porosity, density, and strength.
Foams are created when chemical reactions lead to gases forming within the material during sintering of powders. Closed porosity occurs when the bubbles are trapped, and open porosity occurs when the bubbles break and form interconnected tubes. While high strength of porous components is a universal need, other factors such as porosity (the fraction of pores), pore format (open or closed), and reactivity (inert, reactive or catalytic) are specific to each application. For example, filters need open porosity to allow fluid flow while insulation works better with closed porosity to prevent it.
Both articles use systematic variations in composition of the starting materials. They also explore the effects of processing parameters such as sintering temperature and time along with pressure used to compact the ingredients prior to sintering.
The first paper, authored by researchers at the Federal University of Technology (Ponta Grossa, Brazil) and the State University of Ponta Grossa (Brazil), offers an in-depth exploration of porosity and pore structures as functions of composition and processing parameters. The researchers used factorial design to uncover specific effects and interactions of these parameters. Their base material was commercial soda-lime float glass waste. Their additives were sodium hydroxide as the foaming agent and borax as a flow agent.
Of the factors tested, only sintering temperature and composition had significant effects on the density, porosity, and pore structures; mixing time, compaction pressure, and sintering time did not. Increasing the sodium hydroxide content increased overall porosity (lower density), with a higher fraction of open porosity and lower fraction of closed porosity. Likewise, increasing the sintering temperature had a similar effect.
Increasing the borax content decreased the viscosity of the glass, which in turn decreased the fraction of open porosity in the foam. This result is seemingly contradictory. However, with low sodium hydroxide content, closed porosity content remained steady while the density increased, indicating collapse of the open pores. At higher sodium hydroxide content, the closed porosity increased due to gas forming and being trapped within the thicker areas of the glass matrix.
Most significantly, this study shows that porosity and pore format can be tailored to meet the application requirements through formulation and sintering temperature.
The second paper, authored by researchers at the University of Aviero (Portugal) and Turnin Polytechnic University in Tashkent (Uzbekistan), used sodium-calcium-silicate sheet glass cullet as their main base material, similar in composition to the previous study. Additives included calcium aluminosilicate fabricated in the researchers’ labs, fly ash with a composition somewhat similar to the aluminosilicate, commercial silicon carbides, and two carbonates (commercial dolomite and calcite wastes) from a marble processing plant. This study also used CRT glass with calcite to explore the effects of processing conditions.
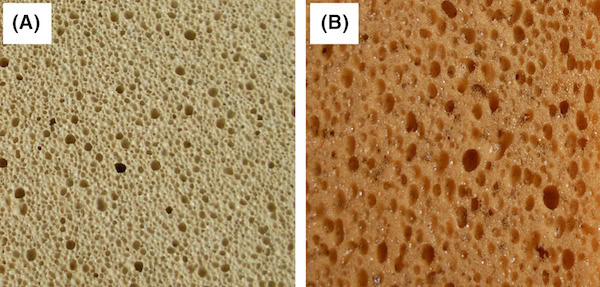
Glass foam (A) compared to a commercial kitchen cleaning sponge (B). Credit: Fernandes et al., International Journal of Applied Ceramic Technology
According to the researchers, the aluminosilicate seemingly strengthens the foam through forming crystals in the glass matrix. Additionally, fly ash appears to provide structural support similar to the aluminosilicate, and it also provides some degree of foaming due to its residual organic components. The bulk of the studies were performed using silicon carbide or carbonates along with the fly ash to achieve higher porosities.
For the foaming agents, silicon carbide requires relatively high temperatures (900–950˚C) for optimal foaming, while the carbonates provided the gas for foaming at 800–850˚C. There is a great deal of detail on the compositional effects. Interestingly, the finer silicon carbide (smaller particles) led to lower density (higher porosity) foams, presumably due to the higher surface area for oxidation.
Perhaps the most critical aspect of this work is the demonstration of foamed glasses from 100% waste or recycled materials had properties like those created from virgin stock.
The combined outcomes of these two papers show that fabricating commercially viable foamed glass products from recycled glass and other industrial waste streams is achievable.
Read more articles on the circular economy in the special issue of ACT and in Circular Economy Topical Collection on ACerS Publication Central at WileyOnline.
The first paper, published in International Journal of Applied Ceramic Technology, is “Glass foams produced by glass waste, sodium hydroxide, and borax with several pore structures using factorial designs” (DOI: 10.1111/ijac.13210).
The second paper, published in International Journal of Applied Ceramic Technology, is “Design and synthesis of foam glasses from recycled materials” (DOI: 10.1111/ijac.13393).
Author
Jonathon Foreman
CTT Categories
- Environment
- Glass